Technology Category
- Functional Applications - Manufacturing Execution Systems (MES)
- Processors & Edge Intelligence - Microcontrollers & Printed Circuit Boards
Applicable Industries
- Electronics
- Equipment & Machinery
Applicable Functions
- Product Research & Development
Use Cases
- Additive Manufacturing
- Manufacturing Process Simulation
Services
- Hardware Design & Engineering Services
About The Customer
Delkin Devices is a Poway, California-based company that has been manufacturing industrial storage products for over 24 years. It is one of the top 25 manufacturers in Southern California and serves some of the largest companies in the world. Delkin Devices has been a long-time user of Altium products, originally using PCAD before switching to Altium Designer in 2004. The company is committed to staying at the forefront of technology and continually seeks ways to improve its productivity and efficiency.
The Challenge
Delkin Devices, a leading manufacturer of industrial storage products, had been using Altium Designer 2004 for five years. However, as electronics design evolved, the software was no longer meeting their design needs. The team at Delkin Devices recognized the need for an upgrade to keep up with the changing demands of their industry. The challenge was to find a solution that would not only meet their current needs but also provide a platform for future growth and development. The solution needed to be easy to implement, with a minimal learning curve, and be able to handle their existing project files.
The Solution
Delkin Devices decided to upgrade to the latest version of Altium Designer. This new version provided productivity-enhancing features such as Design Rules Check, Differential Pair Routing, and the MCAD ECAD 3D Collaboration tool. These features were new to the designers but were provided in a familiar software application, minimizing the learning curve. The upgrade process was straightforward, and the team was able to open all their older project files, designs that were done years ago in either Tango or PCAD. The new Altium Designer also made board design quicker and easier, with improved Design Rule Checks (DRC) being the most significant time saver. The 3D MCAD ECAD design capabilities allowed for better collaboration with the mechanical team and fewer design iterations.
Operational Impact
Quantitative Benefit
Case Study missing?
Start adding your own!
Register with your work email and create a new case study profile for your business.
Related Case Studies.
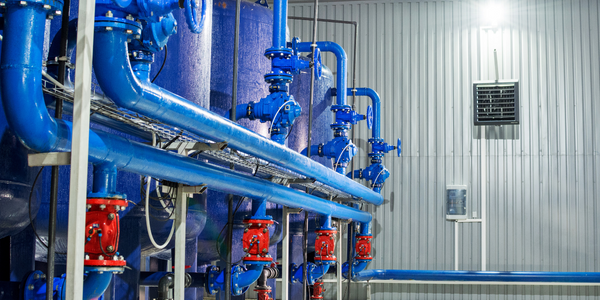
Case Study
Smart Water Filtration Systems
Before working with Ayla Networks, Ozner was already using cloud connectivity to identify and solve water-filtration system malfunctions as well as to monitor filter cartridges for replacements.But, in June 2015, Ozner executives talked with Ayla about how the company might further improve its water systems with IoT technology. They liked what they heard from Ayla, but the executives needed to be sure that Ayla’s Agile IoT Platform provided the security and reliability Ozner required.
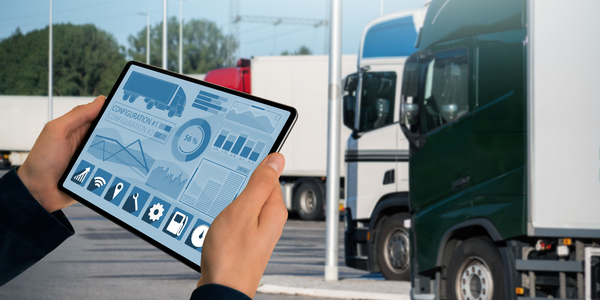
Case Study
IoT enabled Fleet Management with MindSphere
In view of growing competition, Gämmerler had a strong need to remain competitive via process optimization, reliability and gentle handling of printed products, even at highest press speeds. In addition, a digitalization initiative also included developing a key differentiation via data-driven services offers.
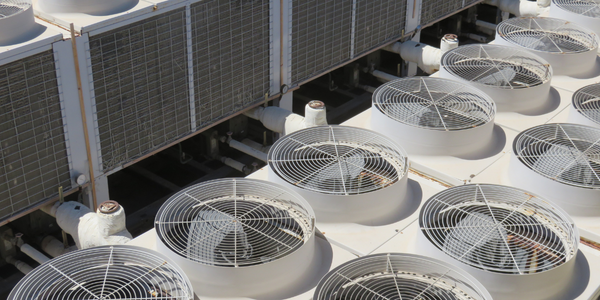
Case Study
Predictive Maintenance for Industrial Chillers
For global leaders in the industrial chiller manufacturing, reliability of the entire production process is of the utmost importance. Chillers are refrigeration systems that produce ice water to provide cooling for a process or industrial application. One of those leaders sought a way to respond to asset performance issues, even before they occur. The intelligence to guarantee maximum reliability of cooling devices is embedded (pre-alarming). A pre-alarming phase means that the cooling device still works, but symptoms may appear, telling manufacturers that a failure is likely to occur in the near future. Chillers who are not internet connected at that moment, provide little insight in this pre-alarming phase.
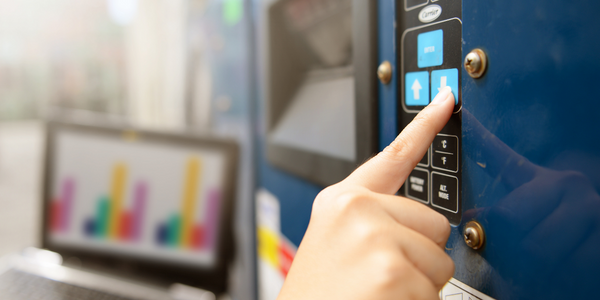
Case Study
Remote Temperature Monitoring of Perishable Goods Saves Money
RMONI was facing temperature monitoring challenges in a cold chain business. A cold chain must be established and maintained to ensure goods have been properly refrigerated during every step of the process, making temperature monitoring a critical business function. Manual registration practice can be very costly, labor intensive and prone to mistakes.
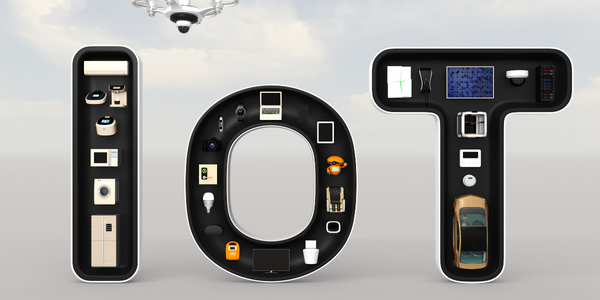
Case Study
Premium Appliance Producer Innovates with Internet of Everything
Sub-Zero faced the largest product launch in the company’s history:It wanted to launch 60 new products as scheduled while simultaneously opening a new “greenfield” production facility, yet still adhering to stringent quality requirements and manage issues from new supply-chain partners. A the same time, it wanted to increase staff productivity time and collaboration while reducing travel and costs.