公司规模
Large Corporate
地区
- America
国家
- United States
产品
- Tableau Professional Services
- Tableau Server
- Salesforce CRM
技术栈
- Data Visualization
- Data Warehousing
- Cloud-based Solution
实施规模
- Enterprise-wide Deployment
影响指标
- Productivity Improvements
- Cost Savings
技术
- 应用基础设施与中间件 - 数据可视化
- 应用基础设施与中间件 - 数据交换与集成
适用行业
- 汽车
- 零售
适用功能
- 销售与市场营销
- 商业运营
用例
- 供应链可见性(SCV)
- 质量预测分析
服务
- 云规划/设计/实施服务
- 数据科学服务
关于客户
Cars.com is a division of Classified Ventures and is a leading destination for online car shoppers. The platform receives more than 11 million visits each month and offers credible and easy-to-understand information from consumers and experts to help buyers formulate opinions on what to buy, where to buy and how much to pay for a car. The company's data warehouse and business intelligence team gathers and interprets site visitor data from these millions of monthly visitors. The data is stored in a 12-terabyte Teradata warehouse appliance. The company has a sales team of over 600 people who are required to do all of their work from within the cloud-based Salesforce solution.
挑战
Cars.com, a leading online car shopping platform, wanted to provide its salespeople with easy-to-access information about how their customers’ ads performed on the site. They also wanted to share similar information directly with its advertisers and internal business users. The company’s data warehouse and business intelligence team gathers and interprets site visitor data from the 11 million monthly visitors. Based on traffic volume, there is a significant amount of data stored in its 12-terabyte Teradata warehouse appliance. The company faced challenges in efficiently analyzing and visualizing this data for multiple audiences. Additionally, Cars.com best practices require that the more than 600-person sales team be able to do all of its work from within the cloud-based Salesforce solution.
解决方案
Cars.com turned to Tableau Professional Services for a data visualization and dashboarding tool that would help improve efficiencies and complement the existing reporting platform. The company decided to have two instances of Tableau Server: one “standard” deployment for within the Cars.com firewall and one external-facing instance that would publish to external channels. Tableau Professional Services consultants worked closely with both Cars.com data warehousing architects and the Salesforce CRM team to establish token authentication between Salesforce and the external-facing Tableau Server. The consultants also helped Wyderka’s team understand how to manage and maintain the two environments from the standpoint of migrating new dashboards through the Cars.com environment, from set-up to maintenance and managing security access.
运营影响
数量效益
Case Study missing?
Start adding your own!
Register with your work email and create a new case study profile for your business.
相关案例.
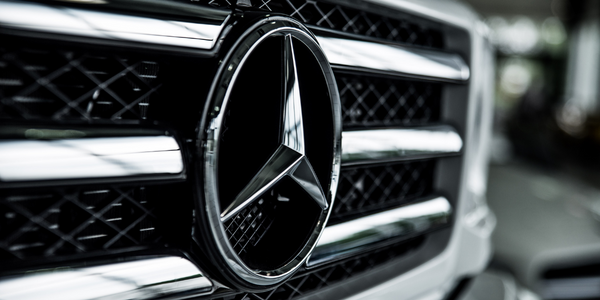
Case Study
Integral Plant Maintenance
Mercedes-Benz and his partner GAZ chose Siemens to be its maintenance partner at a new engine plant in Yaroslavl, Russia. The new plant offers a capacity to manufacture diesel engines for the Russian market, for locally produced Sprinter Classic. In addition to engines for the local market, the Yaroslavl plant will also produce spare parts. Mercedes-Benz Russia and his partner needed a service partner in order to ensure the operation of these lines in a maintenance partnership arrangement. The challenges included coordinating the entire maintenance management operation, in particular inspections, corrective and predictive maintenance activities, and the optimizing spare parts management. Siemens developed a customized maintenance solution that includes all electronic and mechanical maintenance activities (Integral Plant Maintenance).
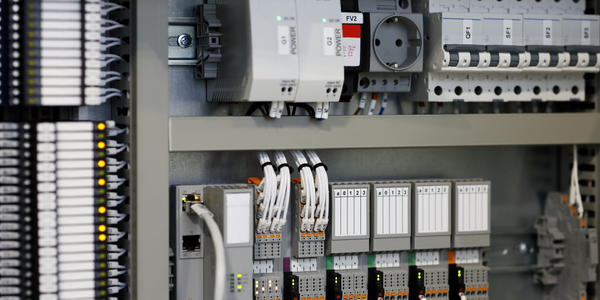
Case Study
Improving Production Line Efficiency with Ethernet Micro RTU Controller
Moxa was asked to provide a connectivity solution for one of the world's leading cosmetics companies. This multinational corporation, with retail presence in 130 countries, 23 global braches, and over 66,000 employees, sought to improve the efficiency of their production process by migrating from manual monitoring to an automatic productivity monitoring system. The production line was being monitored by ABB Real-TPI, a factory information system that offers data collection and analysis to improve plant efficiency. Due to software limitations, the customer needed an OPC server and a corresponding I/O solution to collect data from additional sensor devices for the Real-TPI system. The goal is to enable the factory information system to more thoroughly collect data from every corner of the production line. This will improve its ability to measure Overall Equipment Effectiveness (OEE) and translate into increased production efficiencies. System Requirements • Instant status updates while still consuming minimal bandwidth to relieve strain on limited factory networks • Interoperable with ABB Real-TPI • Small form factor appropriate for deployment where space is scarce • Remote software management and configuration to simplify operations