公司规模
Large Corporate
地区
- Europe
- America
- Asia
国家
- Germany
- Brazil
- China
- France
- United States
产品
- HYDRA
- SAP
- Mettler Toledo Weighing Systems
技术栈
- Oracle Databases
- IPCs and PCs with Touch Screen
实施规模
- Enterprise-wide Deployment
影响指标
- Productivity Improvements
- Digital Expertise
技术
- 功能应用 - 企业资源规划系统 (ERP)
- 功能应用 - 远程监控系统
适用行业
- 汽车
适用功能
- 流程制造
- 质量保证
用例
- 机器状态监测
- 预测性维护
- 远程资产管理
服务
- 系统集成
- 软件设计与工程服务
关于客户
DIEHL Stiftung & Co. KG is a large, family-owned German enterprise with a history spanning over 100 years. The company employs approximately 16,200 staff worldwide and operates internationally. The DIEHL Metall subgroup is a leading supplier in the automotive, heating, sanitary, and electronic industries, with manufacturing locations in Germany and subsidiaries in Brazil, the USA, France, and China. DIEHL Metall is renowned for its semi-finished and forged components made of brass and innovative special brass alloys, which are used in various everyday applications. The Forging Technology division is a global expert in producing drop-forged parts from brass alloys, including synchronizer rings for gearboxes. DIEHL products are also prevalent in households as sanitary and gas fittings. The company generates a turnover of 829 million Euros with 3,339 employees.
挑战
DIEHL Metall faced the challenge of replacing an outdated Time & Attendance system with a new, flexible, and fail-proof system that could integrate with SAP in the future. The new system needed to comply with company agreements on flexible working hours and provide a certified interface to SAP. Additionally, the Shop Floor Data module required online information for the entire production level, simplifying work procedures, supporting paperless production, and facilitating machine data collection.
解决方案
The solution involved implementing the HYDRA system, starting with a detailed requirements specification. The project began in April 1997 with a test run of the Time & Attendance module, followed by a pilot phase for Shop Floor and Machine Data Collection. Within three months, HYDRA was operational at over 60 workstations. The system was later upgraded to include weighing systems by Mettler Toledo, modules for Shop Floor Scheduling, Personnel Scheduling, and Incentive Pay. The Material & Production Logistics module was also added. HYDRA reduced manual input efforts in administration and ensured transparency by showing current order, personnel, and machine statuses. The system's direct connection to weighing systems and machines allowed for precise piece numbers and quantities to be uploaded to SAP PP.
运营影响
数量效益
Case Study missing?
Start adding your own!
Register with your work email and create a new case study profile for your business.
相关案例.
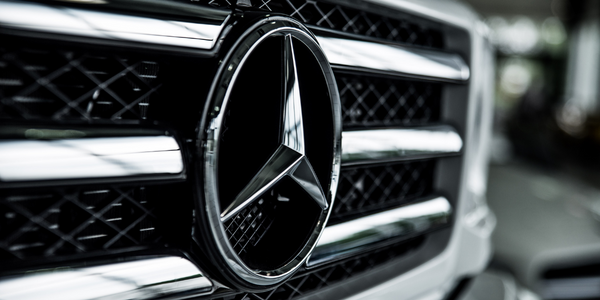
Case Study
Integral Plant Maintenance
Mercedes-Benz and his partner GAZ chose Siemens to be its maintenance partner at a new engine plant in Yaroslavl, Russia. The new plant offers a capacity to manufacture diesel engines for the Russian market, for locally produced Sprinter Classic. In addition to engines for the local market, the Yaroslavl plant will also produce spare parts. Mercedes-Benz Russia and his partner needed a service partner in order to ensure the operation of these lines in a maintenance partnership arrangement. The challenges included coordinating the entire maintenance management operation, in particular inspections, corrective and predictive maintenance activities, and the optimizing spare parts management. Siemens developed a customized maintenance solution that includes all electronic and mechanical maintenance activities (Integral Plant Maintenance).
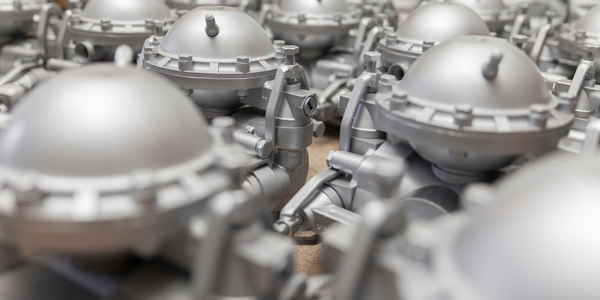
Case Study
Monitoring of Pressure Pumps in Automotive Industry
A large German/American producer of auto parts uses high-pressure pumps to deburr machined parts as a part of its production and quality check process. They decided to monitor these pumps to make sure they work properly and that they can see any indications leading to a potential failure before it affects their process.