公司规模
Large Corporate
地区
- Europe
国家
- Slovakia
- Switzerland
- Austria
- France
产品
- JDA Demand
- JDA Fulfillment
技术栈
- SAP ERP
实施规模
- Enterprise-wide Deployment
影响指标
- Cost Savings
- Customer Satisfaction
- Productivity Improvements
技术
- 平台即服务 (PaaS) - 数据管理平台
适用行业
- 汽车
- 建筑与基础设施
适用功能
- 物流运输
- 采购
用例
- 库存管理
- 供应链可见性(SCV)
服务
- 系统集成
关于客户
伍尔特国际是一家全球批发商,隶属于市值 75.2 亿欧元的伍尔特集团。该公司专门从事全球紧固件和装配材料的销售,包括 100,000 多种螺丝、螺丝配件、销钉和塞子、化工产品、家具和建筑配件、工具以及库存和拣选系统。伍尔特国际成立于 1964 年,是伍尔特集团的中央职能部门,负责全球所有伍尔特子公司的设立、收购、控股和管理,以及集中管理伍尔特德国境外所有子公司的所有采购活动。该公司从供应商处购买 97% 的伍尔特品牌产品,并在斯洛伐克设有重新包装设施。
挑战
Würth International 是一家专门销售紧固件和装配材料的全球批发商,其供应链面临挑战。由于仓库遍布欧洲各地,并且拥有许多独立的供应商,该公司在日常运营中对需求的透明度非常有限,无法支持其增长计划。当货物通过其供应链时,该公司经历了库存短缺和长时间延迟,即所谓的“牛鞭”效应。为了减少这些问题,该公司意识到需要一种新的解决方案,以便深入了解客户需求并实现更高效、自动化的补货流程。Würth International 需要一种方法来提高需求可见性,并使公司能够获得由此带来的好处,包括减少库存、减少产品过时、提高客户服务水平和采购,以及实现物料管理效率。
解决方案
Würth International 选择 JDA Software Group 作为其首选供应商,从 JDA 的 Intelligent Fulfillment™ 解决方案中授权 JDA Demand 和 JDA Fulfillment。该公司于 2007 年 5 月在法国启动了 JDA 解决方案的试点实施。考虑到该公司计划在未来几年内推出 SAP 的 ERP 系统,包括将该系统与其许多供应商连接起来,JDA 与 Würth International 合作开发界面,以成功整合系统并从每个系统中获得最大收益。该公司于 2008 年 7 月在客户位于法国的两个中央仓库以及 Würth International 位于瑞士和斯洛伐克的中央仓库开始使用 JDA Demand。2008 年 9 月,Würth International 也开始使用 JDA Fulfillment。因此,现在所有采购和补货流程都在 JDA 解决方案上运行。
运营影响
数量效益
Case Study missing?
Start adding your own!
Register with your work email and create a new case study profile for your business.
相关案例.
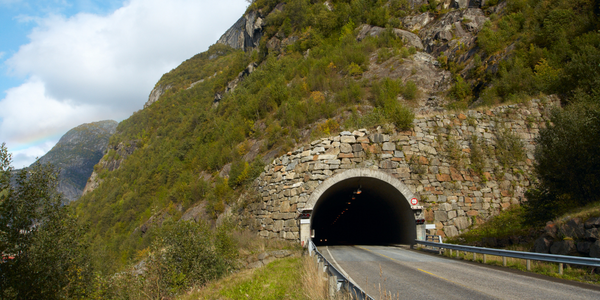
Case Study
IoT System for Tunnel Construction
The Zenitaka Corporation ('Zenitaka') has two major business areas: its architectural business focuses on structures such as government buildings, office buildings, and commercial facilities, while its civil engineering business is targeted at structures such as tunnels, bridges and dams. Within these areas, there presented two issues that have always persisted in regard to the construction of mountain tunnels. These issues are 'improving safety" and "reducing energy consumption". Mountain tunnels construction requires a massive amount of electricity. This is because there are many kinds of electrical equipment being used day and night, including construction machinery, construction lighting, and ventilating fan. Despite this, the amount of power consumption is generally not tightly managed. In many cases, the exact amount of power consumption is only ascertained when the bill from the power company becomes available. Sometimes, corporations install demand-monitoring equipment to help curb the maximum power demanded. However, even in these cases, the devices only allow the total volume of power consumption to be ascertained, or they may issue warnings to prevent the contracted volume of power from being exceeded. In order to tackle the issue of reducing power consumption, it was first necessary to obtain an accurate breakdown of how much power was being used in each particular area. In other words, we needed to be able to visualize the amount of power being consumed. Safety, was also not being managed very rigorously. Even now, tunnel construction sites often use a 'name label' system for managing entry into the work site. Specifically, red labels with white reverse sides that bear the workers' names on both sides are displayed at the tunnel work site entrance. The workers themselves then flip the name label to the appropriate side when entering or exiting from the work site to indicate whether or not they are working inside the tunnel at any given time. If a worker forgets to flip his or her name label when entering or exiting from the tunnel, management cannot be performed effectively. In order to tackle the challenges mentioned above, Zenitaka decided to build a system that could improve the safety of tunnel construction as well as reduce the amount of power consumed. In other words, this new system would facilitate a clear picture of which workers were working in each location at the mountain tunnel construction site, as well as which processes were being carried out at those respective locations at any given time. The system would maintain the safety of all workers while also carefully controlling the electrical equipment to reduce unnecessary power consumption. Having decided on the concept, our next concern was whether there existed any kind of robust hardware that would not break down at the construction work site, that could move freely in response to changes in the working environment, and that could accurately detect workers and vehicles using radio frequency identification (RFID). Given that this system would involve many components that were new to Zenitaka, we decided to enlist the cooperation of E.I.Sol Co., Ltd. ('E.I.Sol') as our joint development partner, as they had provided us with a highly practical proposal.
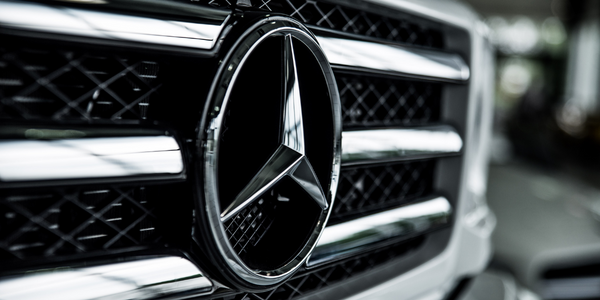
Case Study
Integral Plant Maintenance
Mercedes-Benz and his partner GAZ chose Siemens to be its maintenance partner at a new engine plant in Yaroslavl, Russia. The new plant offers a capacity to manufacture diesel engines for the Russian market, for locally produced Sprinter Classic. In addition to engines for the local market, the Yaroslavl plant will also produce spare parts. Mercedes-Benz Russia and his partner needed a service partner in order to ensure the operation of these lines in a maintenance partnership arrangement. The challenges included coordinating the entire maintenance management operation, in particular inspections, corrective and predictive maintenance activities, and the optimizing spare parts management. Siemens developed a customized maintenance solution that includes all electronic and mechanical maintenance activities (Integral Plant Maintenance).
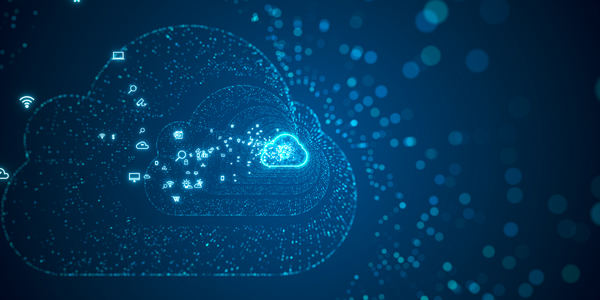
Case Study
Splunk Partnership Ties Together Big Data & IoT Services
Splunk was faced with the need to meet emerging customer demands for interfacing IoT projects to its suite of services. The company required an IoT partner that would be able to easily and quickly integrate with its Splunk Enterprise platform, rather than allocating development resources and time to building out an IoT interface and application platform.