公司规模
Mid-size Company
地区
- America
国家
- United States
产品
- Plex Manufacturing Cloud
技术栈
- Cloud-based ERP
- Real-time Data Access
实施规模
- Enterprise-wide Deployment
影响指标
- Productivity Improvements
- Customer Satisfaction
- Cost Savings
技术
- 功能应用 - 企业资源规划系统 (ERP)
- 功能应用 - 制造执行系统 (MES)
适用行业
- 汽车
- 电子产品
适用功能
- 质量保证
- 商业运营
用例
- 库存管理
- 预测性维护
- 过程控制与优化
服务
- 系统集成
- 培训
关于客户
A&K Finishing is a privately owned company established in 1990, specializing in providing high-quality plastic paint solutions for various industries, including automotive, office furniture, electronics, and commercial sectors. The company is known for its commitment to lean manufacturing and just-in-time delivery, ensuring products are delivered with zero defects on time. A&K Finishing utilizes advanced technology, such as robotic painting and open spray booths, to maintain its reputation for quality and efficiency. The company paints interior automotive components for some of the largest automakers in the nation, following a workflow that involves receiving molded parts, decorating them, finishing with paint, and sending them to tier-1 auto suppliers. A&K Finishing's dedication to being 'First to Finish, with Quality' drives its operations and customer service.
挑战
A&K Finishing faced several challenges in its operations, primarily due to outdated systems and fragmented processes. The company relied heavily on spreadsheets and a Great Plains accounting system, which led to inefficiencies and inaccuracies. Physical inventory counts were time-consuming and often inaccurate, causing delays and disruptions in the production process. Managers spent a significant amount of time on data entry, up to 85%, which detracted from their ability to focus on strategic tasks. Quality control issues were prevalent, leading to production delays and impacting customer satisfaction. The lack of a unified system made it difficult for departments to share data seamlessly, resulting in fragmented business processes. A&K Finishing recognized the need for a robust ERP system to streamline operations, improve data accuracy, and enhance overall efficiency.
解决方案
To address its operational challenges, A&K Finishing implemented the Plex Manufacturing Cloud, a cloud-based ERP system that offered a comprehensive solution for managing business processes. The decision to move to a cloud platform was driven by the need for real-time access to business information and the ability to unify data across departments. The Plex Manufacturing Cloud provided A&K Finishing with instant access to real-time information, reducing the need for manual data entry and allowing managers to focus on strategic planning. The system's functionality, combined with the support of a vibrant customer community, made it an appealing choice for A&K Finishing. The company engaged Cumulus Consulting for implementation, benefiting from a 'train the trainer' approach that facilitated a smooth transition. The Plex system enabled A&K Finishing to digitize its operations, moving from manual data entry to a virtually paperless shop floor. Operators used computer terminals to scan products, ensuring accurate data capture and enhancing product quality. The system also provided tools for quality control, allowing the company to enforce its standards and reduce scrap rates.
运营影响
数量效益
Case Study missing?
Start adding your own!
Register with your work email and create a new case study profile for your business.
相关案例.
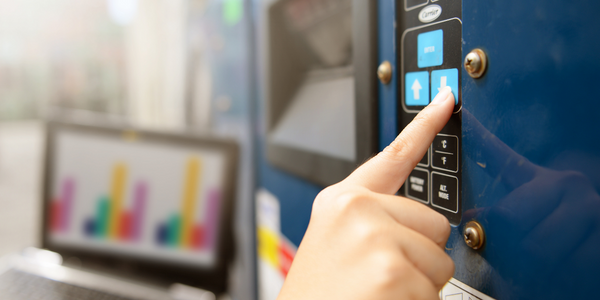
Case Study
Remote Temperature Monitoring of Perishable Goods Saves Money
RMONI was facing temperature monitoring challenges in a cold chain business. A cold chain must be established and maintained to ensure goods have been properly refrigerated during every step of the process, making temperature monitoring a critical business function. Manual registration practice can be very costly, labor intensive and prone to mistakes.
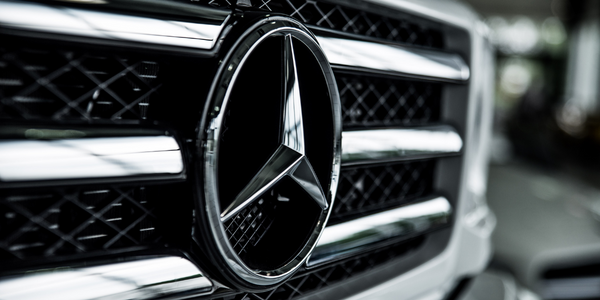
Case Study
Integral Plant Maintenance
Mercedes-Benz and his partner GAZ chose Siemens to be its maintenance partner at a new engine plant in Yaroslavl, Russia. The new plant offers a capacity to manufacture diesel engines for the Russian market, for locally produced Sprinter Classic. In addition to engines for the local market, the Yaroslavl plant will also produce spare parts. Mercedes-Benz Russia and his partner needed a service partner in order to ensure the operation of these lines in a maintenance partnership arrangement. The challenges included coordinating the entire maintenance management operation, in particular inspections, corrective and predictive maintenance activities, and the optimizing spare parts management. Siemens developed a customized maintenance solution that includes all electronic and mechanical maintenance activities (Integral Plant Maintenance).