Customer Company Size
Large Corporate
Region
- Europe
Country
- Germany
Product
- DocuWare
- CONNECT to SAP DocuWare module
- SAP business system
- NetApp storage system
Tech Stack
- SAP
- DocuWare
- NetApp
Implementation Scale
- Enterprise-wide Deployment
Impact Metrics
- Productivity Improvements
- Cost Savings
Technology Category
- Platform as a Service (PaaS) - Data Management Platforms
- Application Infrastructure & Middleware - Data Exchange & Integration
Applicable Functions
- Business Operation
- Procurement
Use Cases
- Supply Chain Visibility
- Inventory Management
Services
- System Integration
- Data Science Services
About The Customer
ZF Friedrichshafen AG is a leading supplier of mechatronic solutions for the automobile industry and a developer of computer input devices. The company is based in Auerbach, Germany. In 2008, ZF Friedrichshafen AG acquired Cherry Corporation, and together they comprise the Electronic Systems business unit in ZF's Industrial Technology division. The management at Cherry Corporation recognized very early on that rapid access to digital information would markedly sharpen their competitiveness. They implemented their first document management system as far back as 1991, choosing Arcis, a package from Siemens Nixdorf. By the time their original DMS was discontinued in 2004, the company had well over a million corporate and technical documents in their electronic archives.
The Challenge
ZF Friedrichshafen AG, a leading supplier of mechatronic solutions for the automobile industry, had over a million corporate and technical documents in their electronic archives by 2004. The company needed a new system that could carry over the legacy documents at low cost, demonstrate a flexible and customizable software structure, and promise to be a safe long-term investment. The requirements for electronic document administration had drastically risen over the years. Features for process management and optimization, such as the ability to generate workflows, were nonnegotiable. They also were looking for a certified SAP interface. In the interests of preventing their applications from growing out of control, for years they have held to the strategy of consistently standardizing all their business processes to fit into their SAP environment.
The Solution
DocuWare satisfied the selection criteria and made a strong impression with its modular structure, not to mention the comparatively low cost to implement and operate it. Beyond those factors, the DocuWare partner demonstrated persuasive expertise and offered a coherent plan for migrating the legacy archive files. In only a few days, the DMS specialist was able to carry through the basic implementation including integration into the SAP system. The CONNECT to SAP DocuWare module augmented the existing SAP infrastructure with features for archiving documents and data via the SAP ArchiveLink interface. Incoming and outgoing documents, print lists, and SAP files could now be archived directly from the business solution. Associated Office documents such as Word and Excel files could also be directly attached to SAP documents and stored with them using the same module. The carryover of legacy documents from the Arcis archive was not a problem from a technical perspective but was outsourced to an external service provider due to the large volume of files.
Operational Impact
Quantitative Benefit
Case Study missing?
Start adding your own!
Register with your work email and create a new case study profile for your business.
Related Case Studies.
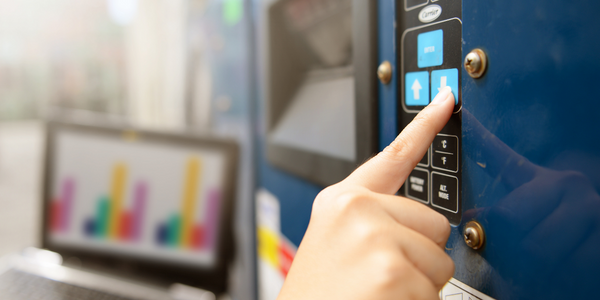
Case Study
Remote Temperature Monitoring of Perishable Goods Saves Money
RMONI was facing temperature monitoring challenges in a cold chain business. A cold chain must be established and maintained to ensure goods have been properly refrigerated during every step of the process, making temperature monitoring a critical business function. Manual registration practice can be very costly, labor intensive and prone to mistakes.
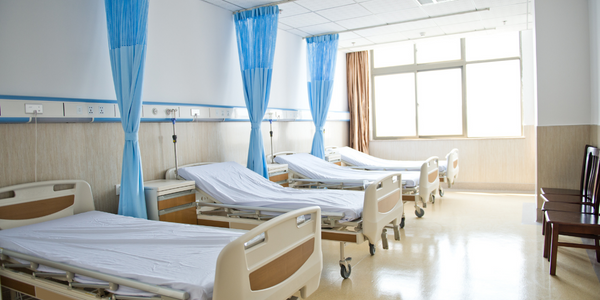
Case Study
Hospital Inventory Management
The hospital supply chain team is responsible for ensuring that the right medical supplies are readily available to clinicians when and where needed, and to do so in the most efficient manner possible. However, many of the systems and processes in use at the cancer center for supply chain management were not best suited to support these goals. Barcoding technology, a commonly used method for inventory management of medical supplies, is labor intensive, time consuming, does not provide real-time visibility into inventory levels and can be prone to error. Consequently, the lack of accurate and real-time visibility into inventory levels across multiple supply rooms in multiple hospital facilities creates additional inefficiency in the system causing over-ordering, hoarding, and wasted supplies. Other sources of waste and cost were also identified as candidates for improvement. Existing systems and processes did not provide adequate security for high-cost inventory within the hospital, which was another driver of cost. A lack of visibility into expiration dates for supplies resulted in supplies being wasted due to past expiry dates. Storage of supplies was also a key consideration given the location of the cancer center’s facilities in a dense urban setting, where space is always at a premium. In order to address the challenges outlined above, the hospital sought a solution that would provide real-time inventory information with high levels of accuracy, reduce the level of manual effort required and enable data driven decision making to ensure that the right supplies were readily available to clinicians in the right location at the right time.