技术
- 功能应用 - 企业资产管理系统 (EAM)
适用行业
- 包装
适用功能
- 产品研发
- 质量保证
用例
- 资产生命周期管理
- 施工管理
服务
- 系统集成
- 测试与认证
关于客户
Carey Color Inc. 是一家提供全方位服务、技术驱动的通信公司,总部位于美国俄亥俄州沙龙中心。该公司专注于包装、激光雕刻、印前、数码摄影、资产管理和大幅面制版。他们自 1994 年以来一直在使用 DALiM LiTHO。该公司的业务包括印前处理、摄影、DAM、包装和制版。他们选择 DALIM SOFTWARE 产品是因为其高质量的修饰、打样、色彩校正、强大的 PDF 生成以及审核和批准工作流程。
挑战
Carey Color Inc. 是一家提供全方位服务、技术驱动的通信公司,面临着利用现有技术和新技术为客户提供最佳结果的挑战。该公司需要管理从小到大的复杂工作流程,并与 Adobe InDesign 等其他软件集成。 Carey 的一些较大客户使用 DALIM ES 进行摄影工作流程,导入文件以进行质量控制并标记以进行校正和色彩准确性。该公司需要一个不仅仅提供数字资产管理 (DAM) 的系统,因为包括电子商务、法律、艺术家、营销、买家和其他人员在内的各种利益相关者都参与了该过程。该系统还需要容纳大量用户,在任何给定时间系统上有多达 40-50 个用户。
解决方案
Carey Color Inc. 采用 DALIM 软件来满足其复杂的需求。 DALIM ES 为该公司提供了项目管理、制作工作流程、软打样和 DAM。它还通过 Silicon Publishing 提供与 Adobe InDesign 的连接,所有这些都在基于 Web 的环境中进行,从而消除了客户加载 ES 的需要。 DALIM SOFTWARE 的多功能性就像一把瑞士军刀,能够处理多种任务。该公司赞赏 DALIM SOFTWARE 对双方关系的承诺及其适应不断变化的市场现实的能力。 25 年来,DALIM SOFTWARE 与 Carey Color Inc. 一起发展,不断适应新的市场现实。
运营影响
Case Study missing?
Start adding your own!
Register with your work email and create a new case study profile for your business.
相关案例.
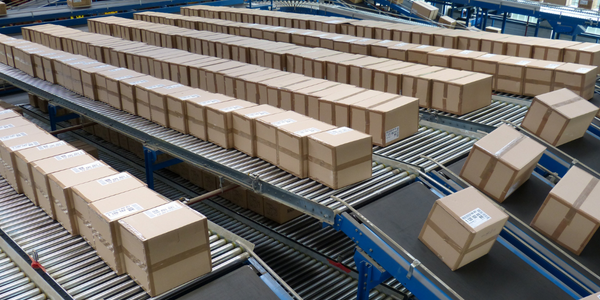
Case Study
IoT Data Analytics Case Study - Packaging Films Manufacturer
The company manufactures packaging films on made to order or configure to order basis. Every order has a different set of requirements from the product characteristics perspective and hence requires machine’s settings to be adjusted accordingly. If the film quality does not meet the required standards, the degraded quality impacts customer delivery causes customer dissatisfaction and results in lower margins. The biggest challenge was to identify the real root cause and devise a remedy for that.
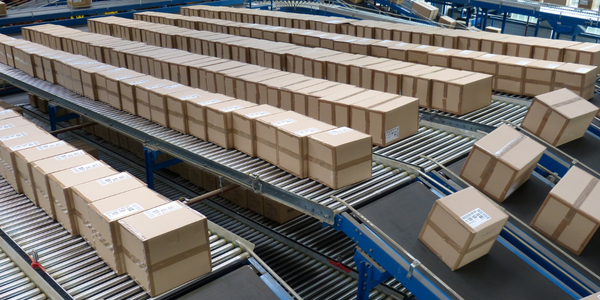
Case Study
Zenon the Ideal Basis for An Ergonomic HMI
KHS develops and produces machines and equipment for filling and packaging in the drinks industry. Because drinks manufacturing, filling and packaging consist of a number of highly complex processes, the user-friendly and intuitive operation of equipment is increasingly gaining in significance. In order to design these processes as simple as possible for the user, KHS decided to introduce a uniform, transparent and standardized solution to the company. The HMI interface should meet the requirement for people with different qualifications and enable them to work on a standard platform.
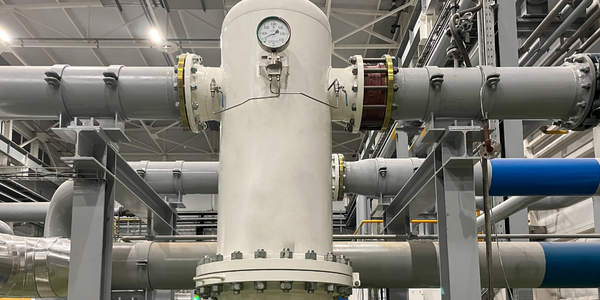
Case Study
Sparks Dynamics Assists Atlas Container Secure a $15,000 BGE Energy Rebate
The ReMASTER Compressed Air Monitoring system was installed in 2015. This system is capable of monitoring compressed air system parameters on a continuous basis and transferring that information to a cloud server which can be accessed by Atlas Container personnel, Industrial Diagnostics and Sparks Dynamics. This information was collected into a database which can be exported to an Excel spreadsheet or displayed graphically using Sparks Dynamics ViewMaster Software. The average annual compressed air electricity expense was estimated to be approximately $116,000. This is based on an incremental $/KWh electric rate of $.091 per KWh and an estimated compressed air energy consumption of 1,279,200 KWH. The implementation phase of Energy Conservation Measures (ECMs) for the Compressed Air System included: • Identification and repair of compressed air leaks • Understanding of compressed air usage per manufacturing machine and installation of shut off valves when the machines are no longer in production mode • Identification of misapplications of compressed air to include blow offs, venturis, and cooling scenarios • Understand system pressure requirements and potential installation of point of use pressure regulation.
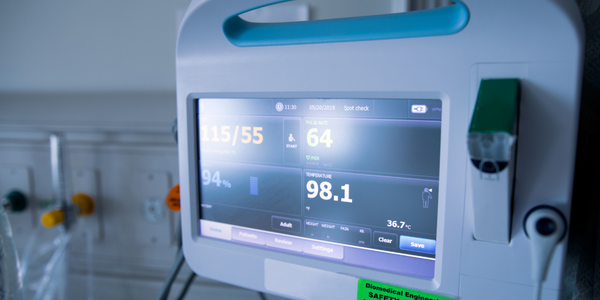
Case Study
Mondi Implements Statistics-Based Health Monitoring and Predictive Maintenance
The extrusion and other machines at Mondi’s plant are large and complex, measuring up to 50 meters long and 15 meters high. Each machine is controlled by up to five programmable logic controllers (PLCs), which log temperature, pressure, velocity, and other performance parameters from the machine’s sensors. Each machine records 300–400 parameter values every minute, generating 7 gigabytes of data daily.Mondi faced several challenges in using this data for predictive maintenance. First, the plant personnel had limited experience with statistical analysis and machine learning. They needed to evaluate a variety of machine learning approaches to identify which produced the most accurate results for their data. They also needed to develop an application that presented the results clearly and immediately to machine operators. Lastly, they needed to package this application for continuous use in a production environment.
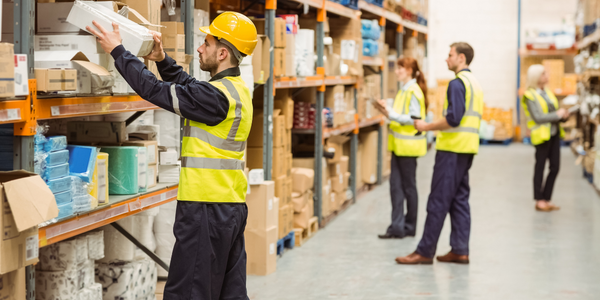
Case Study
Automated Pallet Labeling Solution for SPR Packaging
SPR Packaging, an American supplier of packaging solutions, was in search of an automated pallet labeling solution that could meet their immediate and future needs. They aimed to equip their lines with automatic printer applicators, but also required a solution that could interface with their accounting software. The challenge was to find a system that could read a 2D code on pallets at the stretch wrapper, track the pallet, and flag any pallets with unread barcodes for inspection. The pallets could be single or double stacked, and the system needed to be able to differentiate between the two. SPR Packaging sought a system integrator with extensive experience in advanced printing and tracking solutions to provide a complete traceability system.
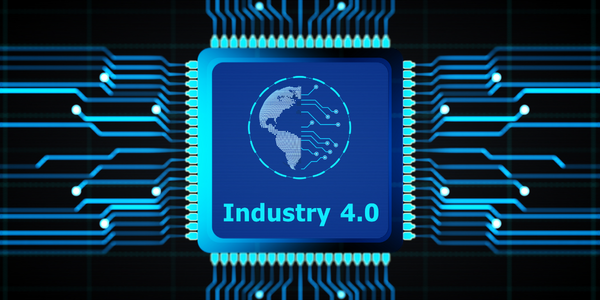
Case Study
Industry 4.0 at ALPLA: Enhancing Factory Efficiency with IoT
ALPLA, a global leader in packaging solutions, faced several challenges as the complexity of their production machinery increased. The need for highly trained specialists in each factory led to higher personnel costs, difficulties in recruiting experienced talent at each location, and costly personnel turnover. Furthermore, less experienced operators running the machines sub-optimally impacted resource consumption and overall equipment effectiveness (OEE). ALPLA also faced the challenge of monitoring visual inspection systems in every line of their plants, which was almost impossible to do manually. In 2016, ALPLA decided to use data from the 900 different types of embedded sensors in each factory to address these issues. However, their initial choice of SQL Server as the data store for the sensor data proved inadequate, as it was unable to cope with their data requirements.