Parsable
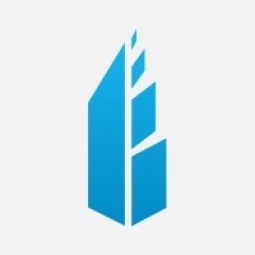
Overview
HQ Location
United States
|
Year Founded
2013
|
Company Type
Private
|
Revenue
$10-100m
|
Employees
51 - 200
|
Website
|
Twitter Handle
|
Company Description
Parsable empowers industrial workers with modern digital tools to improve productivity, quality, safety and sustainability. Parsable's Connected Worker® transforms static, paper-based procedures into mobile and interactive work instructions, enabling workers to leverage multimedia formats and collaborate in real time.
Supplier missing?
Start adding your own!
Register with your work email and create a new supplier profile for your business.
Case Studies.
Case Study
Digital Transformation in Coca-Cola European Partners Germany with Parsable
Coca-Cola European Partners Germany (CCEP DE) operates in a complex beverage market, catering to approximately 325,000 retail and foodservice customers and bottling and selling 3.5 billion liters of mineral water and soft drinks annually. The complexity of the supply chain and the increasing demands on the workforce in production and logistics posed significant challenges for the company's approximately 7,000 employees. As part of its 'Fit for Future' strategy, CCEP DE was seeking digital solutions to alleviate the burden on employees and enhance the company's competitiveness. The company aimed to introduce digital assistants to the store floor, similar to the networking of employees with mobile devices in the sales organization. The goal was to provide employees with electronic instructions and interactive checklists to help them comply with all specifications and standards and prevent errors.
Case Study
GRUPO BIMBO: Achieving Thousands in Cost-Savings Through the Digitization of Safety Programs
Grupo Bimbo, a global Mexico-based CPG company and the largest bakery in the world, was facing costly inaccuracies within their delivery operations. After introducing third-party delivery platforms, they were spending thousands on remedying customer complaints. The company needed to identify the source of the complaints and gain a full picture of where they were losing revenue. However, their paper-based systems could not provide the critical and actionable insights needed, such as visibility into the journey between production, handoff, and delivery, sources of errors such as mismatched orders or damaged products, and identification of costly inefficiencies, such as production errors and waste.
Case Study
Silgan PFC Enhances Quality and Efficiency with Parsable
Silgan Plastic Food Containers (PFC), a global leader in high-barrier plastic packaging, faced several operational challenges. Despite being an industry leader, the company struggled with issues related to transparency and management of tasks. The documentation process was entirely paper-based, leading to a lack of clarity about who was responsible for what tasks and when they were completed. This lack of transparency affected operational results. Handing over responsibilities was also a challenge, especially when team members were absent. Missed tasks were difficult to address due to these issues. Additionally, Silgan was required to conduct one major audit and several smaller ones each year. However, the paper-based filing system made locating necessary documentation a time-consuming and difficult process.
Case Study
GRUPO BIMBO: Elevating Safety Standards and Well-Being Through Digitization and Connectivity
Grupo Bimbo, a global Mexico-based CPG company and the largest bakery in the world, was facing challenges in implementing higher safety standards across its 20 plants in 10 countries. The company's existing systems were unable to provide access and control over key insights such as safety incidents and investigations, progress of best practice SOP implementation, and real-time visibility and data into safety performance. This lack of visibility and control was hindering the company's ability to make proactive decisions to prevent workplace incidents and implement organization-wide changes.
Case Study
Bimbo QSR | Achieving Next Level Occupational Safety Performance
Grupo Bimbo S.A.B. de C.V., the world's largest bakery, faced a lack of standardization across critical components of its safety program. This included safety incident investigations, safety observations, and good safety processes. The team identified an opportunity to improve safety performance by generating more insight into the safety program through standardizing operational procedures. They were already using Parsable Connected Worker® in the manufacturing side of the business and wanted to leverage this technology for safety. The challenge was to implement standardized safety program components in a multilingual environment across 20 plants in 10 countries.
Case Study
Driving Digital Innovation at Holcim through IoT
Holcim, a global leader in innovative and sustainable building solutions, was facing challenges in optimizing field inspections and routine inspections in its Cement, Aggregate, Asphalt and Ready-Mix locations. Despite the availability of modern technology, heavy industries like Holcim still relied on tribal knowledge, outdated paper-based procedures, and lacked accurate, real-time data. This traditional way of working led to numerous questions such as how to perform inspections, the right sequence, the required equipment, and the last time it was done. Both new hires and senior workers faced these challenges as safety and sustainability measures were constantly evolving. Manual paperwork was not only cumbersome and slow but also prone to errors such as missing or lost records, or worse, work that wasn’t being done at all.
Case Study
Global Brewery eliminates raw materials receipt errors and boosts accountability
The global brewery was facing issues with the receipt of brewing ingredients and materials. They were visually spot checking trucks that delivered these materials and often found mismatches between Bills of Lading, Ship Tickets, and even delivery locations. There were instances where they received the wrong materials or someone else’s materials which then hindered production and showed a lack of accountability. The company needed to accurately capture data and digitize processes in order to optimize operations. They wanted to collect and analyze quality data faster, and allow inspectors to report inconsistencies right away. They also wanted to provide quality managers and their teams with greater visibility and control over real-time data captured.
Case Study
Global Brewery increases OEE by 5% with actionable insights from Parsable
The global brewery was focused on product development, which resulted in the adoption of digital transformation processes taking a back seat. One of the major challenges was enabling operators on the floor to complete autonomous maintenance tasks, like clean/inspect/lubricate (CIL). The brewery had industry-standard CIL steps documented on laminated sheets of paper. However, these were rarely used and contained outdated images and information. There was no way to track if operators were completing the process or not – the data on CIL completion rates across teams and machines was inadequate. This resulted in a lack of confidence that the machines were being maintained at an optimal level and the inability to accurately track the completion of this critical procedure.
Case Study
Customer Success Story: Scientific Drilling
Scientific Drilling, a leading provider of directional drilling equipment and services, aimed to become the 'ultimate partner in wellbore placement'. To achieve this, they focused on tool performance, strategic cost reduction, and process optimization. Rob McKee, SVP of Manufacturing and Product Support, was tasked with driving the reliability component of these performance improvements. The team recognized the need to integrate in-depth data analysis into their repair processes at Scientific Drilling’s motor shops. They aimed for digital workflows for standard assembly, disassembly, and repair procedures, actionable insights and quick visibility into quality workflows, near real-time data collection during repair operations, 100% conformance to process standards, and measurable improvements in cost and reliability.
Case Study
Global Dairy Manufacturer improves Quality and Safety with insights from Parsable
The company, one of the largest dairy manufacturers in the world, was facing hurdles in scaling its operations to meet growing demand. Outdated procedures and processes led to inconsistent data capture, impacting operational productivity, quality, and employee safety. The company's largest site produces different types of drinkable yogurts. For every batch of finished product, samples are sent to the quality lab for microbiology and physico-chemical testing. All lab results were recorded on paper and created large binders of data, which were then manually entered into SAP every 24 hours, leaving room for human error. The data reporting process took anywhere from seven to 30 days to uncover trends or identify if the production line was complying with quality standards. Additionally, a single safety inspector would walk around a production facility to conduct safety rounds and create Safety Behavior Observations (SBOs). These reports were filled out inconsistently and would sometimes get lost, resulting in considerable safety insurance premium costs.