- Functional Applications - Enterprise Resource Planning Systems (ERP)
- Functional Applications - Manufacturing Execution Systems (MES)
- Equipment & Machinery
- Maintenance
- Quality Assurance
- Additive Manufacturing
- Manufacturing Process Simulation
- System Integration
Oestergaard is a family-owned manufacturing company based in Nørre Aaby, Denmark. The company specializes in the design, manufacturing, installation, and servicing of processing equipment for the meat and fish by-products rendering industry. Founded in 2017 by Leif Oestergaard, a prominent figure in the global rendering industry, the company operates on modern, lean manufacturing principles. A significant portion of Oestergaard's production is exported outside of Denmark. The company targets customers seeking high-quality, reliable food-rendering equipment that adheres to stringent quality assurance and compliance standards.
Oestergaard, a Denmark-based manufacturing company specializing in processing equipment for the meat and fish by-products rendering industry, faced a significant challenge in improving the accuracy of its bills of materials (BoM). The company experienced a sharp increase in product demand and needed a solution to better communicate design changes from the engineering department to the factory floor. Manual transcriptions of CAD BoMs into the ERP system and inaccurate BoMs were costing the company thousands of dollars in lost productivity and incorrect part orders. Oestergaard used Autodesk Inventor for its CAD system and the Oracle NetSuite OneWorld ERP system, but lacked a seamless bridge between the two.
Oestergaard embarked on an enterprise-wide effort to streamline their business processes, particularly in terms of Items, Bills of Materials, and Routings management. The company aimed to establish a live, real-time, bidirectional link between the CAD and ERP systems to eliminate duplicate manual data entries. After considering various solutions, Oestergaard's Technical Manager, Jesper ANTONSEN, and his team decided to implement the Agni Link system developed by Elmo Solutions. This system allowed both CAD and ERP users to share product information in real-time. The project began in October 2017 and was fully rolled out by January 2018.
Case Study missing?
Start adding your own!
Register with your work email and create a new case study profile for your business.
Related Case Studies.
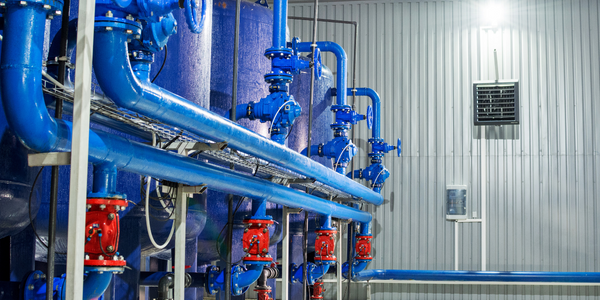
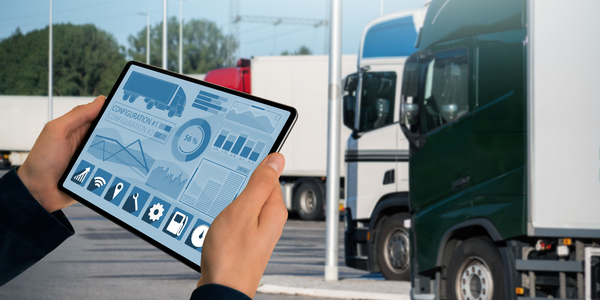
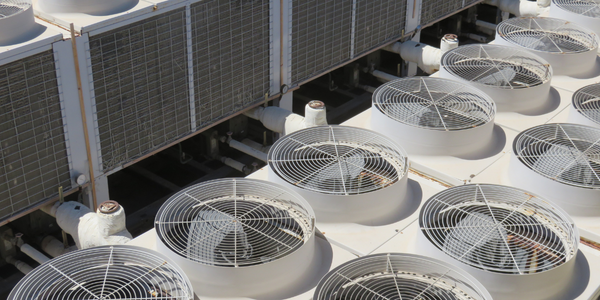
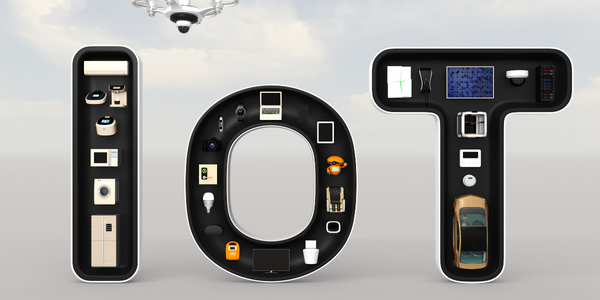
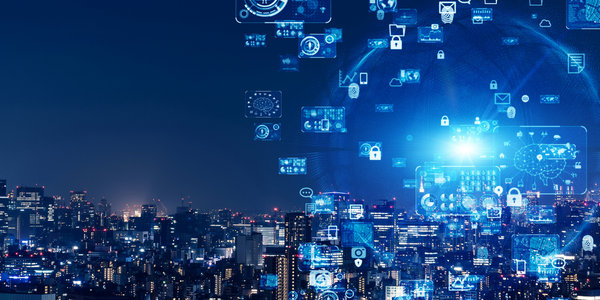
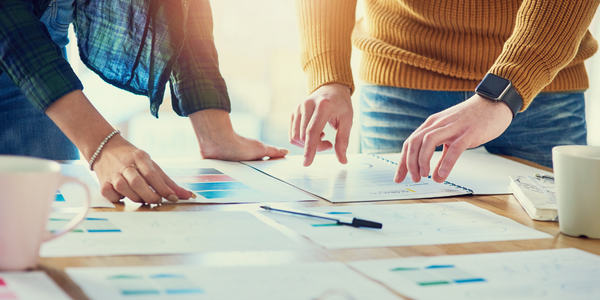