Customer Company Size
Large Corporate
Region
- America
- Asia
- Europe
Country
- United States
Product
- TabWare EAM
Tech Stack
- Cloud Computing
Implementation Scale
- Enterprise-wide Deployment
Impact Metrics
- Productivity Improvements
- Cost Savings
Technology Category
- Functional Applications - Enterprise Asset Management Systems (EAM)
- Infrastructure as a Service (IaaS) - Cloud Computing
Applicable Functions
- Maintenance
Use Cases
- Asset Health Management (AHM)
- Predictive Maintenance
Services
- System Integration
- Training
About The Customer
Universal Forest Products, Inc. is a leading manufacturer and distributor of engineered wood and construction materials in the retail, industrial, and construction markets. Its product offerings include natural wood, composite wood and plastic products for home beautification, pallets and containers for industry and agriculture, specialty concrete forming products, fabricated roof and floor trusses and wall panels for the site-built and mobile home industries. Founded in 1955, UFPI is headquartered in Grand Rapids, Mich., with affiliates throughout North America, Europe, Asia and Australia. The publicly traded company generates over $3 billion in revenue and has approximately 10,000 employees.
The Challenge
Universal Forest Products operates 130 facilities worldwide, with each location acting as an independent operation. Initially only one plant had a CMMS/EAM system, a few locations had paper work order systems, but most had no system in place at all. Maintenance staff at the sites varied as well, ranging from one or two individuals to a team of 15 to 20. The lack of a formalized preventive maintenance system was having an impact on productivity in the plants. Unexpected breakdowns were causing costly repairs and overtime expenses. There was no precise method available to management to identify maintenance expenditures. With more sophisticated equipment being introduced in the plants, it became vital that the equipment be maintained to the manufacturers’ recommendations in order to preserve warranties and realize the expected increases in productivity.
The Solution
A single CMMS/EAM solution throughout the company was a priority. In 2012, the Executive Vice President and Vice President of the Manufacturing division began the search for a system that would fit the needs of UFPI. Aptean TabWare EAM was chosen due to its full features with standard processes and workflows, ease of use and total cost of ownership. A dedicated maintenance system lead was established as a single point of contact to streamline implementation of TabWare and user training on the system. Having one individual with the right skillset has made the implementations easier to plan, schedule and support. The company believes that the best way for employees to embrace the system as their own is to have as much “skin in the game” as early as possible. To that end, the EAM system lead examined what each user persona would be doing within the system in order to focus training on their specific responsibilities. Scenarios are presented in the training environment that mimic each user role. New users then begin working with TabWare by entering actual work orders into the live system to reinforce learning.
Operational Impact
Quantitative Benefit
Case Study missing?
Start adding your own!
Register with your work email and create a new case study profile for your business.
Related Case Studies.

Case Study
Remote Monitoring & Predictive Maintenance App for a Solar Energy System
The maintenance & tracking of various modules was an overhead for the customer due to the huge labor costs involved. Being an advanced solar solutions provider, they wanted to ensure early detection of issues and provide the best-in-class customer experience. Hence they wanted to automate the whole process.
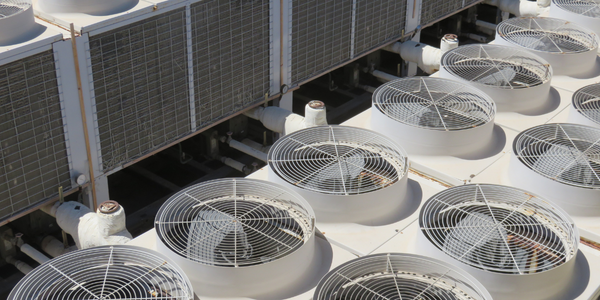
Case Study
Predictive Maintenance for Industrial Chillers
For global leaders in the industrial chiller manufacturing, reliability of the entire production process is of the utmost importance. Chillers are refrigeration systems that produce ice water to provide cooling for a process or industrial application. One of those leaders sought a way to respond to asset performance issues, even before they occur. The intelligence to guarantee maximum reliability of cooling devices is embedded (pre-alarming). A pre-alarming phase means that the cooling device still works, but symptoms may appear, telling manufacturers that a failure is likely to occur in the near future. Chillers who are not internet connected at that moment, provide little insight in this pre-alarming phase.
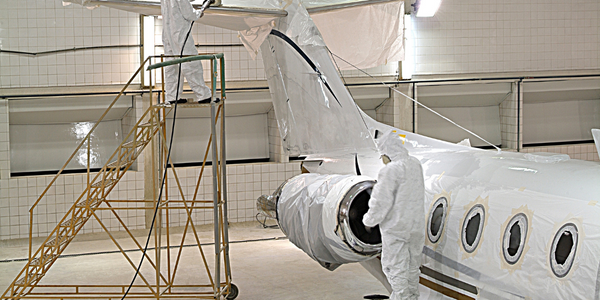
Case Study
Aircraft Predictive Maintenance and Workflow Optimization
First, aircraft manufacturer have trouble monitoring the health of aircraft systems with health prognostics and deliver predictive maintenance insights. Second, aircraft manufacturer wants a solution that can provide an in-context advisory and align job assignments to match technician experience and expertise.
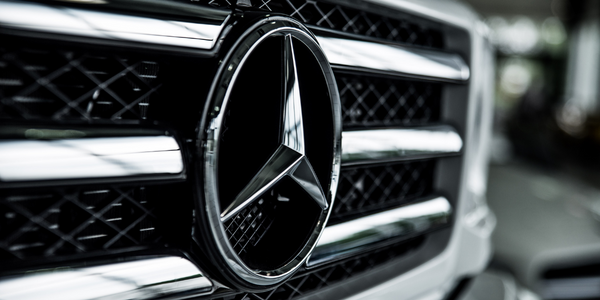
Case Study
Integral Plant Maintenance
Mercedes-Benz and his partner GAZ chose Siemens to be its maintenance partner at a new engine plant in Yaroslavl, Russia. The new plant offers a capacity to manufacture diesel engines for the Russian market, for locally produced Sprinter Classic. In addition to engines for the local market, the Yaroslavl plant will also produce spare parts. Mercedes-Benz Russia and his partner needed a service partner in order to ensure the operation of these lines in a maintenance partnership arrangement. The challenges included coordinating the entire maintenance management operation, in particular inspections, corrective and predictive maintenance activities, and the optimizing spare parts management. Siemens developed a customized maintenance solution that includes all electronic and mechanical maintenance activities (Integral Plant Maintenance).