公司规模
Large Corporate
地区
- Europe
- America
国家
- United Kingdom
- United States
- Puerto Rico
产品
- Sphera PHA Pro®
技术栈
- Desktop Software
实施规模
- Enterprise-wide Deployment
影响指标
- Productivity Improvements
- Customer Satisfaction
技术
- 功能应用 - 远程监控系统
适用行业
- 海洋与航运
- 石油和天然气
适用功能
- 质量保证
- 商业运营
用例
- 过程控制与优化
- 预测性维护
服务
- 系统集成
- 软件设计与工程服务
关于客户
Founded in 1760, Lloyd's Register can trace its roots back to Lloyd's Coffee House, a social hub in London’s maritime district that was frequented by merchants, underwriters, and brokers associated with shipping. Today, Lloyd’s Register works to enhance the safety of life, property and the environment, at sea, on land and in the air, helping its clients to ensure safe, responsible and sustainable supply chains. The company is recognized as a world leader in assessing the alignment of business processes and products with internationally recognized safety standards, serving clients that range from vast multinational corporations to small local businesses. Lloyd’s Register provides its clients with the highest possible business value by continuously improving its own work processes and tools.
挑战
Lloyd’s Register, a world leader in assessing business processes and products for safety standards, sought to improve its client risk assessment meetings. The company wanted to interact more effectively with clients during these meetings and expedite follow-up actions. Previously, meeting notes had to be captured by the engineers and support specialists in the meeting. Data about the client’s specific risks, safeguards, recommendations, and actions would be entered into various word documents and spreadsheets. Afterward, all of that information would have to be manually combined into a single draft document and circulated to the team that had attended the meeting. Each attendee would have to spend additional time checking to see that information from their discussion had been captured correctly and included in this encompassing document. Consolidation of information could take days and people could not see each other’s comments until they were issued in a draft revision. Important points made during the meeting might even get lost in the process.
解决方案
In early 2012, Lloyd’s Register implemented Sphera PHA Pro®, flexible desktop software that helps individual users conduct Process Hazard Analyses (PHAs) – including hazard and operability (HAZOP) and “what-if” analyses. With preformatted industry-standard PHA templates and libraries, PHA-Pro enables Lloyd’s Register experts to focus on identifying, assessing and resolving the client’s potential safety management issues. The system has proved cost effective and worked efficiently. Worksheets were projected so everyone could see them as they captured comments. Everything was recorded in real time and could be corrected and edited at that moment. People could agree right then and there, on the spot, with what was captured and documented. They were able to dramatically shorten – and, in some cases, eliminate - the draft revision stage in their projects.
运营影响
数量效益
Case Study missing?
Start adding your own!
Register with your work email and create a new case study profile for your business.
相关案例.
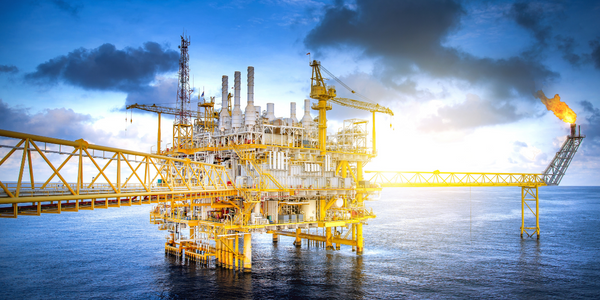
Case Study
Taking Oil and Gas Exploration to the Next Level
DownUnder GeoSolutions (DUG) wanted to increase computing performance by 5 to 10 times to improve seismic processing. The solution must build on current architecture software investments without sacrificing existing software and scale computing without scaling IT infrastructure costs.
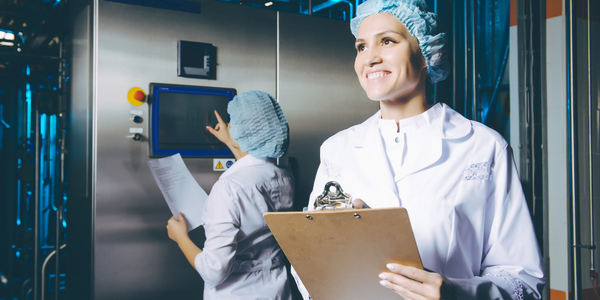
Case Study
Remote Wellhead Monitoring
Each wellhead was equipped with various sensors and meters that needed to be monitored and controlled from a central HMI, often miles away from the assets in the field. Redundant solar and wind generators were installed at each wellhead to support the electrical needs of the pumpstations, temperature meters, cameras, and cellular modules. In addition to asset management and remote control capabilities, data logging for remote surveillance and alarm notifications was a key demand from the customer. Terra Ferma’s solution needed to be power efficient, reliable, and capable of supporting high-bandwidth data-feeds. They needed a multi-link cellular connection to a central server that sustained reliable and redundant monitoring and control of flow meters, temperature sensors, power supply, and event-logging; including video and image files. This open-standard network needed to interface with the existing SCADA and proprietary network management software.
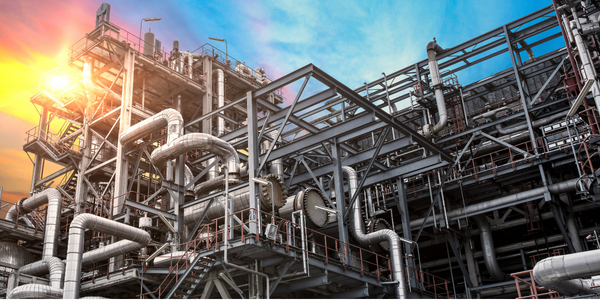
Case Study
Refinery Saves Over $700,000 with Smart Wireless
One of the largest petroleum refineries in the world is equipped to refine various types of crude oil and manufacture various grades of fuel from motor gasoline to Aviation Turbine Fuel. Due to wear and tear, eight hydrogen valves in each refinery were leaking, and each cost $1800 per ton of hydrogen vented. The plant also had leakage on nearly 30 flare control hydrocarbon valves. The refinery wanted a continuous, online monitoring system that could catch leaks early, minimize hydrogen and hydrocarbon production losses, and improve safety for maintenance.