CarMax Leverages Lean UX to Redesign its Shopping Experience with Axure
公司规模
Large Corporate
地区
- America
国家
- United States
产品
- Axure RP
技术栈
- Rapid Prototyping
- Wireframing
- Mockups
实施规模
- Enterprise-wide Deployment
影响指标
- Customer Satisfaction
- Digital Expertise
- Productivity Improvements
技术
- 分析与建模 - 预测分析
- 应用基础设施与中间件 - 数据可视化
- 功能应用 - 远程监控系统
适用行业
- 汽车
- 零售
适用功能
- 销售与市场营销
- 商业运营
用例
- 车队管理
- 预测性维护
服务
- 软件设计与工程服务
- 系统集成
- 培训
关于客户
CarMax disrupted the automotive retail industry more than 20 years ago by turning a universally dreaded life event— buying a used car—into one that’s straightforward and simple. Today, more than 16 million people visit CarMax.com each month to browse thousands of vehicles in its inventory, schedule test drives, secure financing, and more. For the twelfth consecutive year, CarMax ranked in Fortune Magazine’s 100 Best Companies to Work For in 2016.
挑战
Lean UX methods, although agile and flexible, can run counter to organizational principles needed to operate large organizations. For example, Lean UX relies on rapid learning through experimentation, but CarMax’s success partly depends on precise implementation of procedures to ensure a uniformly high-quality customer service experience across its 155 stores. CarMax needed to introduce Lean UX in a way that would not conflict with its existing culture, while still taking full advantage of the speed and adaptability of working lean.
解决方案
CarMax reorganized its digital group to operate more like a lean startup. In 2014, it created an Interaction Design Team to collaborate with the company’s other departments, including Marketing, Legal, Human Resources and Sales. The team leveraged Axure RP in two ways: Develop rapid prototypes to quickly test and validate new designs with users, and create wireframes, mockups and prototypes used to communicate design concepts with other departments and inform the company as a whole during monthly “Open Houses” when the team shared its progress and findings.
运营影响
数量效益
Case Study missing?
Start adding your own!
Register with your work email and create a new case study profile for your business.
相关案例.
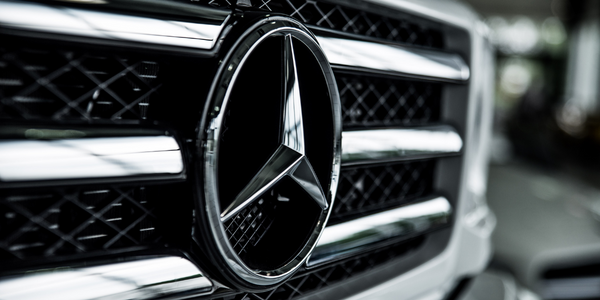
Case Study
Integral Plant Maintenance
Mercedes-Benz and his partner GAZ chose Siemens to be its maintenance partner at a new engine plant in Yaroslavl, Russia. The new plant offers a capacity to manufacture diesel engines for the Russian market, for locally produced Sprinter Classic. In addition to engines for the local market, the Yaroslavl plant will also produce spare parts. Mercedes-Benz Russia and his partner needed a service partner in order to ensure the operation of these lines in a maintenance partnership arrangement. The challenges included coordinating the entire maintenance management operation, in particular inspections, corrective and predictive maintenance activities, and the optimizing spare parts management. Siemens developed a customized maintenance solution that includes all electronic and mechanical maintenance activities (Integral Plant Maintenance).
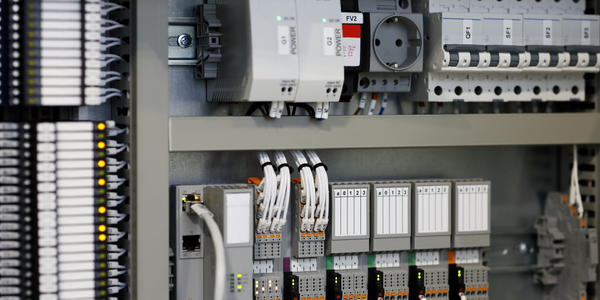
Case Study
Improving Production Line Efficiency with Ethernet Micro RTU Controller
Moxa was asked to provide a connectivity solution for one of the world's leading cosmetics companies. This multinational corporation, with retail presence in 130 countries, 23 global braches, and over 66,000 employees, sought to improve the efficiency of their production process by migrating from manual monitoring to an automatic productivity monitoring system. The production line was being monitored by ABB Real-TPI, a factory information system that offers data collection and analysis to improve plant efficiency. Due to software limitations, the customer needed an OPC server and a corresponding I/O solution to collect data from additional sensor devices for the Real-TPI system. The goal is to enable the factory information system to more thoroughly collect data from every corner of the production line. This will improve its ability to measure Overall Equipment Effectiveness (OEE) and translate into increased production efficiencies. System Requirements • Instant status updates while still consuming minimal bandwidth to relieve strain on limited factory networks • Interoperable with ABB Real-TPI • Small form factor appropriate for deployment where space is scarce • Remote software management and configuration to simplify operations