技术
- 网络安全和隐私 - 身份认证管理
- 网络安全和隐私 - 入侵检测
适用行业
- 服装
- 消费品
适用功能
- 采购
- 销售与市场营销
用例
- 行为与情绪追踪
- 牲畜监测
服务
- 测试与认证
关于客户
6thStreet.com 是 The Apparel Group 的电子商务部门,The Apparel Group 是世界上最大的零售商之一,总部位于迪拜。该公司在 2018 年黑色星期五期间的销售额大幅增长,表明消费者行为正在转向全渠道体验。 6thStreet 的首席执行官 Dharmin Ved 制定了推动 10 倍增长的雄心勃勃的目标,这需要重点关注客户关系管理 (CRM)。该公司使用不同的工具来发送短信、电子邮件、移动推送通知和应用内消息,这些工具各自为政,因此很难提供有意义的全渠道体验。
挑战
The Apparel Group 的电子商务部门 6thStreet.com 的销售额正在显着增长,这表明消费者行为正在向全渠道体验转变。首席执行官设定了推动 10 倍增长的雄心勃勃的目标,这需要重点关注客户关系管理 (CRM)。然而,由于使用不同的工具发送短信、电子邮件、移动推送通知和应用内消息,该团队在了解消费者行为、旅程、喜好、偏好和购买模式方面面临挑战。这些工具各自为政,难以全面了解消费者的旅程、绘制跨渠道的消费者行为并提供有意义的全渠道体验。很明显,他们需要对其技术堆栈进行现代化改造。
解决方案
6thStreet 在 2019 年初选择了 MoEngage 来实现其技术堆栈的现代化。 MoEngage 已展现出处理规模的能力,并在海湾合作委员会地区拥有多个大客户,使其成为首选合作伙伴。 CRM 团队采用了清晰的 12 个月路线图来推动快速增长。他们利用 MoEngage 通过捕获其网站、移动应用程序和电子邮件上的每一次消费者互动来提供卓越的消费者体验和个性化营销传播。他们根据消费者的生命周期阶段、偏好和行为对消费者进行细分,并通过多个渠道向他们提供个性化消息。他们还通过分析每次滑动、点击和点击其数字属性来了解消费者的产品偏好、活动绩效等,从而实现数据驱动的决策。他们使用 MoEngage 强大的分析功能来绘制消费者旅程并识别每个阶段的摩擦点。
运营影响
数量效益
Case Study missing?
Start adding your own!
Register with your work email and create a new case study profile for your business.
相关案例.
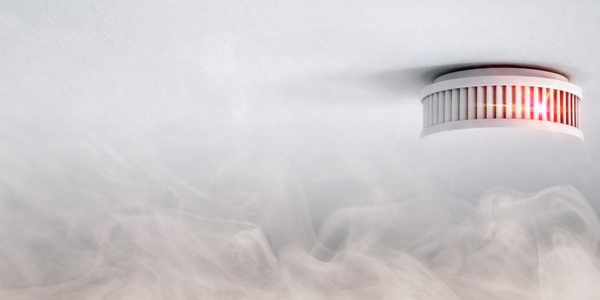
Case Study
Fire Alarm System and Remote Monitoring Sytem
Fire alarm systems are essential in providing an early warning in the event of fire. They help to save lives and protect property whilst also fulfilling the needs of insurance companies and government departments.Fire alarm systems typically consist of several inter-linked components, such as smoke detectors, heat detector, carbon monoxide, manual call points, sounders, alarm and buzzer. The fire alarm system should give immediate information in order to prevent the fire spread and protect live and property.To get maximum protection a shoe manufacturer in Indonesia opted for a new fire alarm system to monitor 13 production sites spread over 160 hectars. Although the company had an existing fire alarm system, it could not be monitored remotely.It was essential that the new system would be able to be monitored from a central control room. It needed to be able to connect to the existing smoke detector and manual call point. Information should be easily collected and passed on to the Supervisory Control and Data Acquisition (SCADA) system. Furthermore, the system should have several features such as alarm management, auto reporting, being connected to many client computers without additional cost, and run 24/7 without fails. The company also needed a system which could be implemented without changing the architecture of the existing fire alarm system.
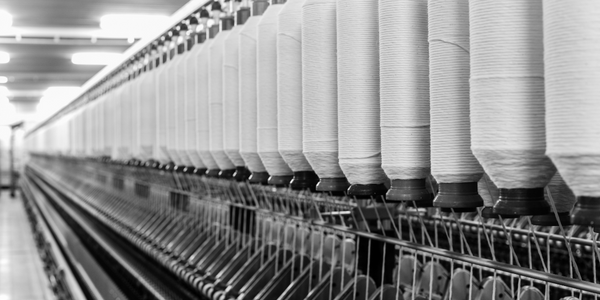
Case Study
IoT Applications and Upgrades in Textile Plant
At any given time, the textile company’s manufacturing facility has up to 2,000 textile carts in use. These carts are pushed from room to room, carrying materials or semi-finished products. Previously, a paper with a hand-written description was attached to each cart. This traditional method of processing made product tracking extremely difficult. Additionally, making sure that every cart of materials or semi-finished products went to its correct processing work station was also a problem. Therefore, the company desired an intelligent solution for tracking assets at their factories. They also wanted a solution that would help them collect process data so they could improve their manufacturing efficiency.
.png)
Case Study
Improving Vending Machine Profitability with the Internet of Things (IoT)
The vending industry is undergoing a sea change, taking advantage of new technologies to go beyond just delivering snacks to creating a new retail location. Intelligent vending machines can be found in many public locations as well as company facilities, selling different types of goods and services, including even computer accessories, gold bars, tickets, and office supplies. With increasing sophistication, they may also provide time- and location-based data pertaining to sales, inventory, and customer preferences. But at the end of the day, vending machine operators know greater profitability is driven by higher sales and lower operating costs.
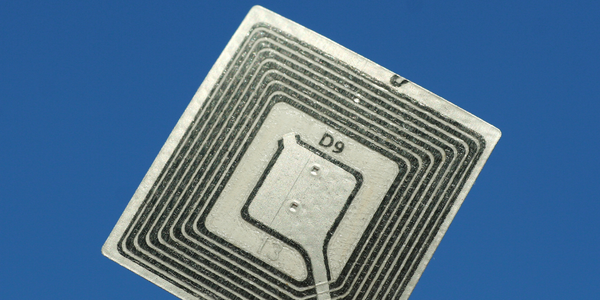
Case Study
Retailer Uses RFID Scanner to Improve Efficiency
Patrizia Pepe wished to improve the logistics of their warehouse: accepting incoming goods from their production sites, movement of items throughout
the warehouse, and packaging of goods for distribution to the retail locations. They initially tried to use barcodes for this function. Because barcodes must be individually scanned within a line-of-sight, the acceptance of goods coming into the warehouse was too time consuming. Working with the University of Florence, Patrizia Pepe instituted a five-month pilot project beginning in August of 2009 to test the validity of an RFID solution. The pilot involved tagging of about 60,000 items for the second seasonal collection, and convinced the company to move forward with tagging all items.