公司规模
Large Corporate
地区
- Europe
- America
- Asia
国家
- Sweden
- United States
产品
- Assure iTERA HA
- IBM System i
- JD Edwards ERP
技术栈
- Remote Journaling
- Role-Swap Process
实施规模
- Enterprise-wide Deployment
影响指标
- Customer Satisfaction
- Productivity Improvements
技术
- 功能应用 - 企业资源规划系统 (ERP)
- 应用基础设施与中间件 - 数据交换与集成
适用行业
- 汽车
适用功能
- 商业运营
- 物流运输
用例
- 预测性维护
- 远程资产管理
服务
- 系统集成
- 软件设计与工程服务
关于客户
Autoliv is a global leader in automotive safety, headquartered in Stockholm, Sweden. The company employs approximately 42,000 people and is renowned for its pioneering work in developing seatbelts and airbags. Autoliv's product portfolio extends to anti-whiplash systems, safety electronics, rollover protection systems, steering wheels with airbags, and child seats. The company serves all major automobile manufacturers worldwide, operating through 80 subsidiaries and joint ventures across 28 countries. Autoliv's commitment to safety and innovation is evident in its extensive testing capabilities, with 20 crash test tracks located in 12 countries. The company is dedicated to adhering to stringent on-time delivery requirements, as its contracts with automakers often include penalties for late shipments. Autoliv's global presence and reputation for quality make it a key player in the automotive safety industry.
挑战
Autoliv, a global leader in automotive safety, faces significant challenges in maintaining stringent on-time delivery requirements for its products, which include seatbelts, airbags, and other safety systems. The company operates in a highly competitive environment where downtime can lead to missed delivery deadlines and measurable revenue losses. Contracts with automakers often include penalties for late shipments, making it crucial for Autoliv to minimize both planned and unplanned downtime. The company's reliance on JD Edwards ERP applications for critical functions such as financial management, inventory, customer service, and purchasing further underscores the need for a reliable high availability (HA) solution. With operations spanning 13 manufacturing facilities worldwide and processing up to 70 million daily transactions, Autoliv's IT infrastructure must be robust and resilient to ensure continuous operations and meet customer expectations.
解决方案
To address its high availability needs, Autoliv's ERP team explored various HA solutions and ultimately selected Assure iTERA HA from Precisely. The decision was influenced by the product's ability to minimize latency, even at high transaction levels, through the use of remote journaling. Additionally, the role-swap process offered by Assure iTERA HA was found to be simple and effective, providing a seamless transition in the event of a system failure. The cost-effectiveness of the solution further solidified Autoliv's choice. Following the installation of Assure iTERA HA, Autoliv experienced immediate benefits, including a significant reduction in apply-latency issues and decreased time required for system monitoring and management. The true test of the solution's effectiveness came just six weeks after installation when Autoliv's production System i experienced a critical failure due to a backplane issue. Despite logistical challenges caused by wildfires in San Diego, Autoliv's IT team successfully initiated a failover to the mirrored backup machine, ensuring uninterrupted operations. With guidance from Precisely's 24/7 support team, the failover process was completed swiftly, allowing all business-critical applications to remain fully functional. As a result, Autoliv maintained its commitment to on-time deliveries, with no customer shipments delayed and no transactions lost.
运营影响
数量效益
Case Study missing?
Start adding your own!
Register with your work email and create a new case study profile for your business.
相关案例.
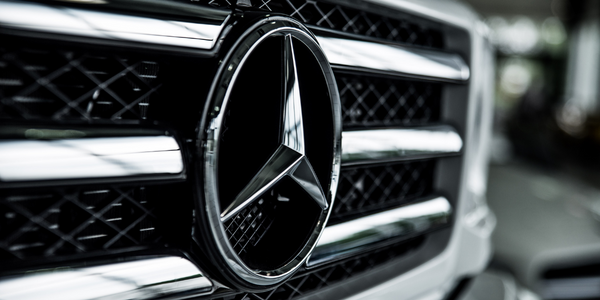
Case Study
Integral Plant Maintenance
Mercedes-Benz and his partner GAZ chose Siemens to be its maintenance partner at a new engine plant in Yaroslavl, Russia. The new plant offers a capacity to manufacture diesel engines for the Russian market, for locally produced Sprinter Classic. In addition to engines for the local market, the Yaroslavl plant will also produce spare parts. Mercedes-Benz Russia and his partner needed a service partner in order to ensure the operation of these lines in a maintenance partnership arrangement. The challenges included coordinating the entire maintenance management operation, in particular inspections, corrective and predictive maintenance activities, and the optimizing spare parts management. Siemens developed a customized maintenance solution that includes all electronic and mechanical maintenance activities (Integral Plant Maintenance).
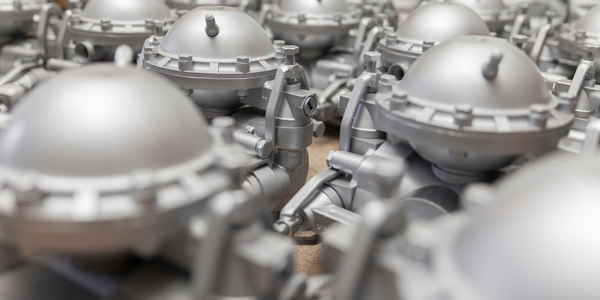
Case Study
Monitoring of Pressure Pumps in Automotive Industry
A large German/American producer of auto parts uses high-pressure pumps to deburr machined parts as a part of its production and quality check process. They decided to monitor these pumps to make sure they work properly and that they can see any indications leading to a potential failure before it affects their process.