aPriori Supports Arrival’s “Microfactory” Approach to Manufacturing Zero-Emission Vehicles
公司规模
Large Corporate
地区
- America
- Europe
国家
- United Kingdom
- United States
产品
- aPriori Cost Insight Design (CID)
- aPriori Cost Insight Generate (CIG)
技术栈
- Manufacturing Simulation
- PLM System Integration
实施规模
- Enterprise-wide Deployment
影响指标
- Cost Savings
- Productivity Improvements
- Waste Reduction
技术
- 分析与建模 - 预测分析
- 应用基础设施与中间件 - 数据交换与集成
- 功能应用 - 制造执行系统 (MES)
适用行业
- 汽车
适用功能
- 产品研发
- 采购
用例
- 自动化制造系统
- 预测性维护
- 供应链可见性(SCV)
服务
- 软件设计与工程服务
- 系统集成
关于客户
Arrival is a company dedicated to developing cost-competitive electric vehicles (EVs) through innovative manufacturing approaches. They have introduced the concept of 'Microfactories,' which are small, flexible, and distributed manufacturing units designed to support localized supply chains and produce vehicles tailored to specific regional needs. This approach allows Arrival to overcome the traditional tension between cost and customization in the automotive industry. By leveraging Microfactories, Arrival aims to produce vehicles that meet the functional and budgetary requirements of different regions, organizations, and use cases. The company is focused on driving down the cost of products wherever possible, and their cost engineering group is dedicated to implementing systematic use of manufacturing cost modeling tools to support this mission-critical focus on cost optimization. Arrival's innovative approach to manufacturing and their commitment to cost efficiency make them a unique player in the automotive industry.
挑战
Arrival’s goal of developing unprecedented cost-competitive EVs fuels an organizational culture dedicated to driving down the cost of products wherever possible. Their cost engineering group wanted to implement systematic use of a manufacturing cost modeling tool capable of supporting this mission-critical focus on cost optimization. The Arrival Microfactory would also require these cost modeling capabilities to work quickly when scaling up new facilities, reflect regional variations in manufacturing cost drivers, and support manufacturability and cost analysis that could be configured to reflect the capabilities of local suppliers. Finally, it would need to bring the automation necessary to align with plans for an agile cost engineering team that can work cross-functionally across different manufacturing processes. Microfactories will be used to support not only localized supply chains, but products tuned to customer needs in local markets. Henry Ford famously proclaimed that customers could have cars “in any color as long as it is black.” Arrival plans to overcome this longstanding tension between cost and customization. Their vehicles can be custom-tailored to the functional and budgetary requirements of different regions, organizations, and use cases. The scale of traditional automotive manufacturing means that designs are only viable if they can command large global sales volume for years at a time. Because the Microfactory enables sustainable unit economics even at smaller production volumes, Arrival has the freedom to produce vehicles purpose-built for end user needs. If these needs change, the Microfactory has the agility required to adapt in short order.
解决方案
aPriori’s Cost Insight Design (CID) and Cost Insight Generate (CIG) products were introduced at Arrival to support their Design for Assembly work. Early successes led Arrival’s newly created cost engineering group to see clear value in expanding aPriori’s footprint at the organizational level. Ultimately, Arrival wanted to establish a single source of truth for cost and manufacturability analysis. Arrival uses aPriori Cost Insight Design (CID) to identify manufacturability issues to meet or beat their cost targets on their designs. With no input required from the designer, aPriori’s Cost Insight Generate (CIG) automatically initiates a comprehensive manufacturing simulation as soon as the designer checks in a new or modified design to their PLM system. If some manufacturing anomaly is identified, CIG proactively notifies the designer with an email communication directly to their inbox. Either manually or by clicking on a hyperlink from the notification, CID allows the designer to quickly upload and evaluate the identified component or assembly. They can study design variants and different material, process, and sourcing options that could address the manufacturability issue identified, and publish the best options for review with the broader team.
运营影响
数量效益
Case Study missing?
Start adding your own!
Register with your work email and create a new case study profile for your business.
相关案例.
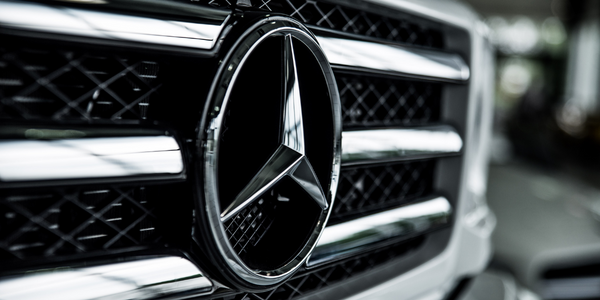
Case Study
Integral Plant Maintenance
Mercedes-Benz and his partner GAZ chose Siemens to be its maintenance partner at a new engine plant in Yaroslavl, Russia. The new plant offers a capacity to manufacture diesel engines for the Russian market, for locally produced Sprinter Classic. In addition to engines for the local market, the Yaroslavl plant will also produce spare parts. Mercedes-Benz Russia and his partner needed a service partner in order to ensure the operation of these lines in a maintenance partnership arrangement. The challenges included coordinating the entire maintenance management operation, in particular inspections, corrective and predictive maintenance activities, and the optimizing spare parts management. Siemens developed a customized maintenance solution that includes all electronic and mechanical maintenance activities (Integral Plant Maintenance).
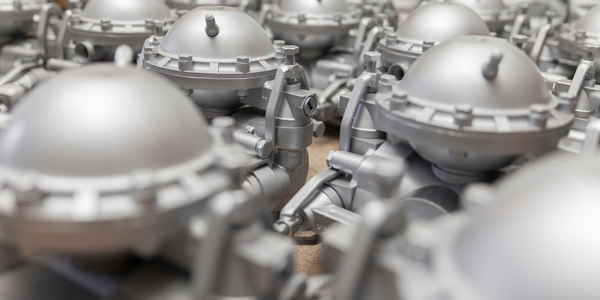
Case Study
Monitoring of Pressure Pumps in Automotive Industry
A large German/American producer of auto parts uses high-pressure pumps to deburr machined parts as a part of its production and quality check process. They decided to monitor these pumps to make sure they work properly and that they can see any indications leading to a potential failure before it affects their process.