Technology Category
- Platform as a Service (PaaS) - Application Development Platforms
- Robots - Wheeled Robots
Applicable Industries
- Equipment & Machinery
- Telecommunications
Applicable Functions
- Procurement
- Quality Assurance
Use Cases
- Personnel Tracking & Monitoring
- Visual Quality Detection
Services
- Testing & Certification
About The Customer
Frutas Bean is a Spain-based company specializing in the cultivation and commercialization of sweet fruits. Located in the Bajo Cinca region, it is one of the main exporters in the area. During peak production times, the company employs over 400 workers. Frutas Bean is committed to continuous product quality improvement, aiming to expand its market reach, particularly in Northern and Eastern Europe. The company faces challenges related to its dispersed workforce, many of whom lack internet access, leading to difficulties in maintaining control over work performance and product quality.
The Challenge
Frutas Bean, a leading exporter of sweet fruits in Spain, was facing challenges in maintaining product quality and competitiveness in the expanding horticultural market. The company's workforce was widely dispersed, often working in different locations each day, and many did not have access to the internet. This led to reliance on paper documentation for work reports and pesticide treatments, resulting in a lack of control over work performance in certain activities. The company was seeking a solution that could connect its employees, improve product quality control, and streamline its operations.
The Solution
ACBP, a consultancy firm, proposed a solution based on AuraQuantic and the implementation of mobile apps. AuraQuantic, with its user-friendly web format and easy integration with other platforms, could manage any process effectively. The mobile apps developed by ACBP could work both online and offline, solving the problem of internet access. They interacted with AuraQuantic to start processes and manage tasks. This combination of technologies automated the processes that manage work reports and pesticide treatments in situ, allowing employees to interact with company processes from their mobile devices. Several processes were implemented, including work report management, pesticide treatment management, quality control of collected and prepared fruit, and control of useful product life. All these processes were implemented in just four months.
Operational Impact
Quantitative Benefit
Case Study missing?
Start adding your own!
Register with your work email and create a new case study profile for your business.
Related Case Studies.
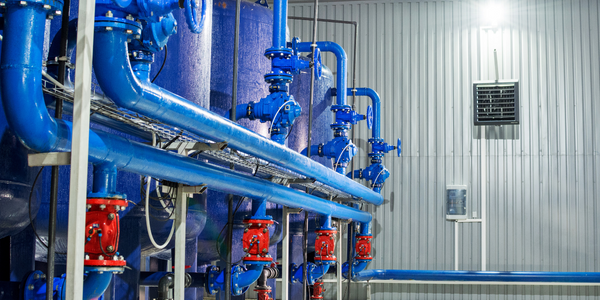
Case Study
Smart Water Filtration Systems
Before working with Ayla Networks, Ozner was already using cloud connectivity to identify and solve water-filtration system malfunctions as well as to monitor filter cartridges for replacements.But, in June 2015, Ozner executives talked with Ayla about how the company might further improve its water systems with IoT technology. They liked what they heard from Ayla, but the executives needed to be sure that Ayla’s Agile IoT Platform provided the security and reliability Ozner required.
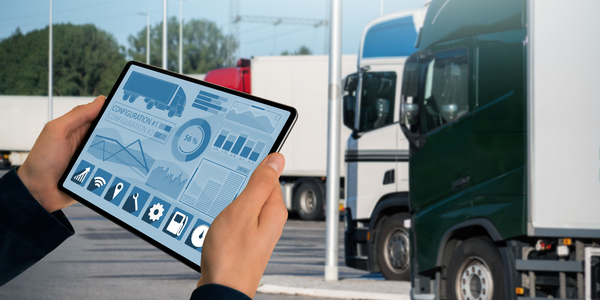
Case Study
IoT enabled Fleet Management with MindSphere
In view of growing competition, Gämmerler had a strong need to remain competitive via process optimization, reliability and gentle handling of printed products, even at highest press speeds. In addition, a digitalization initiative also included developing a key differentiation via data-driven services offers.
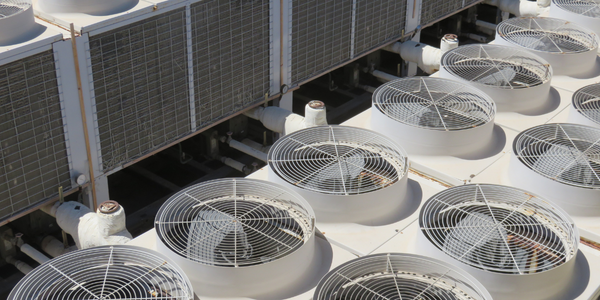
Case Study
Predictive Maintenance for Industrial Chillers
For global leaders in the industrial chiller manufacturing, reliability of the entire production process is of the utmost importance. Chillers are refrigeration systems that produce ice water to provide cooling for a process or industrial application. One of those leaders sought a way to respond to asset performance issues, even before they occur. The intelligence to guarantee maximum reliability of cooling devices is embedded (pre-alarming). A pre-alarming phase means that the cooling device still works, but symptoms may appear, telling manufacturers that a failure is likely to occur in the near future. Chillers who are not internet connected at that moment, provide little insight in this pre-alarming phase.
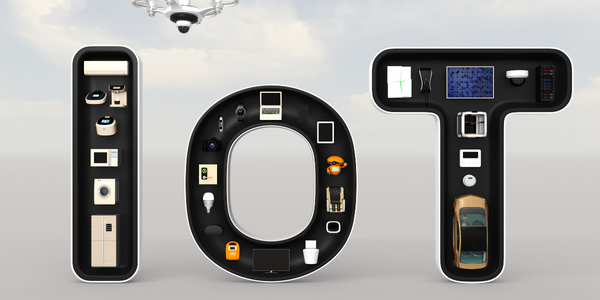
Case Study
Premium Appliance Producer Innovates with Internet of Everything
Sub-Zero faced the largest product launch in the company’s history:It wanted to launch 60 new products as scheduled while simultaneously opening a new “greenfield” production facility, yet still adhering to stringent quality requirements and manage issues from new supply-chain partners. A the same time, it wanted to increase staff productivity time and collaboration while reducing travel and costs.
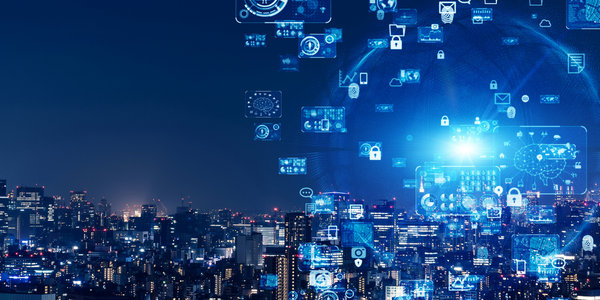
Case Study
Integration of PLC with IoT for Bosch Rexroth
The application arises from the need to monitor and anticipate the problems of one or more machines managed by a PLC. These problems, often resulting from the accumulation over time of small discrepancies, require, when they occur, ex post technical operations maintenance.
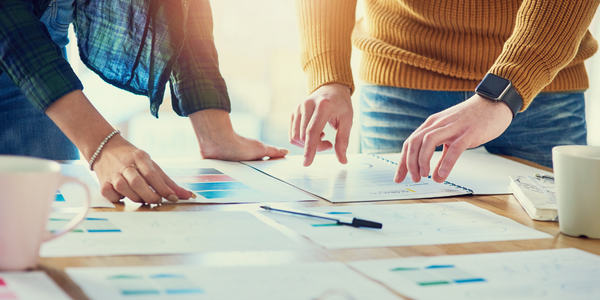
Case Study
Data Gathering Solution for Joy Global
Joy Global's existing business processes required customers to work through an unstable legacy system to collect mass volumes of data. With inadequate processes and tools, field level analytics were not sufficient to properly inform business decisions.