Technology Category
- Functional Applications - Fleet Management Systems (FMS)
- Robots - Autonomous Guided Vehicles (AGV)
Applicable Industries
- Automotive
Applicable Functions
- Maintenance
- Procurement
Use Cases
- Fleet Management
- Vehicle Performance Monitoring
About The Customer
The customer in this case study is a client of Element Fleet. They operate a fleet of vehicles and had planned to place factory vehicle orders for their fall order cycle. However, they faced a challenge when the OEM cut off ordering due to their vehicle needs exceeding the OEM allocation. They had an additional 50-unit order planned for 2022, which meant they were looking at a total of 100 units that needed replacement. They turned to Element Fleet to help them navigate this challenge and find a solution to their vehicle needs.
The Challenge
In 2021, an Element client, like many other fleets, planned to place factory vehicle orders for their fall order cycle. However, they soon discovered that the original equipment manufacturer (OEM) had cut off ordering due to the client's vehicle needs exceeding the OEM allocation. The fall order exceeded the allocation by 50 units. The client had an additional 50-unit order planned for 2022, which meant they needed to find a solution for the 100 units that needed replacement. The challenge was to navigate the OEM controlled ordering allocations and find a way to fulfill the client's vehicle needs.
The Solution
Element Fleet experts, through close collaboration with the client and the OEM, found a solution to the challenge. They learned of another client who had cancelled a 100-unit order and identified an opportunity to reallocate these vehicles to their client. The timing was critical to secure the units, and the client needed to advance the order of 50 units they had planned to place over the next 12 months to meet all their 100-unit replacement needs. This solution required strategic planning and swift action to secure the vehicles before they were taken by another client.
Operational Impact
Quantitative Benefit
Case Study missing?
Start adding your own!
Register with your work email and create a new case study profile for your business.
Related Case Studies.
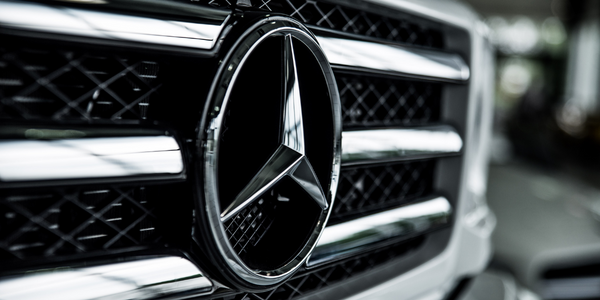
Case Study
Integral Plant Maintenance
Mercedes-Benz and his partner GAZ chose Siemens to be its maintenance partner at a new engine plant in Yaroslavl, Russia. The new plant offers a capacity to manufacture diesel engines for the Russian market, for locally produced Sprinter Classic. In addition to engines for the local market, the Yaroslavl plant will also produce spare parts. Mercedes-Benz Russia and his partner needed a service partner in order to ensure the operation of these lines in a maintenance partnership arrangement. The challenges included coordinating the entire maintenance management operation, in particular inspections, corrective and predictive maintenance activities, and the optimizing spare parts management. Siemens developed a customized maintenance solution that includes all electronic and mechanical maintenance activities (Integral Plant Maintenance).
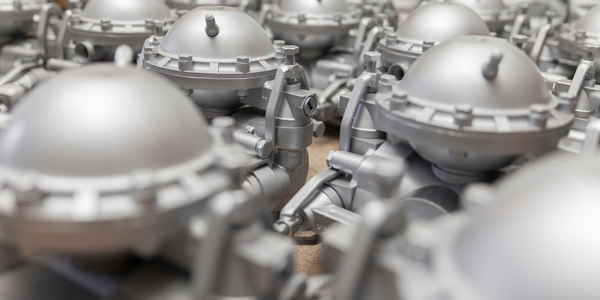
Case Study
Monitoring of Pressure Pumps in Automotive Industry
A large German/American producer of auto parts uses high-pressure pumps to deburr machined parts as a part of its production and quality check process. They decided to monitor these pumps to make sure they work properly and that they can see any indications leading to a potential failure before it affects their process.