Technology Category
- Networks & Connectivity - RF Transceivers
- Sensors - RF Meters
Applicable Industries
- Aerospace
- Equipment & Machinery
Applicable Functions
- Product Research & Development
Use Cases
- Mass Customization
- Time Sensitive Networking
Services
- Hardware Design & Engineering Services
- Training
About The Customer
Spectrum Integrity is a full-service engineering design service firm and solution provider for companies requiring outstanding hardware designs for advanced RF, high-speed, and semiconductor test applications. The company designs ultra-high-speed digital, RF, and microwave PCBs that process signals at frequencies from 20 to 110 GHz and above. The CAD screenshots show 12- and 14-layer ultra-high-speed digital applications successfully designed in Altium Designer. These examples have outer layer traces designed to support 50GHz signals and multiple inner layer traces designed to support 28GHz. These designs utilized complex geometries, split power planes, transmission lines, and coplanar vias successfully designed using a combination of Altium Designer and proprietary design techniques.
The Challenge
Spectrum Integrity, a company that designs ultra-high-speed digital, RF, and microwave PCBs, faced significant challenges in its design process. The company's unique design requirements necessitated a proprietary process, but it also had to interface with industry-standard component libraries and the design review processes of its clients. The company relied on a collection of specialized tools, but the native schematic capabilities in these tools were unusable. Instead, Spectrum Integrity had to use a third-party schematic tool that prevented synchronization of layout and schematic and lacked cross-probing capability. This made the process disjointed. Additionally, there was no free external viewer feature for the board designs, and no simple way to export design files. The frequent client reviews were a tedious and long process. The company had tried to streamline the process using PADS, but its schematic capture tool was similarly inadequate, and its version control was missing critical built-in functionality.
The Solution
Spectrum Integrity adopted Altium Designer to address its design challenges. The advanced features and integration across the design process offered by Altium Designer provided immediate improvements. The company found it easy to customize the Altium Designer environment for the intricacies of RF design. Strategic, proprietary improvements were added to the tool suite to make them very powerful and efficient for RF and ultra-high-speed digital design. To streamline interaction with RF analysis, board designs were exported in Gerber data into a 3D field solver. After completing analysis, Altium Designer read the files back in AutoCAD or DXF format, a process that retained net intelligence within the integrated tool suite. Automation within Altium Designer PCB layout helped streamline steps within the design process. The version control features were very important to Spectrum Integrity, because RF designs often require multiple versions stretched across a very extensive review process. Altium Designer also includes a free design viewer and can import and export across many popular formats.
Operational Impact
Quantitative Benefit
Case Study missing?
Start adding your own!
Register with your work email and create a new case study profile for your business.
Related Case Studies.
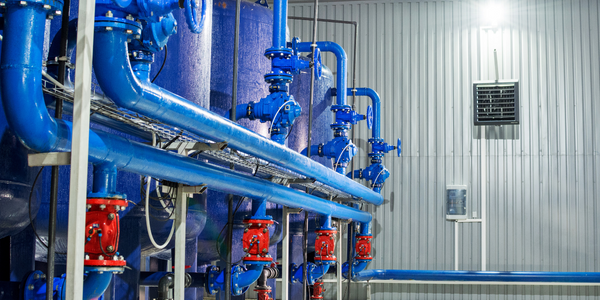
Case Study
Smart Water Filtration Systems
Before working with Ayla Networks, Ozner was already using cloud connectivity to identify and solve water-filtration system malfunctions as well as to monitor filter cartridges for replacements.But, in June 2015, Ozner executives talked with Ayla about how the company might further improve its water systems with IoT technology. They liked what they heard from Ayla, but the executives needed to be sure that Ayla’s Agile IoT Platform provided the security and reliability Ozner required.
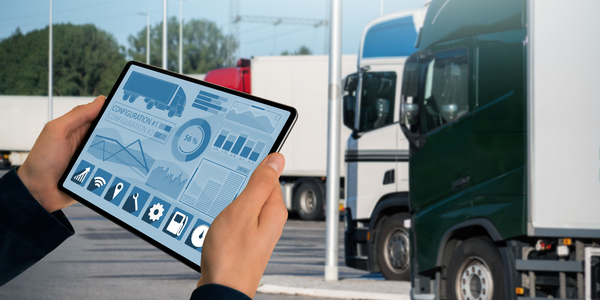
Case Study
IoT enabled Fleet Management with MindSphere
In view of growing competition, Gämmerler had a strong need to remain competitive via process optimization, reliability and gentle handling of printed products, even at highest press speeds. In addition, a digitalization initiative also included developing a key differentiation via data-driven services offers.
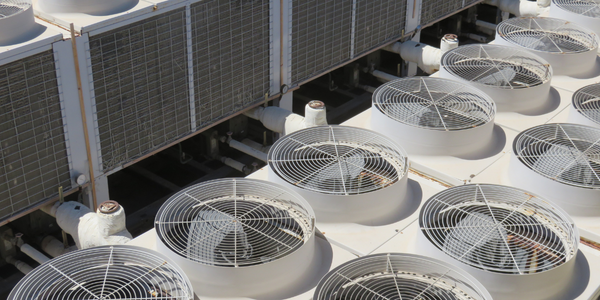
Case Study
Predictive Maintenance for Industrial Chillers
For global leaders in the industrial chiller manufacturing, reliability of the entire production process is of the utmost importance. Chillers are refrigeration systems that produce ice water to provide cooling for a process or industrial application. One of those leaders sought a way to respond to asset performance issues, even before they occur. The intelligence to guarantee maximum reliability of cooling devices is embedded (pre-alarming). A pre-alarming phase means that the cooling device still works, but symptoms may appear, telling manufacturers that a failure is likely to occur in the near future. Chillers who are not internet connected at that moment, provide little insight in this pre-alarming phase.
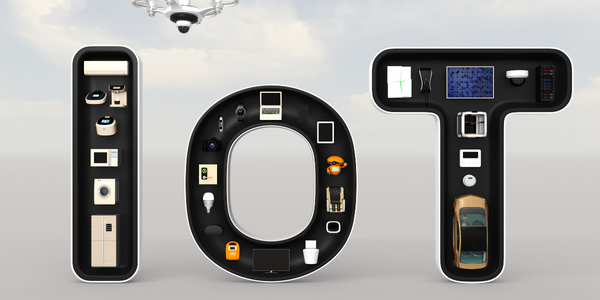
Case Study
Premium Appliance Producer Innovates with Internet of Everything
Sub-Zero faced the largest product launch in the company’s history:It wanted to launch 60 new products as scheduled while simultaneously opening a new “greenfield” production facility, yet still adhering to stringent quality requirements and manage issues from new supply-chain partners. A the same time, it wanted to increase staff productivity time and collaboration while reducing travel and costs.
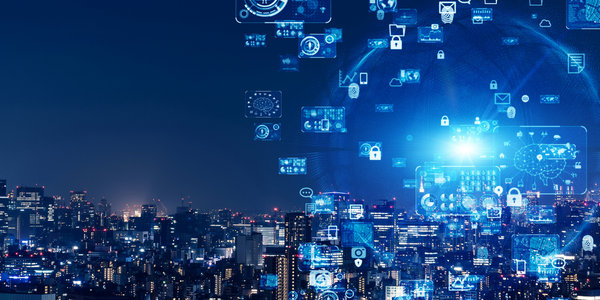
Case Study
Integration of PLC with IoT for Bosch Rexroth
The application arises from the need to monitor and anticipate the problems of one or more machines managed by a PLC. These problems, often resulting from the accumulation over time of small discrepancies, require, when they occur, ex post technical operations maintenance.
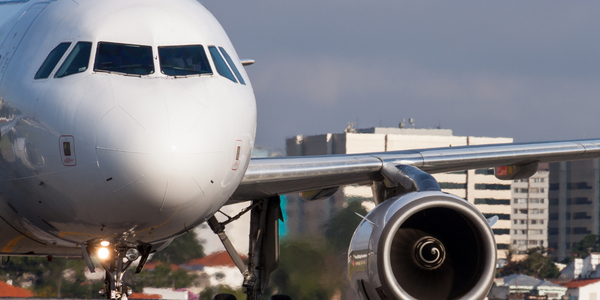
Case Study
Airbus Soars with Wearable Technology
Building an Airbus aircraft involves complex manufacturing processes consisting of thousands of moving parts. Speed and accuracy are critical to business and competitive advantage. Improvements in both would have high impact on Airbus’ bottom line. Airbus wanted to help operators reduce the complexity of assembling cabin seats and decrease the time required to complete this task.