HyperMesh and Custom Export Template Streamline CFD Analysis in Research Projects at Arizona State University
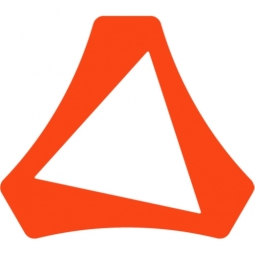
Technology Category
- Sensors - Infrared Sensors
- Sensors - Liquid Detection Sensors
Applicable Industries
- Aerospace
- Equipment & Machinery
Applicable Functions
- Logistics & Transportation
- Product Research & Development
Use Cases
- Mesh Networks
- Smart Campus
About The Customer
Arizona State University is an institution committed to excellence, access, and impact. It pursues research that contributes to the public good and assumes major responsibility for the economic, social, and cultural vitality of the communities that surround it. The School for Engineering of Matter Transport and Energy (SEMTE) at ASU encompasses mechanical, aerospace, materials, and chemical engineering. The Integrative Simulations & Computational Fluids Lab research group at SEMTE is strongly focused on developing and utilizing tools to investigate complex engineering and physical systems on massively parallel machines. They perform their research with the open-source computational fluid dynamics (CFD) solver Nek5000 which is used in a broad range of applications including thermal hydraulics of reactor cores, transition in vascular flows, atmospheric and ocean modeling, and combustion.
The Challenge
The Integrative Simulations & Computational Fluids Lab researchers at the School for Engineering of Matter Transport and Energy (SEMTE) at Arizona State University (ASU) were faced with the challenge of using the commercial code HyperMesh as a general preprocessor to mesh complex geometries for use with the spectral element CFD code Nek5000. The Nek5000 code requires 3D hexahedral elements, which posed a difficulty as most CFD tools use tetrahedral meshes that are easier to generate for conventional geometries. The researchers wanted to benefit from the rich functionality of advanced meshing tools like HyperMesh, capable of producing high-quality hexahedral meshes, while using the Nek5000 solver code. Before the project started, the researchers had no general process for meshing in place. Most of the meshing was handled with custom-made tools that were developed 15-20 years ago and have seen minimal updates since that time. Other users created their own meshing tool for specific problems in software such as MatLab.
The Solution
To overcome this challenge, the researchers at SEMTE set up a project to develop a converter tool that could export a mesh from the commercial code HyperMesh into a form that the Nek5000 code can use. They chose HyperMesh because of its solver-neutral functionality, outstanding documentation, and open architecture. The researchers started with very small problems that did not include more than five to ten elements and gradually worked through the development and debugging process to test it on larger domains. After weeks of intensive research and coding, they finalized the export template, creating a more user-friendly and less error-prone process. The converter tool starts by translating the nodal coordinates for each element from the native format within HyperMesh to the Nek5000 data structure. The users also supply the boundary conditions through HyperMesh and this data is converted to the Nek5000 format after the geometric conversion takes place. All of this data is then written to a file that can be fed into the Nek5000 solver. The engineers also added mid-side node support for the meshes to increase geometric flexibility and the converter automatically implements this information based off the element type used in HyperMesh.
Operational Impact
Case Study missing?
Start adding your own!
Register with your work email and create a new case study profile for your business.
Related Case Studies.
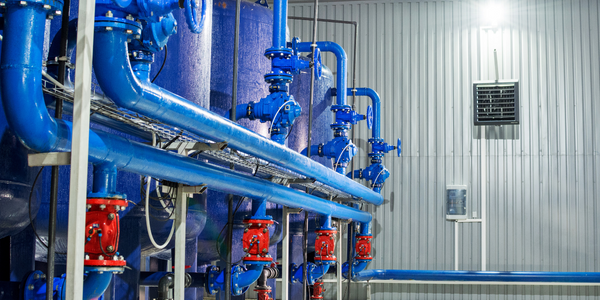
Case Study
Smart Water Filtration Systems
Before working with Ayla Networks, Ozner was already using cloud connectivity to identify and solve water-filtration system malfunctions as well as to monitor filter cartridges for replacements.But, in June 2015, Ozner executives talked with Ayla about how the company might further improve its water systems with IoT technology. They liked what they heard from Ayla, but the executives needed to be sure that Ayla’s Agile IoT Platform provided the security and reliability Ozner required.
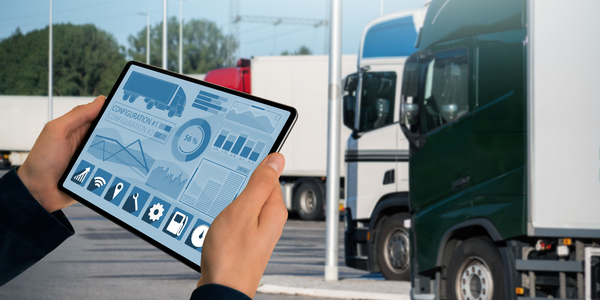
Case Study
IoT enabled Fleet Management with MindSphere
In view of growing competition, Gämmerler had a strong need to remain competitive via process optimization, reliability and gentle handling of printed products, even at highest press speeds. In addition, a digitalization initiative also included developing a key differentiation via data-driven services offers.
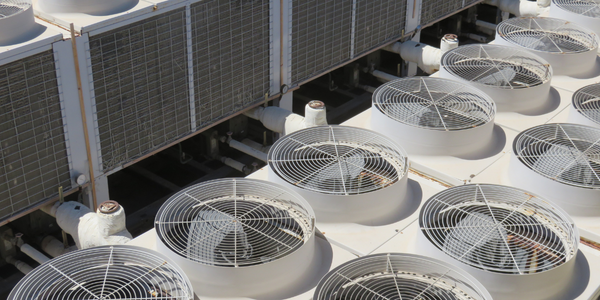
Case Study
Predictive Maintenance for Industrial Chillers
For global leaders in the industrial chiller manufacturing, reliability of the entire production process is of the utmost importance. Chillers are refrigeration systems that produce ice water to provide cooling for a process or industrial application. One of those leaders sought a way to respond to asset performance issues, even before they occur. The intelligence to guarantee maximum reliability of cooling devices is embedded (pre-alarming). A pre-alarming phase means that the cooling device still works, but symptoms may appear, telling manufacturers that a failure is likely to occur in the near future. Chillers who are not internet connected at that moment, provide little insight in this pre-alarming phase.
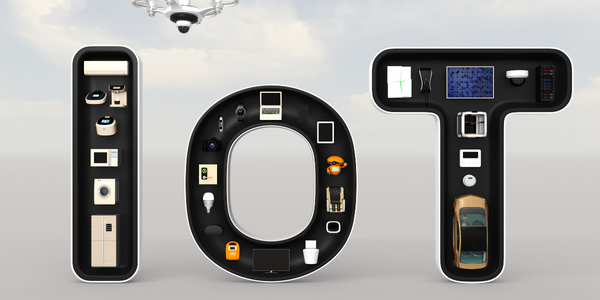
Case Study
Premium Appliance Producer Innovates with Internet of Everything
Sub-Zero faced the largest product launch in the company’s history:It wanted to launch 60 new products as scheduled while simultaneously opening a new “greenfield” production facility, yet still adhering to stringent quality requirements and manage issues from new supply-chain partners. A the same time, it wanted to increase staff productivity time and collaboration while reducing travel and costs.
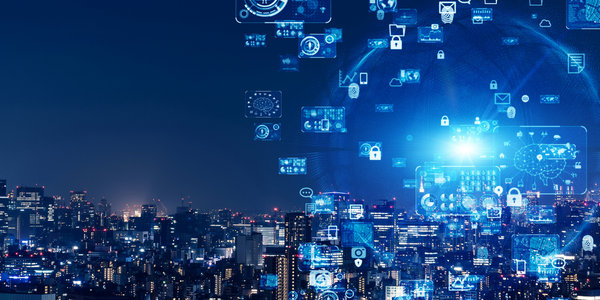
Case Study
Integration of PLC with IoT for Bosch Rexroth
The application arises from the need to monitor and anticipate the problems of one or more machines managed by a PLC. These problems, often resulting from the accumulation over time of small discrepancies, require, when they occur, ex post technical operations maintenance.
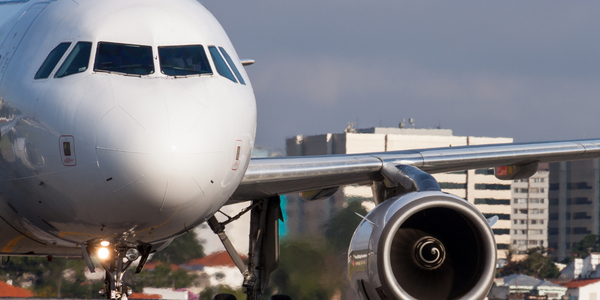
Case Study
Airbus Soars with Wearable Technology
Building an Airbus aircraft involves complex manufacturing processes consisting of thousands of moving parts. Speed and accuracy are critical to business and competitive advantage. Improvements in both would have high impact on Airbus’ bottom line. Airbus wanted to help operators reduce the complexity of assembling cabin seats and decrease the time required to complete this task.