Chassis Systems Ltd Enhances Production Efficiency with Lighthouse Systems Shopfloor-Online
公司规模
Large Corporate
地区
- Europe
国家
- United Kingdom
产品
- Lighthouse Systems Shopfloor-Online
技术栈
- Wireless Network
- Rugged Tablet PCs
实施规模
- Enterprise-wide Deployment
影响指标
- Productivity Improvements
- Customer Satisfaction
技术
- 功能应用 - 制造执行系统 (MES)
- 网络与连接 - 无线局域网
适用行业
- 汽车
适用功能
- 质量保证
- 流程制造
用例
- 机器状态监测
- 预测性维护
- 远程资产管理
服务
- 系统集成
- 软件设计与工程服务
关于客户
Chassis Systems Ltd (CSL) is a joint venture between Dana and GKN, formed to produce chassis structures for Land Rover's Discovery and Range Rover Sport models. As a high-volume producer of complex, high-value parts, CSL places a strong emphasis on quality assurance. The company operates in the automotive industry, focusing on precision manufacturing processes that involve over 200 parts and more than 700 welds per chassis. Ensuring the quality of each product is crucial, and CSL has implemented procedures to measure and record inspection data across the production line. Historically, much of this data recording was done manually, which was time-consuming and prone to errors. CSL sought to improve efficiency, accuracy, and quality in its production processes by leveraging advanced technology solutions.
挑战
Chassis Systems Ltd (CSL) faced challenges in ensuring the quality of chassis structures for Land Rover's Discovery and Range Rover Sport models. The production process involved over 200 parts and more than 700 welds, requiring precise quality control. Historically, data recording was manual, making analysis cumbersome and time-consuming. CSL needed a solution to improve data visibility, automate processes, and increase inspection throughput. The manual system was inefficient, requiring operators to generate PDF documents for alerts, which consumed time and resources.
解决方案
CSL implemented Lighthouse Systems Shopfloor-Online to enhance data visibility and automate processes. The system's modular design allowed for future functionality additions, such as downtime analysis and maintenance management. Phase one focused on improving CMM data visibility, freeing up engineers' time and increasing inspection throughput by 50%. The system automated alerts for out-of-specification readings, eliminating manual PDF document generation. Phase two involved providing patrol inspectors with rugged tablet PCs connected to Shopfloor-Online over a wireless network. This allowed real-time reporting of visual inspections, replacing the manual catalog approach. Inspectors could now log checks and faults immediately, reducing training requirements and improving accuracy. Phase three ensured end-of-line quality checks, with faults input into Shopfloor-Online for detailed reporting and containment until repairs were made. The system provided a complete audit trail, enabling fault frequency and corrective action reporting.
运营影响
数量效益
Case Study missing?
Start adding your own!
Register with your work email and create a new case study profile for your business.
相关案例.
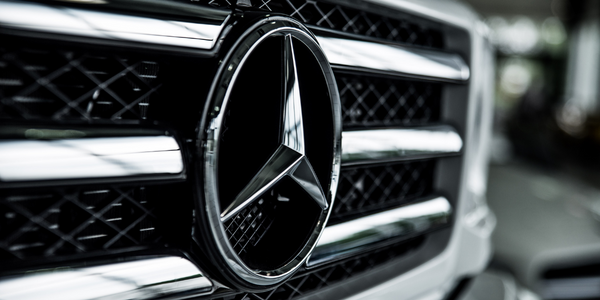
Case Study
Integral Plant Maintenance
Mercedes-Benz and his partner GAZ chose Siemens to be its maintenance partner at a new engine plant in Yaroslavl, Russia. The new plant offers a capacity to manufacture diesel engines for the Russian market, for locally produced Sprinter Classic. In addition to engines for the local market, the Yaroslavl plant will also produce spare parts. Mercedes-Benz Russia and his partner needed a service partner in order to ensure the operation of these lines in a maintenance partnership arrangement. The challenges included coordinating the entire maintenance management operation, in particular inspections, corrective and predictive maintenance activities, and the optimizing spare parts management. Siemens developed a customized maintenance solution that includes all electronic and mechanical maintenance activities (Integral Plant Maintenance).
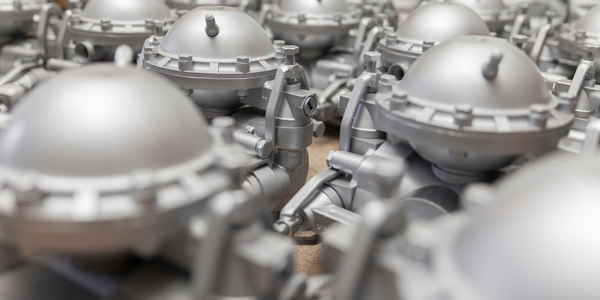
Case Study
Monitoring of Pressure Pumps in Automotive Industry
A large German/American producer of auto parts uses high-pressure pumps to deburr machined parts as a part of its production and quality check process. They decided to monitor these pumps to make sure they work properly and that they can see any indications leading to a potential failure before it affects their process.