公司规模
Mid-size Company
地区
- America
国家
- United States
产品
- Spireon GoldStar GPS
技术栈
- GPS tracking
实施规模
- Enterprise-wide Deployment
影响指标
- Cost Savings
- Productivity Improvements
技术
- 传感器 - 全球定位系统
适用行业
- 汽车
适用功能
- 销售与市场营销
- 商业运营
用例
- 车载远程信息处理
- 资产健康管理 (AHM)
服务
- 系统集成
关于客户
Cactus Jack’s Auto is Arizona’s largest Buy Here Pay Here dealership with 9 state-wide locations. For over 18 years, they have specialized in helping drivers with bad credit get financed for a used car or truck. They have been a Spireon GoldStar GPS customer since 2011. The company has a significant number of active accounts and was facing challenges with vehicle repossession and write-offs.
挑战
Before implementing the GoldStar GPS system, Cactus Jack’s Auto was facing significant challenges with their repo department. They had 1,800 active accounts and were actively searching for 150 vehicles. After a six-month search, these vehicles were written off as total losses. This represented a significant loss for the company, amounting to 8% of all accounts. The company was in dire need of a solution that could help them reduce the number of vehicles being pursued, lower recovery costs and time, retain more working capital, decrease the number of write-offs, and recoup vehicles stolen from their lots.
解决方案
Cactus Jack’s Auto implemented Spireon GoldStar GPS devices in all their vehicles. The GPS system allowed the company to track their vehicles, reducing the number of vehicles being pursued and lowering recovery costs and time. The system also helped the company retain more working capital by decreasing the number of write-offs. Additionally, the GPS system enabled the company to recoup vehicles that were stolen from their lots. The implementation of the GPS system was a strategic move that aimed to improve the company's operations and reduce losses.
运营影响
数量效益
Case Study missing?
Start adding your own!
Register with your work email and create a new case study profile for your business.
相关案例.
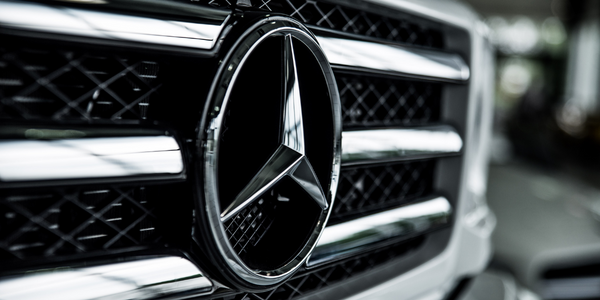
Case Study
Integral Plant Maintenance
Mercedes-Benz and his partner GAZ chose Siemens to be its maintenance partner at a new engine plant in Yaroslavl, Russia. The new plant offers a capacity to manufacture diesel engines for the Russian market, for locally produced Sprinter Classic. In addition to engines for the local market, the Yaroslavl plant will also produce spare parts. Mercedes-Benz Russia and his partner needed a service partner in order to ensure the operation of these lines in a maintenance partnership arrangement. The challenges included coordinating the entire maintenance management operation, in particular inspections, corrective and predictive maintenance activities, and the optimizing spare parts management. Siemens developed a customized maintenance solution that includes all electronic and mechanical maintenance activities (Integral Plant Maintenance).
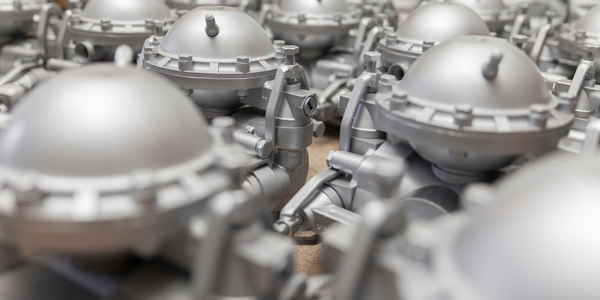
Case Study
Monitoring of Pressure Pumps in Automotive Industry
A large German/American producer of auto parts uses high-pressure pumps to deburr machined parts as a part of its production and quality check process. They decided to monitor these pumps to make sure they work properly and that they can see any indications leading to a potential failure before it affects their process.