Technology Category
- Infrastructure as a Service (IaaS) - Cloud Databases
- Robots - Wheeled Robots
Applicable Industries
- Automotive
- Finance & Insurance
Applicable Functions
- Field Services
- Maintenance
Use Cases
- Inventory Management
- Time Sensitive Networking
Services
- System Integration
About The Customer
Nwestco is a design, permit, construction, and maintenance company that has been offering turnkey project construction of petroleum equipment for over 25 years. The company also constructs car washes, automotive lifts, and fueling systems for regional airports. As Nwestco expanded its operations, adding branches in six different states, it outgrew its existing software setup. The company was using a combination of three different software solutions to manage its projects, but as it grew, it needed a more comprehensive system to handle its accounting, purchasing, project management, and service delivery.
The Challenge
Nwestco, a company specializing in the construction of petroleum equipment, car washes, automotive lifts, and fueling systems, was facing challenges with its software setup as it expanded its operations across six states. The company was using three different software solutions, including QuickBooks, an inventory management product, and a self-designed file maker program for service operations. However, these systems were proving insufficient to handle the company's growing needs in accounting, purchasing, project management, and service delivery. Furthermore, the company was seeking a cloud-based solution that didn't require internal hosting. The maintenance of these internal programs was also a challenge for the company's one-person IT team.
The Solution
Fieldpoint was chosen as the cloud-based solution that Nwestco needed. This move eliminated the need for the company's IT team to maintain the old systems and ensured the security of the new systems. Fieldpoint took over all of Nwestco’s field service needs, while NetSuite’s ERP and accounting system handled invoicing, billing, and customer information. This integration significantly reduced the time spent on producing invoices. Additionally, Nwestco implemented the Fieldpoint MobilePro field service application, which improved the efficiency of their technicians. The app allowed the company to track billable hours, send work orders directly to technicians, and automatically add work time to payroll timesheets, eliminating the need for double entry of information.
Operational Impact
Quantitative Benefit
Case Study missing?
Start adding your own!
Register with your work email and create a new case study profile for your business.
Related Case Studies.
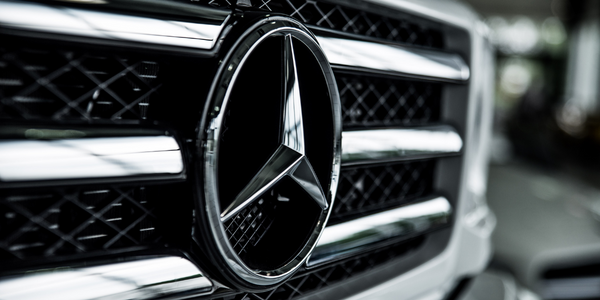
Case Study
Integral Plant Maintenance
Mercedes-Benz and his partner GAZ chose Siemens to be its maintenance partner at a new engine plant in Yaroslavl, Russia. The new plant offers a capacity to manufacture diesel engines for the Russian market, for locally produced Sprinter Classic. In addition to engines for the local market, the Yaroslavl plant will also produce spare parts. Mercedes-Benz Russia and his partner needed a service partner in order to ensure the operation of these lines in a maintenance partnership arrangement. The challenges included coordinating the entire maintenance management operation, in particular inspections, corrective and predictive maintenance activities, and the optimizing spare parts management. Siemens developed a customized maintenance solution that includes all electronic and mechanical maintenance activities (Integral Plant Maintenance).
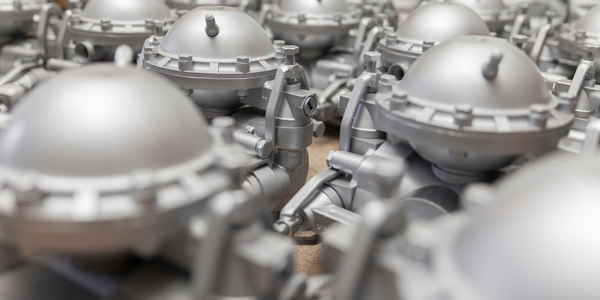
Case Study
Monitoring of Pressure Pumps in Automotive Industry
A large German/American producer of auto parts uses high-pressure pumps to deburr machined parts as a part of its production and quality check process. They decided to monitor these pumps to make sure they work properly and that they can see any indications leading to a potential failure before it affects their process.