Implementing an Economical, Ready-Made EHS Software Solution to Transform Program Performance and Mitigate Risks
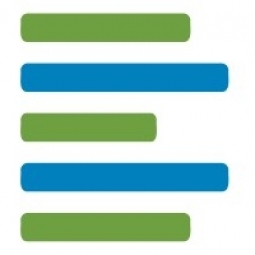
Customer Company Size
Large Corporate
Region
- America
- Asia
Country
- United States
Product
- Gensuite READY for EHS
Tech Stack
- Mobile Applications
- Cloud-based Software
Implementation Scale
- Departmental Deployment
Impact Metrics
- Productivity Improvements
- Waste Reduction
Technology Category
- Functional Applications - Remote Monitoring & Control Systems
Applicable Industries
- Automotive
Applicable Functions
- Discrete Manufacturing
- Quality Assurance
Use Cases
- Predictive Maintenance
- Factory Operations Visibility & Intelligence
Services
- Cloud Planning, Design & Implementation Services
- Training
About The Customer
The customer is an Asia-based automotive company that is publicly traded. They have manufacturing locations globally and are looking to manage EHS at a single, U.S.-based manufacturing site. The company has approximately 1,000 employees at this site. They were previously using a system that lacked built-in reporting features and were looking to digitize their compliance and management system. The company wanted to move away from paper-based employee concern reporting, transition from clipboard inspections to mobile inspections, and replace their excel method for tracking safety and environmental compliance.
The Challenge
The company, a publically traded, Asia-based automotive manufacturer with global manufacturing locations, was looking to manage EHS at a single, U.S.-based manufacturing site. They needed a holistic platform to address EHS compliance and management concerns that could easily be implemented with their ~1,000 employees. The company was particularly interested in built-in reporting features, something their previous system lacked. They were looking to digitize their compliance and management system, including moving away from paper-based employee concern reporting, transitioning from clipboard inspections to mobile inspections, and replacing their excel method for tracking safety and environmental compliance.
The Solution
The company implemented Gensuite READY for EHS, a pre-configured, compliance-centric solution perfect for single sites, smaller organizations or enterprises interested in pilot deployment that can launch in just 2 weeks. The system and application configurations are based on industry standard best practices and programs. It adheres to recurring permit or regulatory reporting obligations, tracks and follows up on incidents, conducts inspections efficiently with seamless mobile to desktop capabilities, and identifies incidents or concerns, assigns corrective actions, and drives actions to closure. The company was able to deploy Gensuite in a matter of weeks with a successful in-person training program for over 1,000 employees.
Operational Impact
Quantitative Benefit
Case Study missing?
Start adding your own!
Register with your work email and create a new case study profile for your business.
Related Case Studies.
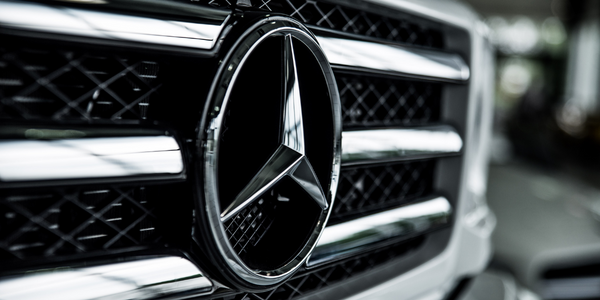
Case Study
Integral Plant Maintenance
Mercedes-Benz and his partner GAZ chose Siemens to be its maintenance partner at a new engine plant in Yaroslavl, Russia. The new plant offers a capacity to manufacture diesel engines for the Russian market, for locally produced Sprinter Classic. In addition to engines for the local market, the Yaroslavl plant will also produce spare parts. Mercedes-Benz Russia and his partner needed a service partner in order to ensure the operation of these lines in a maintenance partnership arrangement. The challenges included coordinating the entire maintenance management operation, in particular inspections, corrective and predictive maintenance activities, and the optimizing spare parts management. Siemens developed a customized maintenance solution that includes all electronic and mechanical maintenance activities (Integral Plant Maintenance).
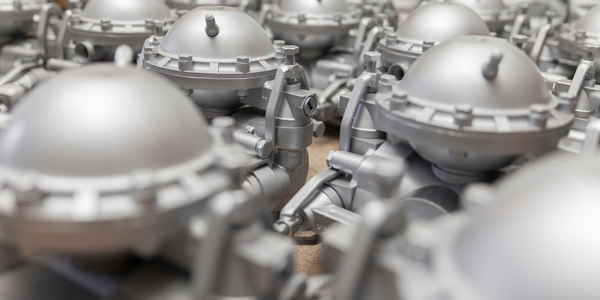
Case Study
Monitoring of Pressure Pumps in Automotive Industry
A large German/American producer of auto parts uses high-pressure pumps to deburr machined parts as a part of its production and quality check process. They decided to monitor these pumps to make sure they work properly and that they can see any indications leading to a potential failure before it affects their process.