公司规模
Large Corporate
地区
- America
国家
- United States
产品
- AiM from AssetWorks
- FuelFocus from AssetWorks
技术栈
- Web-based Integrated Workplace Management System
- UNIX system
实施规模
- Enterprise-wide Deployment
影响指标
- Cost Savings
- Productivity Improvements
技术
- 应用基础设施与中间件 - 数据交换与集成
适用行业
- 教育
适用功能
- 设施管理
- 维护
用例
- 楼宇自动化与控制
- 预测性维护
- 库存管理
服务
- 系统集成
- 软件设计与工程服务
关于客户
Appalachian State University (ASU) is a pioneering institution located in the scenic Blue Ridge Mountains of western North Carolina. The university boasts a student population greater than that of the neighboring hamlet of Boone, a town named for legendary American revolutionary war veteran, pioneer, explorer and politician Daniel Boone. ASU is a pioneering institution that continues to explore new paths to success. This pioneering spirit carries over to how business is conducted at ASU, and although insightful business decision are often made behind the scenes, the success of ASU’s facilities management program merits a closer look. ASU’s Physical Plant Department is responsible for creating and maintaining an aesthetically pleasing, environmentally sustainable and energy efficient environment for the campus community by maintaining campus buildings and grounds, providing auxiliary services and preserving the value of the university’s infrastructure.
挑战
ASU’s Physical Plant Department is responsible for creating and maintaining an aesthetically pleasing, environmentally sustainable and energy efficient environment for the campus community by maintaining campus buildings and grounds, providing auxiliary services and preserving the value of the university’s infrastructure. Prior to installing a Web-based Integrated Workplace Management System (IWMS), ASU relied on a homegrown UNIX system that was originally developed in the 1980’s and ran on a legacy DEC server. Over the years, this system became increasingly difficult to maintain and update, because much of the information was deeply hard-coded into the software. Sharing information inter-departmentally was difficult and the existing library of reports was inadequate. ASU realized a modern maintenance management system was needed to keep pace with the demands of a growing university. The university initiated a search for a system that would enable them to effectively share data and quickly make informed business decisions given the daily operational demands facing the Physical Plant Department.
解决方案
ASU initiated a search for a system that would enable them to effectively share data and quickly make informed business decisions given the daily operational demands facing the Physical Plant Department. It needed to be a scalable system that could turn around over 12,000 maintenance service requests annually, readily interface with the university’s SCT/ Banner ERP, integrate with ASU’s fuel management system, continuously update preventive maintenance schedules for over 6,000 pieces of equipment and provide inventory control and billing for over 10,000 line items. After a competitive procurement process that included on-site demonstrations and a full analysis of the proposed systems, ASU selected AiM from AssetWorks. ASU went live with AiM in August of 2008. The system was initially deployed by the Physical Plant Department with an eye toward focusing on work management. Today, AiM is used by several university departments, including Housing, Campus Police, Emergency Management and the Central Warehouse.
运营影响
数量效益
Case Study missing?
Start adding your own!
Register with your work email and create a new case study profile for your business.
相关案例.
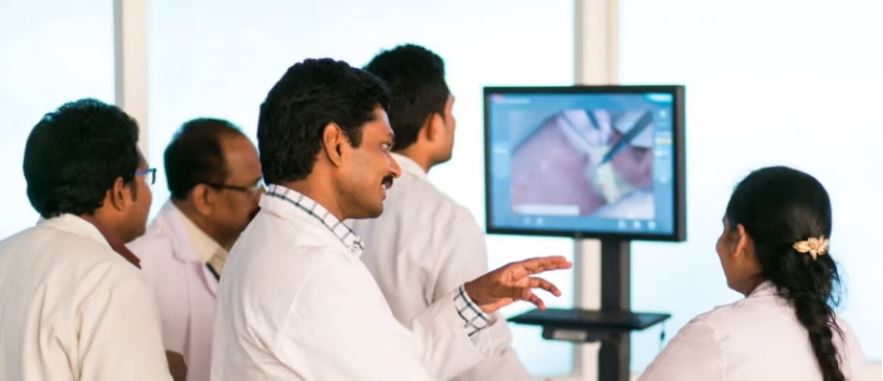
Case Study
Revolutionizing Medical Training in India: GSL Smart Lab and the LAP Mentor
The GSL SMART Lab, a collective effort of the GSL College of Medicine and the GSL College of Nursing and Health Science, was facing a challenge in providing superior training to healthcare professionals. As clinical medicine was becoming more focused on patient safety and quality of care, the need for medical simulation to bridge the educational gap between the classroom and the clinical environment was becoming increasingly apparent. Dr. Sandeep Ganni, the director of the GSL SMART Lab, envisioned a world-class surgical and medical training center where physicians and healthcare professionals could learn skills through simulation training. He was looking for different simulators for different specialties to provide both basic and advanced simulation training. For laparoscopic surgery, he was interested in a high fidelity simulator that could provide basic surgical and suturing skills training for international accreditation as well as specific hands-on training in complex laparoscopic procedures for practicing physicians in India.
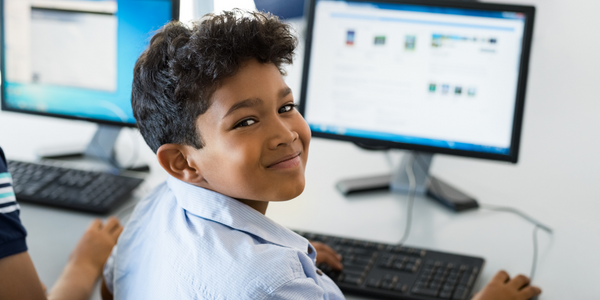
Case Study
IoT platform Enables Safety Solutions for U.S. School Districts
Designed to alert drivers when schoolchildren are present, especially in low-visibility conditions, school-zone flasher signals are typically updated manually at each school. The switching is based on the school calendar and manually changed when an unexpected early dismissal occurs, as in the case of a weather-event altering the normal schedule. The process to reprogram the flashers requires a significant effort by school district personnel to implement due to the large number of warning flashers installed across an entire school district.
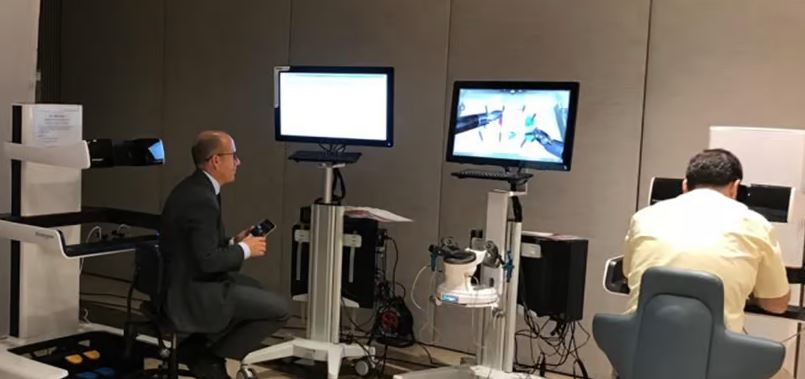
Case Study
Implementing Robotic Surgery Training Simulator for Enhanced Surgical Proficiency
Fundacio Puigvert, a leading European medical center specializing in Urology, Nephrology, and Andrology, faced a significant challenge in training its surgical residents. The institution recognized the need for a more standardized and comprehensive training curriculum, particularly in the area of robotic surgery. The challenge was underscored by two independent studies showing that less than 5% of residents in Italian and German residency programs could perform major or complex procedures by the end of their residency. The institution sought to establish a virtual reality simulation lab that would include endourological, laparoscopic, and robotic platforms. However, they needed a simulator that could replicate both the hardware and software of the robotic Da Vinci console used in the operating room, without being connected to the actual physical console. They also required a system that could provide both basic and advanced simulation training, and a metrics system to assess the proficiency of the trainees before they performed surgical procedures in the operating theater.
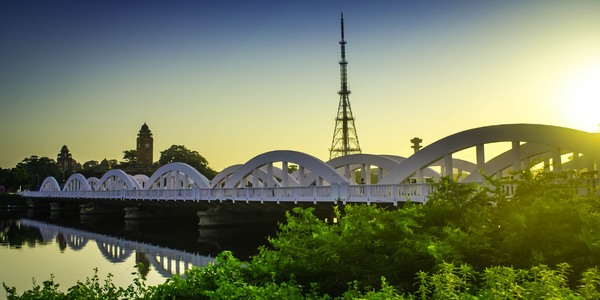
Case Study
Edinburgh Napier University streamlines long-distance learning with Cisco WebEX
• Geographically dispersed campus made in-person meetings costly and inconvenient.• Distance-learning programs in Malaysia, India, and China required dependable, user-friendly online tools to maximize interaction in collaborative workspaces.• Virtual learning environment required a separate sign-in process, resulting in a significant administrative burden for IT staff and limited adoption of collaboration technology.
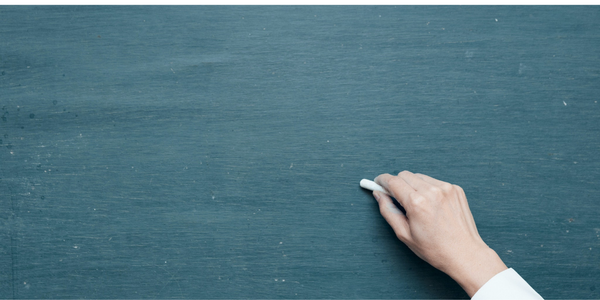
Case Study
8x increased productivity with VKS
Before VKS, a teacher would spend a lot of time showing a group of 22 students how to build a set of stairs within a semester of 120 hours. Along with not leaving the teacher much time to provide one-on-one support for each student to properly learn carpentry, it also left a considerable amount of room for error. Key information would be misinterpreted or lost as the class was taught in the typical show-and-tell way.
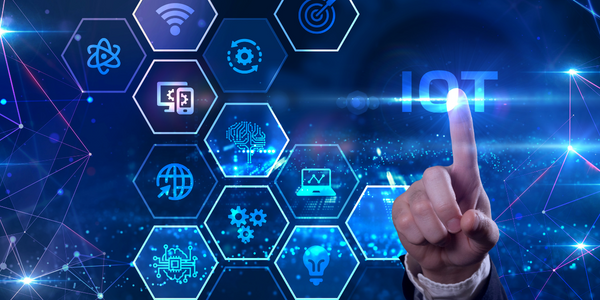
Case Study
Scalable IoT Empowering GreenFlex's Sustainable Growth
GreenFlex, a company that supports sustainable development, decarbonization, and energy efficiency, faced several challenges in its quest to expand its business. The company needed to deploy a robust and sustainable IoT technology to support its growth. It was crucial for them to monitor and control devices at customer sites in a safe and reliable manner. They also needed to integrate devices across a range of communication protocols and gather and act on data to meet efficiency targets. GreenFlex had previously built IoT capabilities into its digital platform, GreenFlexIQ, to monitor and manage customer sites remotely. However, they soon realized that they needed a new platform to support their ambitions. They needed a platform that could scale to connect more devices for production management and make it easier for the operations team to manage devices in the field.