Customer Company Size
SME
Region
- Europe
Country
- Denmark
Product
- Zenoss
Tech Stack
- Atlassian Jira
- Zenoss ZenPack
Implementation Scale
- Enterprise-wide Deployment
Impact Metrics
- Productivity Improvements
- Customer Satisfaction
Technology Category
- Application Infrastructure & Middleware - API Integration & Management
Applicable Industries
- Healthcare & Hospitals
- Retail
Applicable Functions
- Business Operation
Use Cases
- Infrastructure Inspection
- Remote Asset Management
Services
- System Integration
- Software Design & Engineering Services
About The Customer
Netic A/S is a managed application operations service for public and private customers in Denmark. Founded in 2003, the company has since specialized in application operations, which involves monitoring the entire stack from bare metal to the application itself. Among its clients is Danish retailer JYSK, who sells beds, linens and furniture from 2,800 stores worldwide through their global e-commerce platform run and operated by Netic. Netic also uses Zenoss to monitor the performance of the application and its underlying infrastructure for MedCom, the Danish nationwide health network.
The Challenge
Netic A/S, a managed application operations service for public and private customers in Denmark, was founded in 2003 on the basis that IT operations could be done smarter and better than was typically the case. Since that time, Netic has become increasingly specialized in application operations, which involves monitoring the entire stack from bare metal to the application itself. For that reason, Netic was on the hunt for a solution that had to perform on a range of important parameters, including: Ability to handle monitoring across the entire stack, with a focus on infrastructure, Scalability, and Cost-effectiveness. As a managed service provider, Netic requires a monitoring platform that enables segregation of duties and is able to scale both horizontally and vertically. These issues meant that Netic struggled to efficiently provide top value for customers — and in a competitive environment, this can rapidly become critical. For that reason, a project was initiated to identify, test and onboard a new monitoring solution.
The Solution
Netic chose Zenoss to handle monitoring large parts of the infrastructure, supporting the applications that Netic operates for its clients. Zenoss was chosen as a result of a review that tested the key need of being able to monitor the end-to-end infrastructure. During the test, Netic evaluated Zenoss on the ability to integrate with the preferred project management and workflow tool, Atlassian Jira. Netic leveraged the Zenoss ZenPack architecture to easily build a seamless integration between Zenoss and Jira, including a dashboard that shows active incidents. After the evaluation period, Zenoss stood out as the strongest candidate and was chosen to replace Netic’s existing monitoring tools.
Operational Impact
Case Study missing?
Start adding your own!
Register with your work email and create a new case study profile for your business.
Related Case Studies.
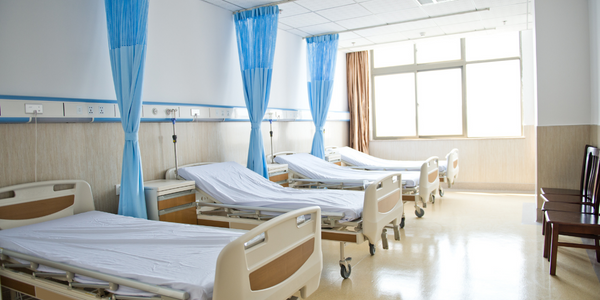
Case Study
Hospital Inventory Management
The hospital supply chain team is responsible for ensuring that the right medical supplies are readily available to clinicians when and where needed, and to do so in the most efficient manner possible. However, many of the systems and processes in use at the cancer center for supply chain management were not best suited to support these goals. Barcoding technology, a commonly used method for inventory management of medical supplies, is labor intensive, time consuming, does not provide real-time visibility into inventory levels and can be prone to error. Consequently, the lack of accurate and real-time visibility into inventory levels across multiple supply rooms in multiple hospital facilities creates additional inefficiency in the system causing over-ordering, hoarding, and wasted supplies. Other sources of waste and cost were also identified as candidates for improvement. Existing systems and processes did not provide adequate security for high-cost inventory within the hospital, which was another driver of cost. A lack of visibility into expiration dates for supplies resulted in supplies being wasted due to past expiry dates. Storage of supplies was also a key consideration given the location of the cancer center’s facilities in a dense urban setting, where space is always at a premium. In order to address the challenges outlined above, the hospital sought a solution that would provide real-time inventory information with high levels of accuracy, reduce the level of manual effort required and enable data driven decision making to ensure that the right supplies were readily available to clinicians in the right location at the right time.
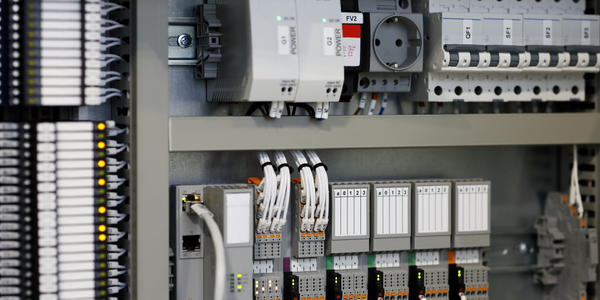
Case Study
Improving Production Line Efficiency with Ethernet Micro RTU Controller
Moxa was asked to provide a connectivity solution for one of the world's leading cosmetics companies. This multinational corporation, with retail presence in 130 countries, 23 global braches, and over 66,000 employees, sought to improve the efficiency of their production process by migrating from manual monitoring to an automatic productivity monitoring system. The production line was being monitored by ABB Real-TPI, a factory information system that offers data collection and analysis to improve plant efficiency. Due to software limitations, the customer needed an OPC server and a corresponding I/O solution to collect data from additional sensor devices for the Real-TPI system. The goal is to enable the factory information system to more thoroughly collect data from every corner of the production line. This will improve its ability to measure Overall Equipment Effectiveness (OEE) and translate into increased production efficiencies. System Requirements • Instant status updates while still consuming minimal bandwidth to relieve strain on limited factory networks • Interoperable with ABB Real-TPI • Small form factor appropriate for deployment where space is scarce • Remote software management and configuration to simplify operations
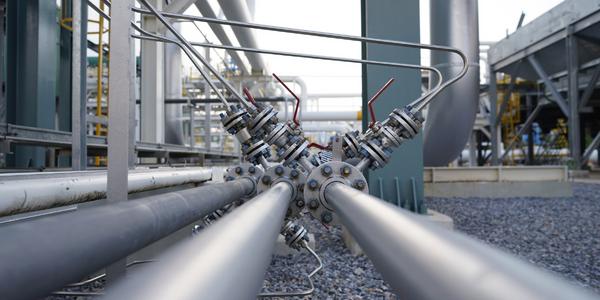
Case Study
Gas Pipeline Monitoring System for Hospitals
This system integrator focuses on providing centralized gas pipeline monitoring systems for hospitals. The service they provide makes it possible for hospitals to reduce both maintenance and labor costs. Since hospitals may not have an existing network suitable for this type of system, GPRS communication provides an easy and ready-to-use solution for remote, distributed monitoring systems System Requirements - GPRS communication - Seamless connection with SCADA software - Simple, front-end control capability - Expandable I/O channels - Combine AI, DI, and DO channels
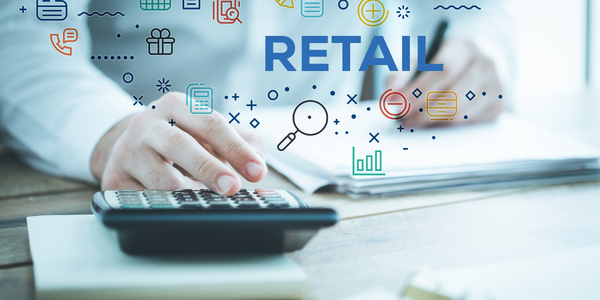
Case Study
Digital Retail Security Solutions
Sennco wanted to help its retail customers increase sales and profits by developing an innovative alarm system as opposed to conventional connected alarms that are permanently tethered to display products. These traditional security systems were cumbersome and intrusive to the customer shopping experience. Additionally, they provided no useful data or analytics.