Technology Category
- Application Infrastructure & Middleware - Data Exchange & Integration
- Platform as a Service (PaaS) - Application Development Platforms
Applicable Industries
- Equipment & Machinery
- Oil & Gas
Applicable Functions
- Sales & Marketing
Use Cases
- Time Sensitive Networking
Services
- System Integration
About The Customer
UJET is a world-leading contact center platform that bridges the technology gap between outdated customer service platforms and modern consumers and brands. Their intuitively designed voice and digital engagement suite, coupled with powerful AI and advanced analytics capabilities, makes providing excellent customer experiences seamless for every business. UJET has been ranked #1 in Contact Center Operations by G2 users for 11 quarters in a row and won the 2022 Best of Enterprise Connect Overall. UJET is also partnered with Google on its Contact Center AI Platform.
The Challenge
UJET, a leading contact center platform, was facing challenges in prioritizing their vast array of accounts due to their status as a rapidly growing startup with multiple ideal customer profiles. The company's sales development representatives (SDRs) were struggling with inconsistent open rates, reply rates, and outbound pipeline due to a lack of account-level insights on the buyers’ journey. The timing of their outreach was often off, and they lacked the necessary tools to track intent, drive awareness, and deliver messages to the right audience at the right time. As Bob Wassell, SDR Director at UJET, put it, they were trying to 'find treasure without a map.'
The Solution
UJET turned to 6sense for a solution to their challenges. 6sense's intent data provided UJET's SDRs with direction and focus, allowing them to prioritize their efforts on the right accounts showing interest in solutions like theirs. The SDRs were able to uncover which accounts were visiting their website and where they were located, understand the keywords these accounts were searching for, set up daily alerts for accounts that reached 6QA (6sense qualified accounts) status, and build dashboards to view accounts in every stage. They incorporated these searched-for keywords directly into their messaging and optimized their outreach response. 6sense quickly became an essential coaching and messaging tool for inbound and outbound motions, and also helped to strengthen marketing and sales alignment by bringing data to subjective conversations.
Operational Impact
Quantitative Benefit
Case Study missing?
Start adding your own!
Register with your work email and create a new case study profile for your business.
Related Case Studies.
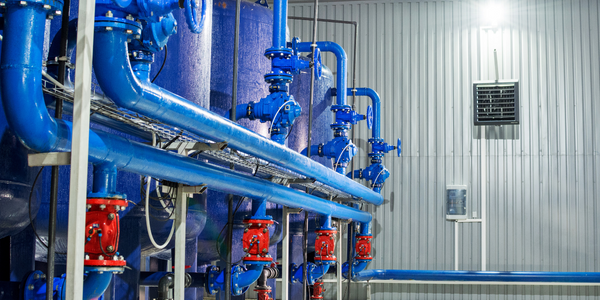
Case Study
Smart Water Filtration Systems
Before working with Ayla Networks, Ozner was already using cloud connectivity to identify and solve water-filtration system malfunctions as well as to monitor filter cartridges for replacements.But, in June 2015, Ozner executives talked with Ayla about how the company might further improve its water systems with IoT technology. They liked what they heard from Ayla, but the executives needed to be sure that Ayla’s Agile IoT Platform provided the security and reliability Ozner required.
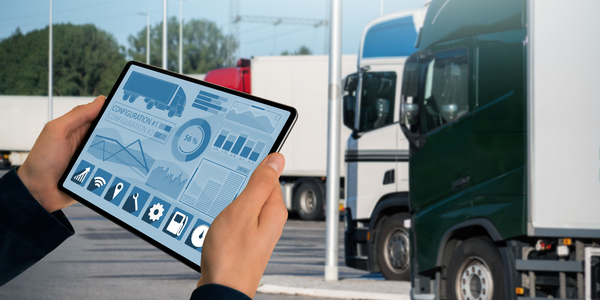
Case Study
IoT enabled Fleet Management with MindSphere
In view of growing competition, Gämmerler had a strong need to remain competitive via process optimization, reliability and gentle handling of printed products, even at highest press speeds. In addition, a digitalization initiative also included developing a key differentiation via data-driven services offers.
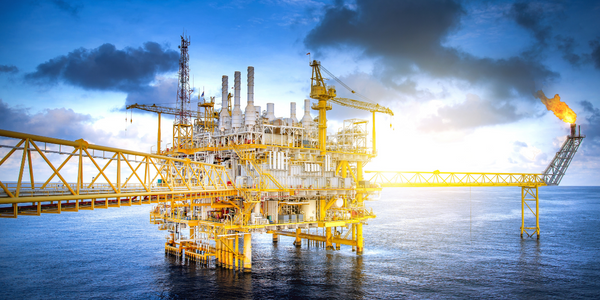
Case Study
Taking Oil and Gas Exploration to the Next Level
DownUnder GeoSolutions (DUG) wanted to increase computing performance by 5 to 10 times to improve seismic processing. The solution must build on current architecture software investments without sacrificing existing software and scale computing without scaling IT infrastructure costs.
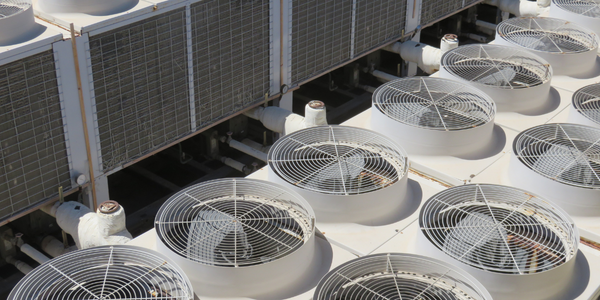
Case Study
Predictive Maintenance for Industrial Chillers
For global leaders in the industrial chiller manufacturing, reliability of the entire production process is of the utmost importance. Chillers are refrigeration systems that produce ice water to provide cooling for a process or industrial application. One of those leaders sought a way to respond to asset performance issues, even before they occur. The intelligence to guarantee maximum reliability of cooling devices is embedded (pre-alarming). A pre-alarming phase means that the cooling device still works, but symptoms may appear, telling manufacturers that a failure is likely to occur in the near future. Chillers who are not internet connected at that moment, provide little insight in this pre-alarming phase.
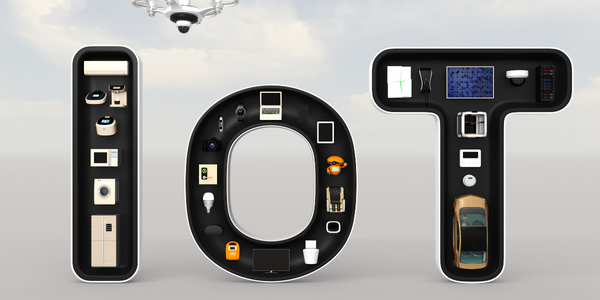
Case Study
Premium Appliance Producer Innovates with Internet of Everything
Sub-Zero faced the largest product launch in the company’s history:It wanted to launch 60 new products as scheduled while simultaneously opening a new “greenfield” production facility, yet still adhering to stringent quality requirements and manage issues from new supply-chain partners. A the same time, it wanted to increase staff productivity time and collaboration while reducing travel and costs.