公司规模
Mid-size Company
地区
- America
国家
- United States
产品
- Plex Manufacturing Cloud
技术栈
- Cloud Computing
- ERP Systems
实施规模
- Enterprise-wide Deployment
影响指标
- Productivity Improvements
- Cost Savings
- Employee Satisfaction
技术
- 功能应用 - 企业资源规划系统 (ERP)
- 平台即服务 (PaaS) - 连接平台
适用行业
- 汽车
适用功能
- 商业运营
- 质量保证
用例
- 库存管理
- 过程控制与优化
服务
- 系统集成
- 培训
关于客户
FT Precision Inc. is a Japanese-parented company based in Fredericktown, Ohio, specializing in the supply of automotive chassis and engine components. The company is a subsidiary of Tanaka Seimitsu Kogyo Co., and its operations include machining raw steel forgings and cast aluminum combustion engine rocker arms, as well as forgings of constant velocity joint bearings and outboard retainer forgings. With a workforce of 400 employees, FT Precision has established itself as a key player in the automotive industry, known for its commitment to quality and excellence. Over the years, the company has evolved from a small operation to a mid-sized enterprise, driven by a strategy focused on long-term survival and commercial success. Despite its achievements, FT Precision recognized the need to modernize its processes to keep pace with the demands of a real-time, lean production environment.
挑战
FT Precision faced significant challenges with their paper-based processes, which were unable to keep up with the demands of a real-time, lean production environment. The manual data entry and inventory tracking systems were outdated and resource-draining, leading to inefficiencies and slow response times. The company needed a platform that could provide immediate access to accurate operational data across all departments to maintain their competitive edge and support their growth strategy. The senior management recognized that transitioning to software-driven, integrated processes was essential to realize their lean manufacturing and growth potential.
解决方案
FT Precision decided to implement the Plex Manufacturing Cloud to address their operational challenges. Initially, they planned to deploy only the inventory management module, but after realizing the software's full capabilities, they partnered with Plante Moran to explore its potential further. Plante Moran provided industry expertise, bilingual support, and knowledge of JSOX compliance, facilitating a smooth transition to the new system. The implementation was divided into phases, with phase zero focusing on identifying areas for improvement and phase one on the actual deployment. The project was completed on time and under budget, with no disruptions to operations. The transition involved significant changes for the workforce, who were initially resistant to moving from paper-based processes to a technology-driven environment. To ease the transition, FT Precision provided training sessions and ran parallel processes to test the new system. The Plex Community also played a crucial role in supporting the company by offering a platform for collaboration and advice.
运营影响
数量效益
Case Study missing?
Start adding your own!
Register with your work email and create a new case study profile for your business.
相关案例.
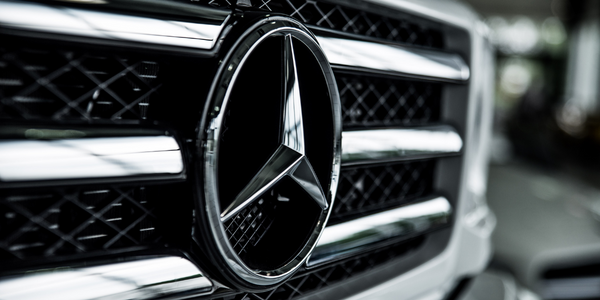
Case Study
Integral Plant Maintenance
Mercedes-Benz and his partner GAZ chose Siemens to be its maintenance partner at a new engine plant in Yaroslavl, Russia. The new plant offers a capacity to manufacture diesel engines for the Russian market, for locally produced Sprinter Classic. In addition to engines for the local market, the Yaroslavl plant will also produce spare parts. Mercedes-Benz Russia and his partner needed a service partner in order to ensure the operation of these lines in a maintenance partnership arrangement. The challenges included coordinating the entire maintenance management operation, in particular inspections, corrective and predictive maintenance activities, and the optimizing spare parts management. Siemens developed a customized maintenance solution that includes all electronic and mechanical maintenance activities (Integral Plant Maintenance).
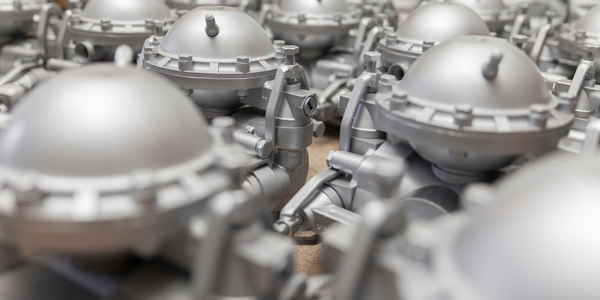
Case Study
Monitoring of Pressure Pumps in Automotive Industry
A large German/American producer of auto parts uses high-pressure pumps to deburr machined parts as a part of its production and quality check process. They decided to monitor these pumps to make sure they work properly and that they can see any indications leading to a potential failure before it affects their process.