Customer Company Size
Large Corporate
Region
- Europe
Country
- Germany
Product
- DocuWare
- Microsoft Business Central
- BSS (Industry Solution for Building Services)
- NAPA3 (Payroll)
Tech Stack
- SQL server
Implementation Scale
- Enterprise-wide Deployment
Impact Metrics
- Productivity Improvements
- Cost Savings
Technology Category
- Application Infrastructure & Middleware - Data Exchange & Integration
- Functional Applications - Enterprise Resource Planning Systems (ERP)
Applicable Functions
- Human Resources
Use Cases
- Digital Thread
- Inventory Management
Services
- System Integration
- Software Design & Engineering Services
About The Customer
gepe Peterhoff is a German company that specializes in building management services, including cleaning, maintenance, security, and catering. The company has a history of over 60 years and generates a total of around 140 million euros. They pride themselves on providing high-quality services and well-thought-out concepts, which has earned them high-profile corporations as their longest-standing customers. Some of these customers have special demands due to cleanrooms that form part of their production facilities. Comprehensive cleaning in hospitals and retirement homes is another specialty of this family-owned business.
The Challenge
gepe Peterhoff, a German company specializing in building management services, was facing challenges with its document management. The company did not have a Document Management System (DMS), resulting in many documents such as orders being archived and managed decentrally at twelve locations. This lack of a centralized system made daily work processes less transparent and less efficient. The company sought a DMS that would streamline their operations and a solution partner who could understand their processes.
The Solution
To address their challenges, gepe Peterhoff implemented DocuWare, a proven, mature system with a strong workflow engine. The system was installed on-site, with all prerequisites in place on the hardware side along with a SQL server. The company launched DocuWare on June 1, 2020, introducing a new electronic invoice processing system. Invoices received by post are given a QR code, then scanned and stored in a DocuWare tray. Incoming email invoices are also transferred to this tray via Connect to Outlook. The company also achieved virtually complete automation for processing invoices from one of their largest suppliers. The range of applications of DocuWare is continuously being expanded, with an important area being the HR file cabinet, which is used intensively by the 15-person HR department.
Operational Impact
Quantitative Benefit
Case Study missing?
Start adding your own!
Register with your work email and create a new case study profile for your business.
Related Case Studies.
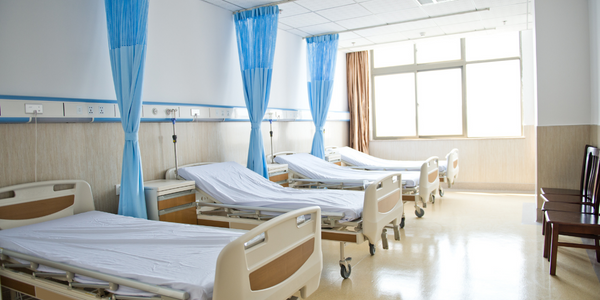
Case Study
Hospital Inventory Management
The hospital supply chain team is responsible for ensuring that the right medical supplies are readily available to clinicians when and where needed, and to do so in the most efficient manner possible. However, many of the systems and processes in use at the cancer center for supply chain management were not best suited to support these goals. Barcoding technology, a commonly used method for inventory management of medical supplies, is labor intensive, time consuming, does not provide real-time visibility into inventory levels and can be prone to error. Consequently, the lack of accurate and real-time visibility into inventory levels across multiple supply rooms in multiple hospital facilities creates additional inefficiency in the system causing over-ordering, hoarding, and wasted supplies. Other sources of waste and cost were also identified as candidates for improvement. Existing systems and processes did not provide adequate security for high-cost inventory within the hospital, which was another driver of cost. A lack of visibility into expiration dates for supplies resulted in supplies being wasted due to past expiry dates. Storage of supplies was also a key consideration given the location of the cancer center’s facilities in a dense urban setting, where space is always at a premium. In order to address the challenges outlined above, the hospital sought a solution that would provide real-time inventory information with high levels of accuracy, reduce the level of manual effort required and enable data driven decision making to ensure that the right supplies were readily available to clinicians in the right location at the right time.
-Testbed.png)
Case Study
IIC Industrial Digital Thread (IDT) Testbed
Field engineers and service teams often lack data and digital insights needed to assess, troubleshoot, and determine work scope for the large industrial assets in performing corrective and preventative maintenance activities. QA engineers many times need to understand why a particular problem in the part is happening recurrently or why parts from suppliers don’t stack up well in the assemblies due to mismatch. The root cause is usually hidden in design, manufacturing processes, supply chain logistics or production planning. But without the right data and digital insights, it's hard to pinpoint. GOAL To collect information in the design, manufacturing, service, supply-chain setup and provide access to and intelligent analytics for industrial manufacturing and performance data, to identify the root cause easier. Such insights can improve not only service and owner/operator productivity, but also provide critical feedback to the design engineering and manufacturing operations teams for continuous improvement.
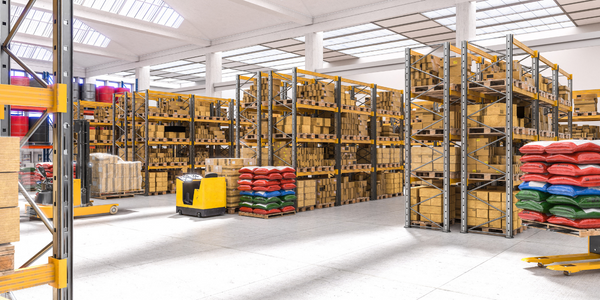
Case Study
Hardware Retailer Uses Data Warehouse to Track Inventory
Ace tracked which products retailers ordered, when they were ordered and shipped. However, the company could not track or forecast actual sales. Data used for reporting was up to a one-week old, owing to performance and data cleansing issues. Requirement to integrate wholesale and inventory data with POS data to help drive key business decisions, improve category management, lower inventory costs and optimize pricing. Reliance on custom coding to integrate POS data was excessively resource intensive and led to major performance constraints.
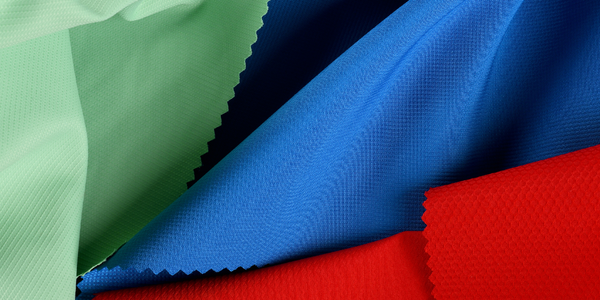
Case Study
Remake Enterprise-to-production System
The client was running a legacy material flow tracking system and wanted to replace the system with a more effective one as the system was increasingly expensive to maintain and support and also was not extendable. The client's IT landscape was filled with modern applications and it was difficult to interface the material flow tracking system with modern applications.