Customer Company Size
Mid-size Company
Region
- Europe
Country
- Germany
Product
- DocuWare
- SAP R3 EHP7
- MS Outlook
- Fujitsu fi-7160 scanners
Tech Stack
- DMS
- ERP
Implementation Scale
- Enterprise-wide Deployment
Impact Metrics
- Productivity Improvements
- Cost Savings
Technology Category
- Application Infrastructure & Middleware - Data Exchange & Integration
- Functional Applications - Enterprise Resource Planning Systems (ERP)
Applicable Functions
- Procurement
- Human Resources
Use Cases
- Supply Chain Visibility
- Inventory Management
Services
- System Integration
- Cloud Planning, Design & Implementation Services
About The Customer
The KLEiN Group is a leading sheet metal manufacturer in Europe, specializing in products with complex requirements that international competitors do not have the expertise to make. In addition to mass-produced components, KLEiN also supplies customers with highly specialized tools. About 75 percent of their business comes from the automotive industry. For example, Adient, one of the largest car seat manufacturers in the world, uses KLEiN products. Renowned appliance manufacturers such as Miele and Vaillant are also part of their customer base. The company operates at two locations 500 kilometers apart and has an in-house IT team.
The Challenge
KLEiN Umformtechnik, a leading sheet metal manufacturer in Europe, was facing challenges in managing its administrative processes. The company specializes in products with complex requirements that international competitors do not have the expertise to make. In addition to mass-produced components, KLEiN also supplies customers with highly specialized tools. About 75 percent of their business comes from the automotive industry. Renowned appliance manufacturers such as Miele and Vaillant are also part of their customer base. In 2018, the company's management team decided to modernize all of its administrative processes. An important goal for introducing the DMS was to support their distributed workforce at two locations 500 kilometers apart. The company needed a solution that could automate processes, reduce search times, and increase transparency.
The Solution
KLEiN decided to use a DocuWare on-premises solution due to their existing IT infrastructure and in-house IT team. Several Fujitsu fi-7160 scanners were purchased for scanning paper documents. The implementation of the DMS began in the Purchasing department on January 1, 2020. All procurement processes needed to run smoothly – from ordering office supplies to machine parts – at both locations. This was often cumbersome and error-prone pre-DMS, when paper documents had to be searched for in file cabinets and then shared or transferred between office locations. Today, this is all handled with a tremendous degree of transparency in the DMS. Employees who are authorized users have all the data available immediately allowing them to seamlessly complete any task. KLEiN works with SAP as their ERP system, in version R3 EHP7. Providing an interface between SAP and DocuWare was a “must-have.” Automatic filing of documents generated by the SAP system increases efficiency as well as the security of their processes.
Operational Impact
Case Study missing?
Start adding your own!
Register with your work email and create a new case study profile for your business.
Related Case Studies.
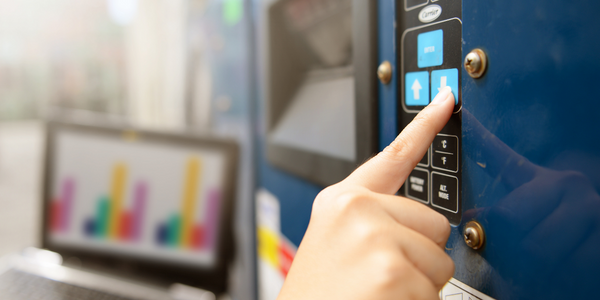
Case Study
Remote Temperature Monitoring of Perishable Goods Saves Money
RMONI was facing temperature monitoring challenges in a cold chain business. A cold chain must be established and maintained to ensure goods have been properly refrigerated during every step of the process, making temperature monitoring a critical business function. Manual registration practice can be very costly, labor intensive and prone to mistakes.
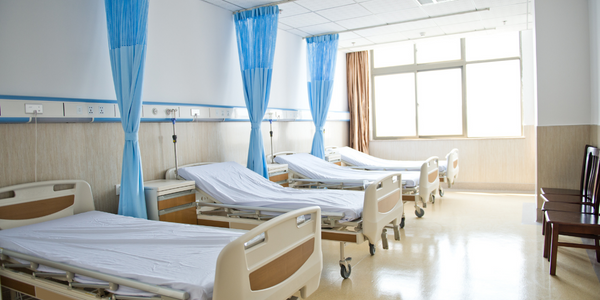
Case Study
Hospital Inventory Management
The hospital supply chain team is responsible for ensuring that the right medical supplies are readily available to clinicians when and where needed, and to do so in the most efficient manner possible. However, many of the systems and processes in use at the cancer center for supply chain management were not best suited to support these goals. Barcoding technology, a commonly used method for inventory management of medical supplies, is labor intensive, time consuming, does not provide real-time visibility into inventory levels and can be prone to error. Consequently, the lack of accurate and real-time visibility into inventory levels across multiple supply rooms in multiple hospital facilities creates additional inefficiency in the system causing over-ordering, hoarding, and wasted supplies. Other sources of waste and cost were also identified as candidates for improvement. Existing systems and processes did not provide adequate security for high-cost inventory within the hospital, which was another driver of cost. A lack of visibility into expiration dates for supplies resulted in supplies being wasted due to past expiry dates. Storage of supplies was also a key consideration given the location of the cancer center’s facilities in a dense urban setting, where space is always at a premium. In order to address the challenges outlined above, the hospital sought a solution that would provide real-time inventory information with high levels of accuracy, reduce the level of manual effort required and enable data driven decision making to ensure that the right supplies were readily available to clinicians in the right location at the right time.