Customer Company Size
Mid-size Company
Region
- America
Country
- United States
Product
- DocuWare
Tech Stack
- Enterprise Resource Planning system
Implementation Scale
- Departmental Deployment
Impact Metrics
- Productivity Improvements
- Waste Reduction
Technology Category
- Functional Applications - Enterprise Resource Planning Systems (ERP)
Applicable Functions
- Business Operation
Use Cases
- Inventory Management
Services
- System Integration
About The Customer
Lawrence Paper Company is one of the oldest box companies west of the Mississippi. It is a family-owned business that was established in 1882. The company has about 215 employees at its Kansas location. Lawrence Paper Company produces a variety of boxes and packaging materials, ranging from simple brown boxes to items large enough to hold auto parts. The company serves about 2,000 customers ranging from pet food producers to beer brewers, from industrial to retail, and from manufacturing to the automotive industry. Last year, it made enough corrugated sheets to circumnavigate the globe.
The Challenge
Lawrence Paper Company, a family-owned business established in 1882, produces a variety of boxes and packaging materials. With about 215 employees at its Kansas location, the company serves about 2,000 customers ranging from pet food producers to beer brewers, from industrial to retail, and from manufacturing to the automotive industry. However, the company was facing challenges with its record-keeping process. The volume of work required precise record-keeping, which used to generate a lot of paper. The company had been doing things the same way for 30 to 40 years, with a lot of paper pushing between different departments. They were looking for a way to be more efficient.
The Solution
Lawrence Paper Company decided to implement DocuWare, a digital document management system, to improve its record-keeping process. The company installed DocuWare about three years ago, starting with the Accounting Department. Digitizing immediately brought benefits. DocuWare also improved workflow and made operations more efficient. Prior to DocuWare, when an employee made a purchase, they would initiate a paper trail. A paper-based purchase order would circulate between seven different people and then was stored in a file cabinet. DocuWare made it much more time effective and easier to reconcile in the company’s Enterprise Resource Planning system and streamline the work of the Accounts Payable team.
Operational Impact
Quantitative Benefit
Case Study missing?
Start adding your own!
Register with your work email and create a new case study profile for your business.
Related Case Studies.
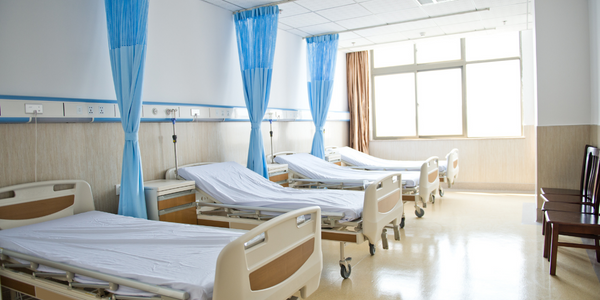
Case Study
Hospital Inventory Management
The hospital supply chain team is responsible for ensuring that the right medical supplies are readily available to clinicians when and where needed, and to do so in the most efficient manner possible. However, many of the systems and processes in use at the cancer center for supply chain management were not best suited to support these goals. Barcoding technology, a commonly used method for inventory management of medical supplies, is labor intensive, time consuming, does not provide real-time visibility into inventory levels and can be prone to error. Consequently, the lack of accurate and real-time visibility into inventory levels across multiple supply rooms in multiple hospital facilities creates additional inefficiency in the system causing over-ordering, hoarding, and wasted supplies. Other sources of waste and cost were also identified as candidates for improvement. Existing systems and processes did not provide adequate security for high-cost inventory within the hospital, which was another driver of cost. A lack of visibility into expiration dates for supplies resulted in supplies being wasted due to past expiry dates. Storage of supplies was also a key consideration given the location of the cancer center’s facilities in a dense urban setting, where space is always at a premium. In order to address the challenges outlined above, the hospital sought a solution that would provide real-time inventory information with high levels of accuracy, reduce the level of manual effort required and enable data driven decision making to ensure that the right supplies were readily available to clinicians in the right location at the right time.
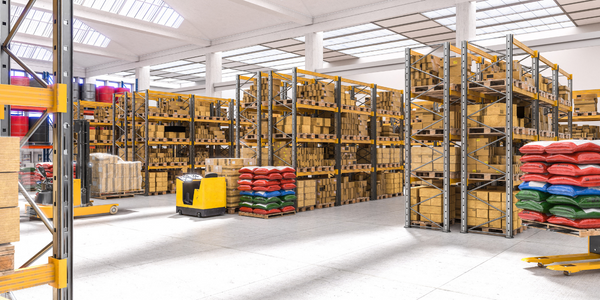
Case Study
Hardware Retailer Uses Data Warehouse to Track Inventory
Ace tracked which products retailers ordered, when they were ordered and shipped. However, the company could not track or forecast actual sales. Data used for reporting was up to a one-week old, owing to performance and data cleansing issues. Requirement to integrate wholesale and inventory data with POS data to help drive key business decisions, improve category management, lower inventory costs and optimize pricing. Reliance on custom coding to integrate POS data was excessively resource intensive and led to major performance constraints.
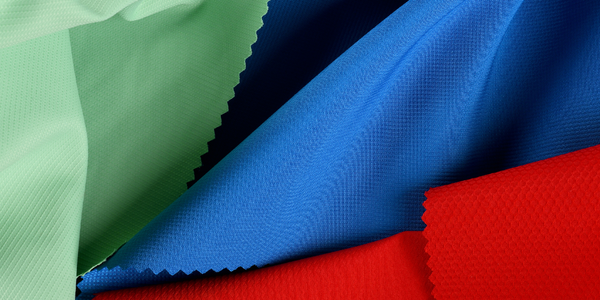
Case Study
Remake Enterprise-to-production System
The client was running a legacy material flow tracking system and wanted to replace the system with a more effective one as the system was increasingly expensive to maintain and support and also was not extendable. The client's IT landscape was filled with modern applications and it was difficult to interface the material flow tracking system with modern applications.
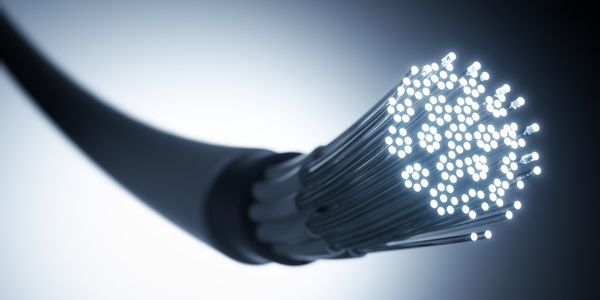
Case Study
Expertech - Capital Tool Inventory
Costly tools used to splice fiber optic cables are an important part of Expertech’s operational and capitalized expenses, but the company did not have an automated system in place to track their tools and optimize their usage. The existing data in its tracking system was inaccurate and required manual updating, making it essential for the company to implement an efficient process to track and follow up on its capital tool inventory.