公司规模
Mid-size Company
地区
- America
国家
- United States
产品
- Plex Manufacturing Cloud
技术栈
- Real-time Data Tracking
- Inventory Management Systems
实施规模
- Enterprise-wide Deployment
影响指标
- Productivity Improvements
- Cost Savings
- Customer Satisfaction
技术
- 功能应用 - 企业资源规划系统 (ERP)
- 分析与建模 - 实时分析
适用功能
- 商业运营
- 质量保证
用例
- 库存管理
- 机器状态监测
- 过程控制与优化
服务
- 系统集成
- 软件设计与工程服务
关于客户
Avon Machining, headquartered in Shelby Township, Michigan, is a prominent manufacturer of precision-machined components and subassemblies for heavy industrial equipment manufacturers across North America and beyond. The company acquired the assets of Avon Gear in May 2017, further solidifying its position in the industry. Avon Machining operates in the general manufacturing sector, focusing on delivering high-quality products to its clients. With a commitment to innovation and efficiency, the company has experienced significant growth over the years. Its operations are characterized by a dedication to precision and quality, ensuring that its components meet the stringent requirements of its industrial clients. Avon Machining's strategic location in Michigan allows it to serve a wide range of customers, contributing to its reputation as a reliable and trusted partner in the manufacturing industry.
挑战
Avon Machining faced significant challenges due to its siloed operations. Each department, including engineering, production, quality, and accounting, maintained separate databases and spreadsheets, leading to a lack of integration and communication. This disjointed approach made it difficult to track, retrieve, and communicate critical data efficiently. The complexity and time consumption involved in compiling data were major hurdles. Additionally, errors in data entry, tracking, and reporting resulted in a lack of confidence in the data, preventing the company from gaining a clear picture of its performance. Management recognized the need for a solution that could seamlessly integrate across the enterprise and provide real-time information access. After evaluating several options, Avon Machining selected the Plex Manufacturing Cloud for its ability to connect and manage all areas of manufacturing operations.
解决方案
To address its operational challenges, Avon Machining implemented the Plex Manufacturing Cloud, a comprehensive solution designed to integrate and manage all aspects of manufacturing operations. This cloud-based platform provided Avon Machining with real-time visibility and tracking capabilities, enabling the company to efficiently manage costs and resources. The Plex Manufacturing Cloud tracks and records all physical events, including production, inventory status changes, receiving, subcontracting, and shipping, directly on the shop floor. Employees can log in at their work centers to record production details in real time, allowing for immediate identification and correction of defective parts. This real-time tracking capability has transformed Avon Machining's operations, providing shop floor managers with the tools to calculate costs accurately and retrieve important information such as the quantity of parts produced, production time, and quality metrics. Additionally, the Plex Manufacturing Cloud streamlined the process of identifying and flagging parts that require rework, significantly reducing the time and effort involved in tracking and managing rework processes. The availability of real-time data has also enhanced reporting and forecasting capabilities, allowing managers to make informed decisions and maintain steady growth.
运营影响
数量效益
Case Study missing?
Start adding your own!
Register with your work email and create a new case study profile for your business.
相关案例.
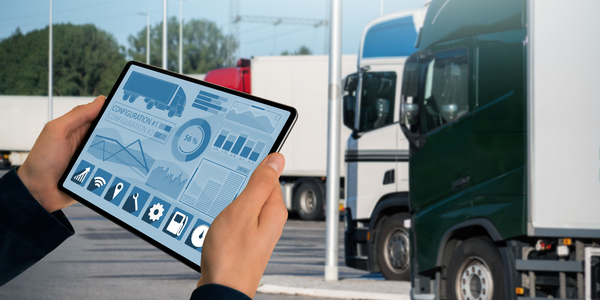
Case Study
IoT enabled Fleet Management with MindSphere
In view of growing competition, Gämmerler had a strong need to remain competitive via process optimization, reliability and gentle handling of printed products, even at highest press speeds. In addition, a digitalization initiative also included developing a key differentiation via data-driven services offers.
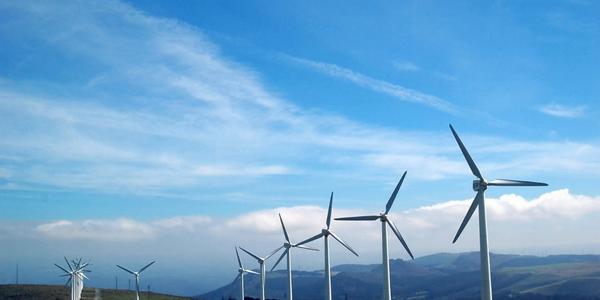
Case Study
Siemens Wind Power
Wind provides clean, renewable energy. The core concept is simple: wind turbines spin blades to generate power. However, today's systems are anything but simple. Modern wind turbines have blades that sweep a 120 meter circle, cost more than 1 million dollars and generate multiple megawatts of power. Each turbine may include up to 1,000 sensors and actuators – integrating strain gages, bearing monitors and power conditioning technology. The turbine can control blade speed and power generation by altering the blade pitch and power extraction. Controlling the turbine is a sophisticated job requiring many cooperating processors closing high-speed loops and implementing intelligent monitoring and optimization algorithms. But the real challenge is integrating these turbines so that they work together. A wind farm may include hundreds of turbines. They are often installed in difficult-to-access locations at sea. The farm must implement a fundamentally and truly distributed control system. Like all power systems, the goal of the farm is to match generation to load. A farm with hundreds of turbines must optimize that load by balancing the loading and generation across a wide geography. Wind, of course, is dynamic. Almost every picture of a wind farm shows a calm sea and a setting sun. But things get challenging when a storm goes through the wind farm. In a storm, the control system must decide how to take energy out of gusts to generate constant power. It must intelligently balance load across many turbines. And a critical consideration is the loading and potential damage to a half-billion-dollar installed asset. This is no environment for a slow or undependable control system. Reliability and performance are crucial.
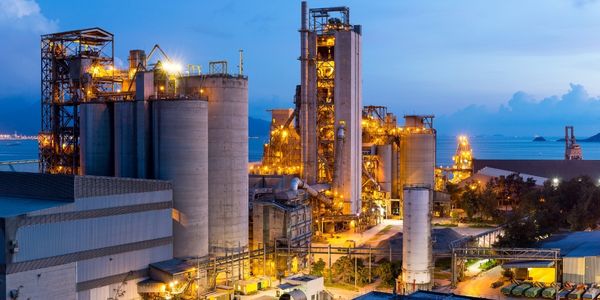
Case Study
System 800xA at Indian Cement Plants
Chettinad Cement recognized that further efficiencies could be achieved in its cement manufacturing process. It looked to investing in comprehensive operational and control technologies to manage and derive productivity and energy efficiency gains from the assets on Line 2, their second plant in India.
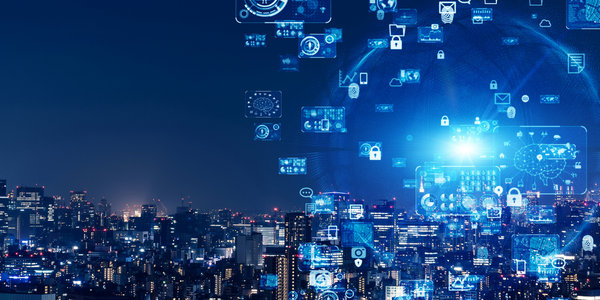
Case Study
Integration of PLC with IoT for Bosch Rexroth
The application arises from the need to monitor and anticipate the problems of one or more machines managed by a PLC. These problems, often resulting from the accumulation over time of small discrepancies, require, when they occur, ex post technical operations maintenance.
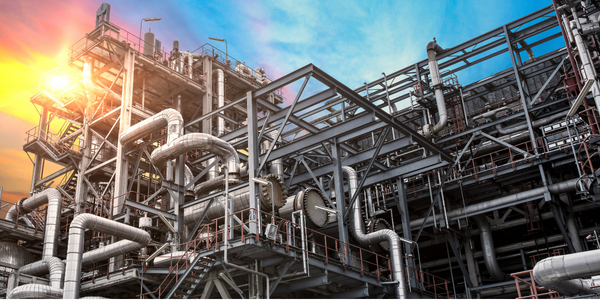
Case Study
Refinery Saves Over $700,000 with Smart Wireless
One of the largest petroleum refineries in the world is equipped to refine various types of crude oil and manufacture various grades of fuel from motor gasoline to Aviation Turbine Fuel. Due to wear and tear, eight hydrogen valves in each refinery were leaking, and each cost $1800 per ton of hydrogen vented. The plant also had leakage on nearly 30 flare control hydrocarbon valves. The refinery wanted a continuous, online monitoring system that could catch leaks early, minimize hydrogen and hydrocarbon production losses, and improve safety for maintenance.