公司规模
Mid-size Company
地区
- Europe
国家
- Germany
产品
- FORCAM FORCE
技术栈
- In-Memory Technology
- Data Collection Unit (DCU)
实施规模
- Enterprise-wide Deployment
影响指标
- Customer Satisfaction
- Productivity Improvements
技术
- 功能应用 - 制造执行系统 (MES)
- 分析与建模 - 大数据分析
- 应用基础设施与中间件 - 数据交换与集成
适用行业
- 汽车
- 航天
- 石油和天然气
适用功能
- 流程制造
- 产品研发
- 质量保证
用例
- 机器状态监测
- 预测性维护
- 过程控制与优化
- 监管合规监控
- 供应链可见性(SCV)
服务
- 软件设计与工程服务
- 系统集成
- 培训
关于客户
The customer is a medium-sized automotive supplier facing challenges in integrating a suitable traceability solution for their shop floor. They had previously attempted to implement a Manufacturing Execution System (MES) but faced numerous issues, including poor usability and failure to connect key machines. The company required a flexible and expandable system to ensure full traceability, regulatory compliance, and seamless integration with various machines. FORCAM's positive reputation and advanced technology made them the ideal choice to address these challenges and meet the customer's requirements.
挑战
Full traceability of all processes and products is critical to success in any business. A modern traceability solution is necessary to ensure reliable error analysis, rapid shutdown of vulnerabilities, and higher quality. The solution must consider all supply and value chains and support the connection of machinery and equipment seamlessly. A medium-sized automotive supplier struggled to integrate a suitable traceability solution for their shop floor. After a year of changes, configurations, and patches, the MES still did not work properly, and employees complained about poor usability. The management then consulted FORCAM.
解决方案
FORCAM provided their FORCAM FORCE technology, a first-of-its-kind solution for Manufacturing Intelligence. This technology ensures a flexible flow of parts from production orders throughout the production process. It abstracts quality-related data from specific control signals of the machine and compiles all quality-related parameters within a traceability metamodel. The solution supports flexible supply and value chains and allows for the exchange or replacement of equipment via plug and work, ensuring continuous traceability. The Data Collection Unit (DCU) decouples control units of individual systems and machines, enabling flexible routing and hot deployment. The process parameters provided by the DCU can be used directly in the traceability metamodel or further aggregated for more meaningful values. The solution also supports capturing incoming components using Data Matrix codes, barcodes, or tags, which are then assigned to the ERP system for a full process diagram.
运营影响
数量效益
Case Study missing?
Start adding your own!
Register with your work email and create a new case study profile for your business.
相关案例.
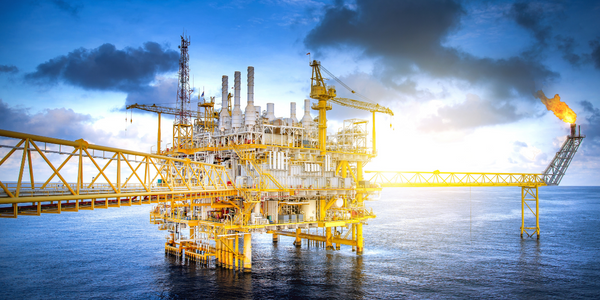
Case Study
Taking Oil and Gas Exploration to the Next Level
DownUnder GeoSolutions (DUG) wanted to increase computing performance by 5 to 10 times to improve seismic processing. The solution must build on current architecture software investments without sacrificing existing software and scale computing without scaling IT infrastructure costs.
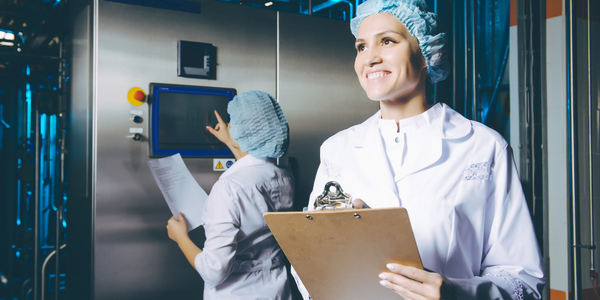
Case Study
Remote Wellhead Monitoring
Each wellhead was equipped with various sensors and meters that needed to be monitored and controlled from a central HMI, often miles away from the assets in the field. Redundant solar and wind generators were installed at each wellhead to support the electrical needs of the pumpstations, temperature meters, cameras, and cellular modules. In addition to asset management and remote control capabilities, data logging for remote surveillance and alarm notifications was a key demand from the customer. Terra Ferma’s solution needed to be power efficient, reliable, and capable of supporting high-bandwidth data-feeds. They needed a multi-link cellular connection to a central server that sustained reliable and redundant monitoring and control of flow meters, temperature sensors, power supply, and event-logging; including video and image files. This open-standard network needed to interface with the existing SCADA and proprietary network management software.
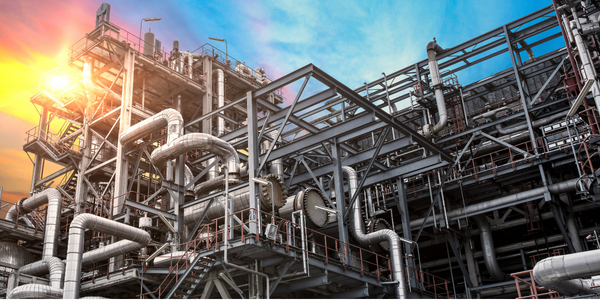
Case Study
Refinery Saves Over $700,000 with Smart Wireless
One of the largest petroleum refineries in the world is equipped to refine various types of crude oil and manufacture various grades of fuel from motor gasoline to Aviation Turbine Fuel. Due to wear and tear, eight hydrogen valves in each refinery were leaking, and each cost $1800 per ton of hydrogen vented. The plant also had leakage on nearly 30 flare control hydrocarbon valves. The refinery wanted a continuous, online monitoring system that could catch leaks early, minimize hydrogen and hydrocarbon production losses, and improve safety for maintenance.
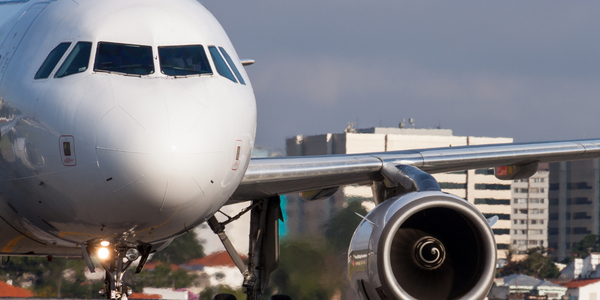
Case Study
Airbus Soars with Wearable Technology
Building an Airbus aircraft involves complex manufacturing processes consisting of thousands of moving parts. Speed and accuracy are critical to business and competitive advantage. Improvements in both would have high impact on Airbus’ bottom line. Airbus wanted to help operators reduce the complexity of assembling cabin seats and decrease the time required to complete this task.
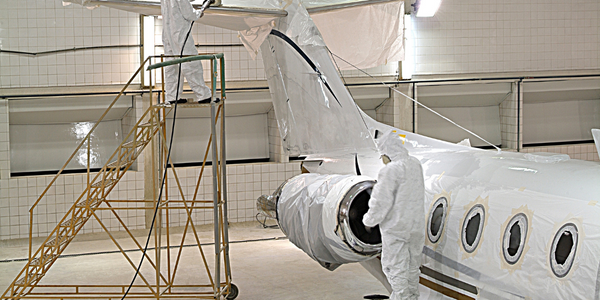
Case Study
Aircraft Predictive Maintenance and Workflow Optimization
First, aircraft manufacturer have trouble monitoring the health of aircraft systems with health prognostics and deliver predictive maintenance insights. Second, aircraft manufacturer wants a solution that can provide an in-context advisory and align job assignments to match technician experience and expertise.