Technology Category
- Analytics & Modeling - Digital Twin / Simulation
- Sensors - Infrared Sensors
Applicable Industries
- Automotive
- Equipment & Machinery
Applicable Functions
- Product Research & Development
- Quality Assurance
Use Cases
- Virtual Training
- Visual Quality Detection
Services
- Testing & Certification
- Training
About The Customer
Mando Softtech India Private Limited, incorporated in 2005, is a subsidiary of Mando Corporation, South Korea, which holds 100% of the share capital of the company. Mando Corporation, established in 1962, is the leading manufacturer of automotive component systems in Korea with an annual turnover of USD 5.3 billion in 2013 and 10,500 employees. The major shareholder of Mando is Halla corporation. Mando Softtech India started providing services from January 2006 onwards. The company manufactures automotive components such as brake systems, steering systems, suspension systems, and advanced driver assistance systems.
The Challenge
Mando Softtech India, a leading manufacturer of automotive component systems, faced significant challenges in maintaining the high performance and quality standards of their products. The company needed to conduct in-depth analysis of their product designs to identify and rectify even the smallest design errors early in the design cycle. The automotive industry being highly competitive and price sensitive, it was crucial for Mando India to compress their design and development cycle time and develop products with utmost cost efficiency without compromising on quality. The company had invested heavily in setting up the right infrastructure in-house with advanced product design, analysis, and simulation tools. However, they faced complex problems such as conducting accurate Hexameshing, generating 2D Meshing and 3D Meshing, and conducting Thermal simulation for ECU casing development. They were also struggling with Tetra and Volume tetra meshing and needed a reliable tool for structural and non-linear analysis.
The Solution
Mando Softtech India invested in Altair HyperWorks, starting with HyperMesh in 2008. After evaluating the capabilities, potential, and reliability of the results generated by the software, they decided to invest more in HyperWorks units. The quality of output and performance standards of Altair FEA solution helped Mando Softtech India conduct 3D Meshing to their utmost satisfaction. They used AcuSolve for thermal simulation of the development of ECU casing, RADIOSS solver for high quality structural and non-linear analysis, and OptiStruct solver for weight and shape optimization of a bracket. Mando Softtech India also started using Simlab solution for Tetra Meshing, which saved them considerable time and improved the result quality. Over the years, the use of Altair solutions at Mando Softtech India evolved from using only the pre-processing tools to using solvers such as AcuSolve, RADIOSS and OptiSturct for thermal analysis, structural analysis, and product design optimization.
Operational Impact
Quantitative Benefit
Case Study missing?
Start adding your own!
Register with your work email and create a new case study profile for your business.
Related Case Studies.
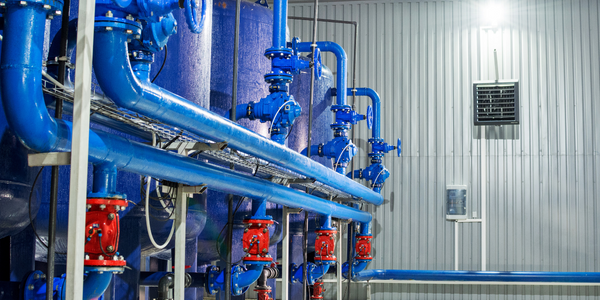
Case Study
Smart Water Filtration Systems
Before working with Ayla Networks, Ozner was already using cloud connectivity to identify and solve water-filtration system malfunctions as well as to monitor filter cartridges for replacements.But, in June 2015, Ozner executives talked with Ayla about how the company might further improve its water systems with IoT technology. They liked what they heard from Ayla, but the executives needed to be sure that Ayla’s Agile IoT Platform provided the security and reliability Ozner required.
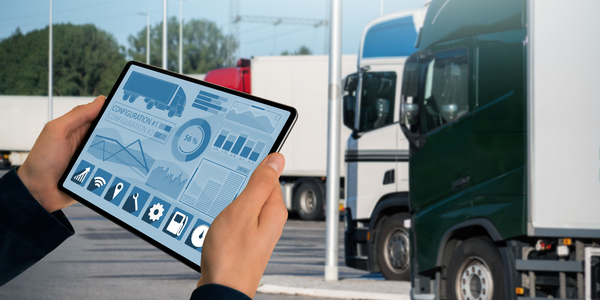
Case Study
IoT enabled Fleet Management with MindSphere
In view of growing competition, Gämmerler had a strong need to remain competitive via process optimization, reliability and gentle handling of printed products, even at highest press speeds. In addition, a digitalization initiative also included developing a key differentiation via data-driven services offers.
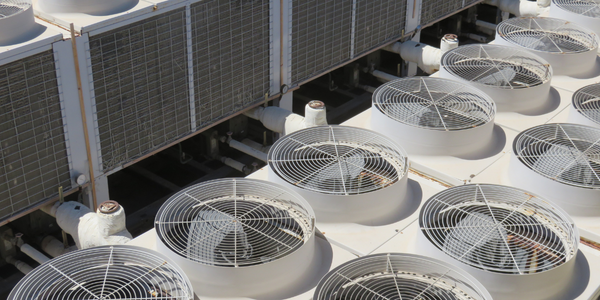
Case Study
Predictive Maintenance for Industrial Chillers
For global leaders in the industrial chiller manufacturing, reliability of the entire production process is of the utmost importance. Chillers are refrigeration systems that produce ice water to provide cooling for a process or industrial application. One of those leaders sought a way to respond to asset performance issues, even before they occur. The intelligence to guarantee maximum reliability of cooling devices is embedded (pre-alarming). A pre-alarming phase means that the cooling device still works, but symptoms may appear, telling manufacturers that a failure is likely to occur in the near future. Chillers who are not internet connected at that moment, provide little insight in this pre-alarming phase.
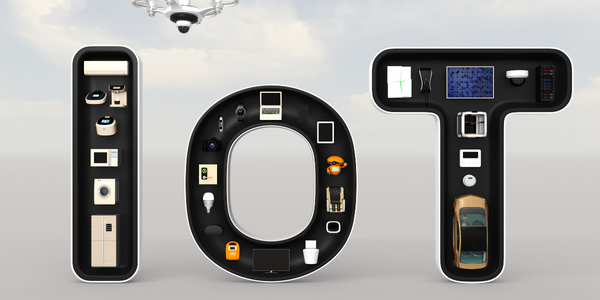
Case Study
Premium Appliance Producer Innovates with Internet of Everything
Sub-Zero faced the largest product launch in the company’s history:It wanted to launch 60 new products as scheduled while simultaneously opening a new “greenfield” production facility, yet still adhering to stringent quality requirements and manage issues from new supply-chain partners. A the same time, it wanted to increase staff productivity time and collaboration while reducing travel and costs.
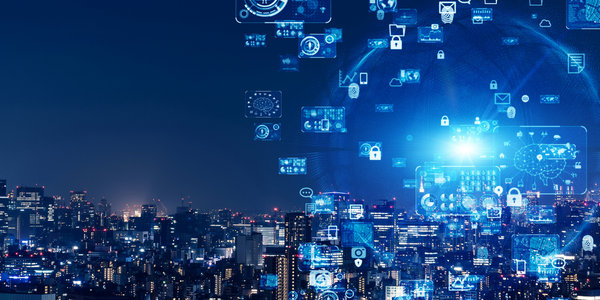
Case Study
Integration of PLC with IoT for Bosch Rexroth
The application arises from the need to monitor and anticipate the problems of one or more machines managed by a PLC. These problems, often resulting from the accumulation over time of small discrepancies, require, when they occur, ex post technical operations maintenance.
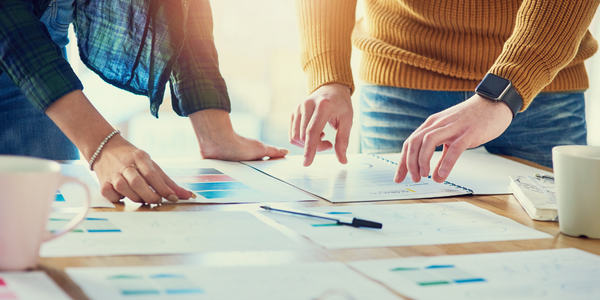
Case Study
Data Gathering Solution for Joy Global
Joy Global's existing business processes required customers to work through an unstable legacy system to collect mass volumes of data. With inadequate processes and tools, field level analytics were not sufficient to properly inform business decisions.