公司规模
Large Corporate
地区
- America
国家
- United States
- Canada
产品
- OnStar Interactive Virtual Assistant (IVA)
- Google Cloud Dialogflow
- Google Assistant
技术栈
- Conversational AI
- Intent Recognition Algorithms
实施规模
- Enterprise-wide Deployment
影响指标
- Customer Satisfaction
- Digital Expertise
技术
- 分析与建模 - Generative AI
- 应用基础设施与中间件 - API 集成与管理
适用行业
- 汽车
用例
- 预测性维护
- 远程资产管理
服务
- 云规划/设计/实施服务
- 系统集成
关于客户
General Motors (GM) is a global automotive company committed to advancing an all-electric future. With a focus on inclusivity and accessibility, GM operates under several well-known brands, including Chevrolet, Buick, GMC, Cadillac, Baojun, and Wuling. The company is at the forefront of automotive innovation, particularly with its Ultium battery platform, which powers a range of vehicles from mass-market to high-performance models. GM's commitment to safety and connected vehicle technology is exemplified by its OnStar service, a leader in providing safety services and advanced connectivity solutions. GM's collaboration with Google Cloud reflects its dedication to leveraging cutting-edge technology to enhance customer experiences and drive digital transformation across its operations.
挑战
General Motors (GM) sought to enhance its customer service capabilities by integrating advanced AI technologies into its OnStar service. The challenge was to provide a seamless, efficient, and responsive customer experience that could handle a high volume of inquiries while distinguishing between routine and emergency situations. GM aimed to leverage AI to improve the accuracy and speed of responses, reduce hold times, and allow human advisors to focus on more complex customer needs. Additionally, GM wanted to explore the potential of generative AI applications across its business operations, building on its existing collaboration with Google Cloud.
解决方案
To address its challenges, GM partnered with Google Cloud to integrate conversational AI technology into its OnStar service. The OnStar Interactive Virtual Assistant (IVA) was launched, utilizing Google Cloud's Dialogflow technology to power advanced intent recognition algorithms. This integration enabled the OnStar IVA to handle over 1 million customer inquiries monthly, providing routing and navigation assistance with a natural-sounding voice. The system was designed to quickly understand and respond to customer requests, distinguishing between routine inquiries and potential emergency situations. This allowed OnStar Advisors to dedicate more time to complex customer interactions requiring human intervention. Additionally, GM deployed chatbots using Dialogflow technology to assist customers with questions about GM vehicles and product features. These chatbots, active on GM's corporate and vehicle brand websites, provided quick answers to inquiries, enhancing customer convenience and engagement. The successful deployment of these AI technologies has paved the way for future generative AI applications, with GM and Google Cloud exploring new business-wide opportunities.
运营影响
数量效益
Case Study missing?
Start adding your own!
Register with your work email and create a new case study profile for your business.
相关案例.
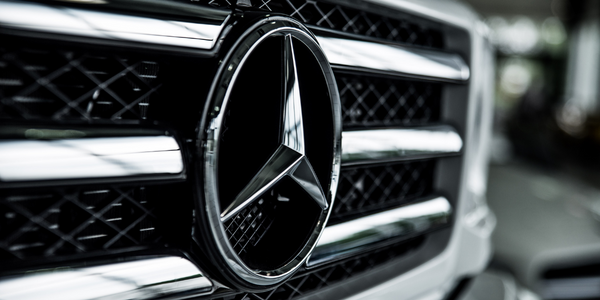
Case Study
Integral Plant Maintenance
Mercedes-Benz and his partner GAZ chose Siemens to be its maintenance partner at a new engine plant in Yaroslavl, Russia. The new plant offers a capacity to manufacture diesel engines for the Russian market, for locally produced Sprinter Classic. In addition to engines for the local market, the Yaroslavl plant will also produce spare parts. Mercedes-Benz Russia and his partner needed a service partner in order to ensure the operation of these lines in a maintenance partnership arrangement. The challenges included coordinating the entire maintenance management operation, in particular inspections, corrective and predictive maintenance activities, and the optimizing spare parts management. Siemens developed a customized maintenance solution that includes all electronic and mechanical maintenance activities (Integral Plant Maintenance).
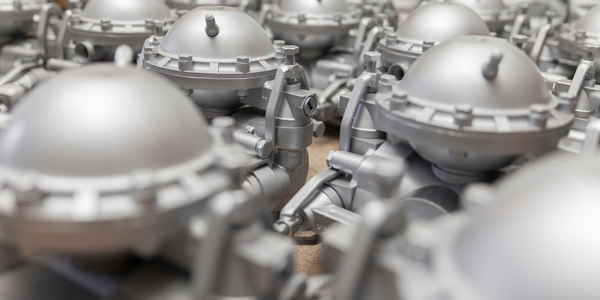
Case Study
Monitoring of Pressure Pumps in Automotive Industry
A large German/American producer of auto parts uses high-pressure pumps to deburr machined parts as a part of its production and quality check process. They decided to monitor these pumps to make sure they work properly and that they can see any indications leading to a potential failure before it affects their process.