Implementing an Economical, Ready-Made EHS Software Solution to Transform Program Performance and Mitigate Risks
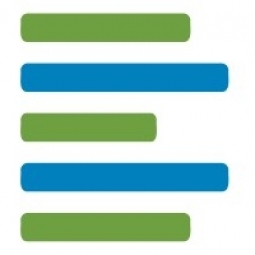
公司规模
Large Corporate
地区
- America
- Asia
国家
- United States
产品
- Gensuite READY for EHS
技术栈
- Mobile Applications
- Cloud-based Software
实施规模
- Departmental Deployment
影响指标
- Productivity Improvements
- Waste Reduction
技术
- 功能应用 - 远程监控系统
适用行业
- 汽车
适用功能
- 离散制造
- 质量保证
用例
- 预测性维护
- 工厂可见化与智能化
服务
- 云规划/设计/实施服务
- 培训
关于客户
The customer is an Asia-based automotive company that is publicly traded. They have manufacturing locations globally and are looking to manage EHS at a single, U.S.-based manufacturing site. The company has approximately 1,000 employees at this site. They were previously using a system that lacked built-in reporting features and were looking to digitize their compliance and management system. The company wanted to move away from paper-based employee concern reporting, transition from clipboard inspections to mobile inspections, and replace their excel method for tracking safety and environmental compliance.
挑战
The company, a publically traded, Asia-based automotive manufacturer with global manufacturing locations, was looking to manage EHS at a single, U.S.-based manufacturing site. They needed a holistic platform to address EHS compliance and management concerns that could easily be implemented with their ~1,000 employees. The company was particularly interested in built-in reporting features, something their previous system lacked. They were looking to digitize their compliance and management system, including moving away from paper-based employee concern reporting, transitioning from clipboard inspections to mobile inspections, and replacing their excel method for tracking safety and environmental compliance.
解决方案
The company implemented Gensuite READY for EHS, a pre-configured, compliance-centric solution perfect for single sites, smaller organizations or enterprises interested in pilot deployment that can launch in just 2 weeks. The system and application configurations are based on industry standard best practices and programs. It adheres to recurring permit or regulatory reporting obligations, tracks and follows up on incidents, conducts inspections efficiently with seamless mobile to desktop capabilities, and identifies incidents or concerns, assigns corrective actions, and drives actions to closure. The company was able to deploy Gensuite in a matter of weeks with a successful in-person training program for over 1,000 employees.
运营影响
数量效益
Case Study missing?
Start adding your own!
Register with your work email and create a new case study profile for your business.
相关案例.
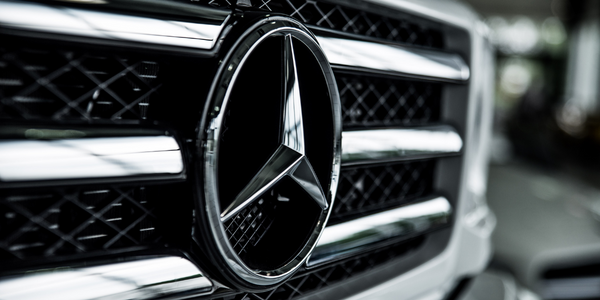
Case Study
Integral Plant Maintenance
Mercedes-Benz and his partner GAZ chose Siemens to be its maintenance partner at a new engine plant in Yaroslavl, Russia. The new plant offers a capacity to manufacture diesel engines for the Russian market, for locally produced Sprinter Classic. In addition to engines for the local market, the Yaroslavl plant will also produce spare parts. Mercedes-Benz Russia and his partner needed a service partner in order to ensure the operation of these lines in a maintenance partnership arrangement. The challenges included coordinating the entire maintenance management operation, in particular inspections, corrective and predictive maintenance activities, and the optimizing spare parts management. Siemens developed a customized maintenance solution that includes all electronic and mechanical maintenance activities (Integral Plant Maintenance).
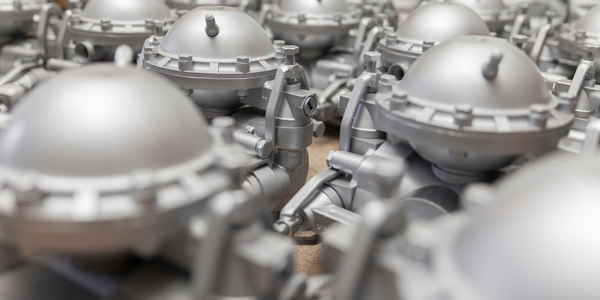
Case Study
Monitoring of Pressure Pumps in Automotive Industry
A large German/American producer of auto parts uses high-pressure pumps to deburr machined parts as a part of its production and quality check process. They decided to monitor these pumps to make sure they work properly and that they can see any indications leading to a potential failure before it affects their process.