MPDV
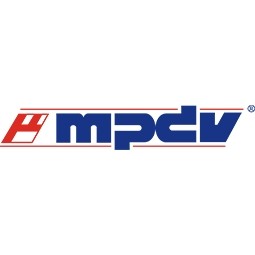
Overview
HQ Location
Germany
|
Year Founded
1977
|
Company Type
Private
|
Revenue
< $10m
|
Employees
201 - 1,000
|
Website
|
Company Description
MPDV is one of the leading suppliers of Manufacturing Execution Systems (MES). They offer solutions for competitive businesses with innovative and sophisticated MES systems of high quality and a broad range of services.
Year founded: 1977
Year founded: 1977
IoT Solutions
The proposed MES architecture is based on the Internet of Things (IoT), completely linking all resources and the manufacturing companies' security needs. Consequently, shop floor and IT clouds should be separated. In order for the machine level to reap benefits from cloud technologies, a specific modification known as the edge cloud or fog, was employed. The central instance, the Edge Gateway, connects the edge cloud with the IT cloud. Therefore, shop floor components can communicate with each other in real time and the IT cloud can retrieve and manage the data.
IT support in production plays a key role for Integrated Industry (Industry 4.0). In order to cover future production processes new standards and functions are required, which will especially affect MES applications. MPDV introduces a concept for the Manufacturing Execution System (MES) of the future MES 4.0.
IT support in production plays a key role for Integrated Industry (Industry 4.0). In order to cover future production processes new standards and functions are required, which will especially affect MES applications. MPDV introduces a concept for the Manufacturing Execution System (MES) of the future MES 4.0.
Key Customers
Adidas, Alstom, Johnson Controls
IoT Snapshot
MPDV is a provider of Industrial IoT testing and certification, and training services, and also active in the electronics, life sciences, and metals industries.
Technology Stack
MPDV’s Technology Stack maps MPDV’s participation in the IoT Technology stack.
-
Devices Layer
-
Edge Layer
-
Cloud Layer
-
Application Layer
-
Supporting Technologies
Technological Capability:
None
Minor
Moderate
Strong
Supplier missing?
Start adding your own!
Register with your work email and create a new supplier profile for your business.
Case Studies.
Case Study
Melitta Europa GmbH & Co. KG Implements HYDRA MES for Enhanced Production Efficiency
Melitta Europa GmbH & Co. KG faced the challenge of maintaining high-quality production standards while ensuring competitiveness, environmental friendliness, and innovation in their manufacturing processes. The production of filter bags required a focus on these aspects to meet market demands and regulatory standards. Additionally, the company needed to streamline its production processes to improve efficiency and reduce costs. The existing systems were not sufficient to provide real-time data and insights necessary for optimizing production and maintenance schedules. This lack of real-time visibility into production operations and machine conditions posed a significant challenge in maintaining optimal production flow and minimizing downtime.
Case Study
pelzGROUP Implements HYDRA MES for Enhanced Manufacturing and Operational Efficiency
In 2014, pelzGROUP sought to automate data collection on the shop floor to replace paper-based systems and improve data reliability and speed. They needed a scalable Manufacturing Execution System (MES) that could integrate with their existing processes and provide real-time data access. The challenge was to find a system that could handle the complexity of their operations, including processing multiple orders per day and managing a high volume of packaging units. Additionally, they required a solution that could integrate with their in-house developed ERP system and provide reliable key performance indicators like Overall Equipment Effectiveness (OEE).
Case Study
Schmidt + Clemens Implements HYDRA MES for Enhanced Production Control and Integration with SAP
In the summer of 2007, Schmidt + Clemens faced the challenge of replacing their outdated systems for time and attendance and access control. They required a new system that could integrate seamlessly with SAP for various functions such as maintenance, shop floor scheduling, production control, DNC operation, and machine data collection. The company sought a modular and powerful MES solution from a reputable supplier with extensive SAP expertise and a certified SAP interface. The goal was to enhance their operational efficiency and ensure smooth data flow between different systems.
Case Study
DIEHL Metall Implements HYDRA for Enhanced Time & Attendance and Shop Floor Data Management
DIEHL Metall faced the challenge of replacing an outdated Time & Attendance system with a new, flexible, and fail-proof system that could integrate with SAP in the future. The new system needed to comply with company agreements on flexible working hours and provide a certified interface to SAP. Additionally, the Shop Floor Data module required online information for the entire production level, simplifying work procedures, supporting paperless production, and facilitating machine data collection.
Case Study
ARGO-HYTOS Enhances Production Efficiency with HYDRA Manufacturing Execution System
ARGO-HYTOS faced challenges in increasing transparency and efficiency at their production site in Kraichtal-Menzingen. The company needed a solution to collect and analyze data on machine standstills to gain insights into machine efficiencies. The existing systems were not providing the level of detail and integration required to optimize machine assignments and improve overall production efficiency. Additionally, there was a need to consolidate the IT landscape and replace the existing Time & Attendance system to streamline operations and reduce manual data recording.
Case Study
GEDIA Automotive Group Enhances Production with MES HYDRA Integration Across Multiple Locations
GEDIA Automotive Group required a modular application package to connect ERP, HR, and production systems to increase machine and personnel capacities, obtain real-time data evaluations, and optimize planning. The challenge was to use as many standard functions as possible to ensure seamless integration and efficiency. The company needed a solution that could handle detailed planning on shift levels, specify order processing, and provide real-time progress tracking. Additionally, the solution had to support data collection from numerous machines and terminals, and facilitate the calculation of incentive wages while ensuring access control for authorized personnel.
Case Study
PHOENIX CONTACT Enhances Manufacturing Efficiency with HYDRA MES and SAP Integration
PHOENIX CONTACT faced the challenge of managing and efficiently controlling a vast array of data derived from complex multi-staged manufacturing processes. The company needed a solution that could provide higher transparency in production, improve productivity, and enhance the quality of data supplied by their ERP system, SAP. Additionally, they required a system that could detect machine standstills and provide statistics to optimize machine and tooling availability. The challenge was further compounded by the need to ensure the availability of all required resources for machines at the start of production, necessitating timely information and efficient data transmission to injection molding machines.
Case Study
WIKA Implements HYDRA MES to Enhance Production Control and Standardize Reporting
WIKA faced the challenge of maintaining efficiency and productivity amidst increasing product variety in their pre-fabrication processes. The company needed a solution to optimize production control and standardize controlling and reporting. The introduction of a Manufacturing Execution System (MES) was advised by a lean consultant to address these challenges. The main reason for selecting the MES solution HYDRA by MPDV was its broad range of standardized modules that could handle various tasks. Additionally, the mindset of the MES experts from MPDV and their international experience were appreciated by WIKA. The company expected the MES system to provide reliable order and machine data, which would benefit production control and improve planning, thus compensating for any delays in production.
Case Study
Ruch Novaplast GmbH + Co. KG Implements MES HYDRA for Enhanced Manufacturing Efficiency
In 2009, RUCH NOVAPLAST GmbH + Co. KG sought an integrated Manufacturing Execution System (MES) to address multiple operational needs. The company required a system capable of shop floor and machine data collection, batch tracing, quality data collection, and recording of working hours and access control. Additionally, the system needed to integrate seamlessly with their existing ERP system, Microsoft Dynamics AX, and ensure investment reliability. The challenge was to find a solution that could meet these diverse requirements while also being accepted by all departments involved.
Case Study
Krone Implements HYDRA MES System to Optimize Manufacturing Processes and Employee Management
In 2006, Krone faced the challenge of replacing outdated isolated solutions with an integrated MES system. Despite existing software tools, many manufacturing processes required optimization. Shop floor scheduling and production controlling were managed via Excel lists, making capacity planning based on actual values impossible. Quantities and interruptions were recorded per shift, with interruptions entered as overhead, preventing standardized and sustainable controlling.
Case Study
GROHE AG Enhances Manufacturing Efficiency with HYDRA MES System
Producing fittings and fixtures involves several steps such as casting, machining, surface finishing, and final assembly. The challenge was to collect data across the entire processing chain and efficiently plan and control the procedures. The focus was on perfect utilization of tools and machines to avoid unnecessary stockpiling and ensure smooth operations. The need for real-time data collection and evaluation was critical to address malfunctions and bottlenecks promptly.
Similar Suppliers.
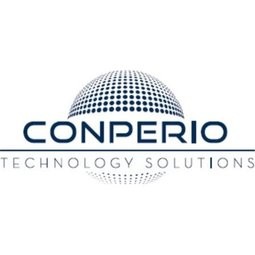
Supplier
Conperio Technology Solutions
Conperio Technology Solutions has served as a premiere provider of custom technology solutions for 25 years. Their commitment is to customers and to facilitate long-term alliances and use a tried and true process while providing cost effective solutions that enhances the customers’ value and return on capital investment.
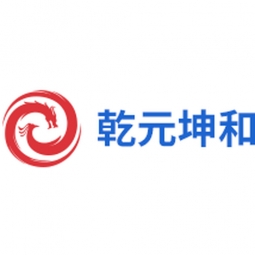
Supplier
Qianyuankunhe
Founded in July 2009, Qianyuankunhe is a professional software development company mainly providing intelligent industrial management systems consulting and software development and R&D services. With the continuous development of industrial strategy, and "Internet +" in China, Qianyuankunhe promotes the new concept of enterprise management and creates a unique intelligent manufacturing plant execution management platform to achieve rapid transformation and upgrading, allowing customers to improve operational efficiency, reduce costs and enhance core competitiveness.