Chefs on an ERP Roll
公司规模
Mid-size Company
地区
- America
国家
- United States
产品
- SYSPRO ERP
- Bar-Code for Impact
技术栈
- SQL Database
- Windows 2000
- RAID5
实施规模
- Enterprise-wide Deployment
影响指标
- Productivity Improvements
- Customer Satisfaction
- Cost Savings
技术
- 功能应用 - 企业资源规划系统 (ERP)
- 功能应用 - 库存管理系统
适用行业
- 食品与饮料
适用功能
- 商业运营
- 仓库和库存管理
用例
- 库存管理
- 资产跟踪
- 过程控制与优化
服务
- 系统集成
- 软件设计与工程服务
关于客户
Two Chefs On A Roll Inc., in Carson, California, manufactures a full range of custom savory and bakery products in a state-of-the-art certified organic manufacturing facility. Founded by Culinary Institute of America graduates Lori Daniel and Eliot Swartz in 1985, the company began operations as a wholesale dessert company specializing in distinctly American sweets. Today, Two Chefs On A Roll produces 7 bakery and 10 savory product lines totaling approximately 100 stock keeping units which are marketed globally to food manufacturers, retail food outlets, and casual dining food services. The company’s success is an example of perfect market timing and product ingenuity. Founders Daniel and Swartz saw the requirement for easy-to-prepare gourmet dishes comprised of all natural ingredients and set about to develop quality products to fill the need. Using a combination of their culinary studies, restaurant background, and extensive world travels, they developed unique, tasty product lines to satisfy the pallet and today’s fast-paced lifestyle. Currently, more than 195 employees extend the vision, supporting preservative-free, all natural food manufacturing, and an unswerving dedication to quality products, superior service, and doing what others won’t.
挑战
It was the move to a new manufacturing facility in April 2003 that prompted Two Chefs to conduct a search for a new ERP software solution. When they relocated their manufacturing plant, tripling their physical space and manufacturing capacity, they realized it was also time to implement an ERP solution to support growth and future needs. Two Chefs had been using outmoded accounting software, which was not only limited in functionality, but was no longer being supported. Their “wish list” for the new system included an integrated solution and support for bar coding to reflect industry standards.
解决方案
After an extensive search, the choice narrowed to SYSPRO ERP software. In addition to extensive integrated ERP capabilities, SYSPRO also offered bar-coding support. More importantly, it provided in-depth lot traceability and allergen tracking throughout the manufacturing process, key requirements for quality food processing. Assessing the impact of the software, the food manufacturer agrees that SYSPRO enables them to react more quickly to changing market conditions and customer requests with added flexibility and knowledge. The software is integral to Two Chef’s purchasing decisions and material requirements planning (MRP) recommendations. Previously, purchasing and MRP decisions were calculated manually. Consequently, they feel SYSPRO has added functionality and better control and reporting of our manufacturing processes. While they are still fine-tuning implementation and establishing new reporting formats, Two Chefs has gained the lot traceability and allergen tracking required, and can properly measure product and customer profitability. Presently, Two Chefs On A Roll is in the process of implementing a bar-coding system to enable scanning and tracking all product movements throughout the plant from receiving, raw material storage, work-in-process, finished goods, and shipping. When fully functional, the bar-coding solution will further improve internal control of inventory and produce more accurate inventory information on which it can base purchasing decisions and better manage cash flow.
运营影响
数量效益
Case Study missing?
Start adding your own!
Register with your work email and create a new case study profile for your business.
相关案例.

Case Study
The Kellogg Company
Kellogg keeps a close eye on its trade spend, analyzing large volumes of data and running complex simulations to predict which promotional activities will be the most effective. Kellogg needed to decrease the trade spend but its traditional relational database on premises could not keep up with the pace of demand.
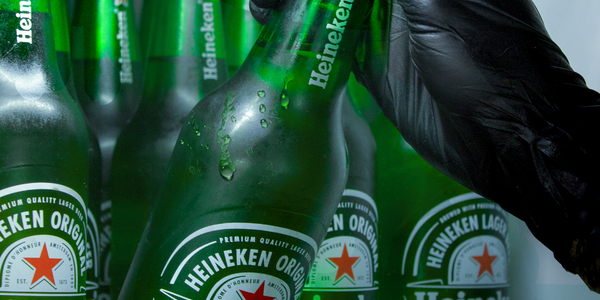
Case Study
HEINEKEN Uses the Cloud to Reach 10.5 Million Consumers
For 2012 campaign, the Bond promotion, it planned to launch the campaign at the same time everywhere on the planet. That created unprecedented challenges for HEINEKEN—nowhere more so than in its technology operation. The primary digital content for the campaign was a 100-megabyte movie that had to play flawlessly for millions of viewers worldwide. After all, Bond never fails. No one was going to tolerate a technology failure that might bruise his brand.Previously, HEINEKEN had supported digital media at its outsourced datacenter. But that datacenter lacked the computing resources HEINEKEN needed, and building them—especially to support peak traffic that would total millions of simultaneous hits—would have been both time-consuming and expensive. Nor would it have provided the geographic reach that HEINEKEN needed to minimize latency worldwide.
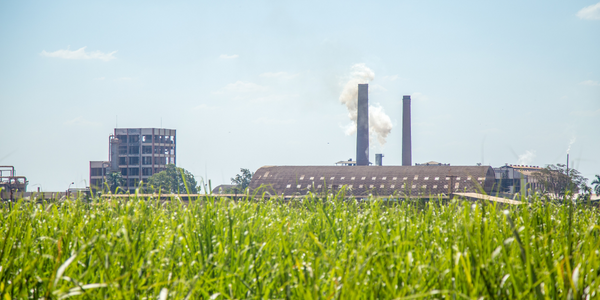
Case Study
Energy Management System at Sugar Industry
The company wanted to use the information from the system to claim under the renewable energy certificate scheme. The benefit to the company under the renewable energy certificates is Rs 75 million a year. To enable the above, an end-to-end solution for load monitoring, consumption monitoring, online data monitoring, automatic meter data acquisition which can be exported to SAP and other applications is required.
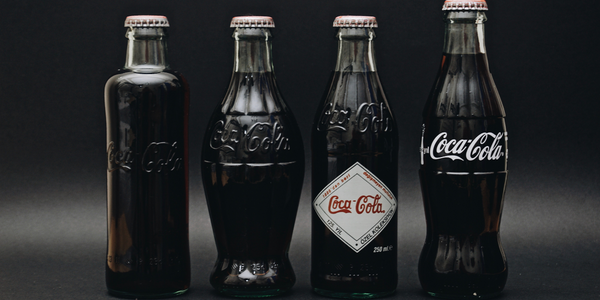
Case Study
Coca Cola Swaziland Conco Case Study
Coco Cola Swaziland, South Africa would like to find a solution that would enable the following results: - Reduce energy consumption by 20% in one year. - Formulate a series of strategic initiatives that would enlist the commitment of corporate management and create employee awareness while helping meet departmental targets and investing in tools that assist with energy management. - Formulate a series of tactical initiatives that would optimize energy usage on the shop floor. These would include charging forklifts and running cold rooms only during off-peak periods, running the dust extractors only during working hours and basing lights and air-conditioning on someone’s presence. - Increase visibility into the factory and other processes. - Enable limited, non-intrusive control functions for certain processes.
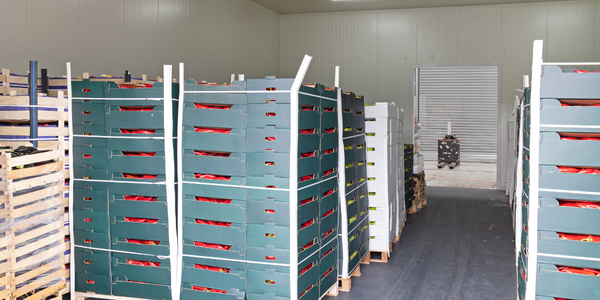
Case Study
Temperature Monitoring for Restaurant Food Storage
When it came to implementing a solution, Mr. Nesbitt had an idea of what functionality that he wanted. Although not mandated by Health Canada, Mr. Nesbitt wanted to ensure quality control issues met the highest possible standards as part of his commitment to top-of-class food services. This wish list included an easy-to use temperature-monitoring system that could provide a visible display of the temperatures of all of his refrigerators and freezers, including historical information so that he could review the performance of his equipment. It also had to provide alert notification (but email alerts and SMS text message alerts) to alert key staff in the event that a cooling system was exceeding pre-set warning limits.
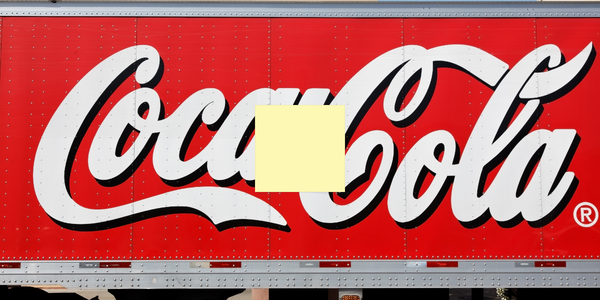
Case Study
Coca-Cola Refreshments, U.S.
Coca-Cola Refreshments owns and manages Coca-Cola branded refrigerators in retail establishments. Legacy systems were used to locate equipment information by logging onto multiple servers which took up to 8 hours to update information on 30-40 units. The company had no overall visibility into equipment status or maintenance history.