公司规模
Mid-size Company
地区
- America
国家
- United States
产品
- Plex Cloud ERP
技术栈
- Cloud ERP
实施规模
- Enterprise-wide Deployment
影响指标
- Cost Savings
- Employee Satisfaction
- Productivity Improvements
技术
- 功能应用 - 企业资源规划系统 (ERP)
适用行业
- 汽车
适用功能
- 商业运营
用例
- 过程控制与优化
- 连续排放监测系统
服务
- 软件设计与工程服务
关于客户
GR Spring & Stamping (GRSS) is a prominent supplier in the automotive industry, recognized for its expertise in manufacturing metal stampings, value-added assemblies, springs, and slide-formed products. Established in 1960 as Grand Rapids Spring & Wire, the company has grown to become an industry leader, known for its commitment to quality and innovation. GRSS operates with a strong focus on continuous improvement, believing that this approach is essential for thriving in a competitive marketplace. The company has institutionalized a culture of innovation, encouraging every employee to contribute ideas for improvement. This culture is supported by the World Class Idea (WCI) program, which has led to significant improvements in manufacturing processes, resulting in cost savings and enhanced operational efficiency. GRSS is dedicated to leveraging technology to work as efficiently as possible, while also fostering a collaborative environment where employees are motivated to think creatively and contribute to the company's success. The company's commitment to continuous improvement and employee engagement has positioned it as a leader in the automotive industry, capable of navigating market challenges and achieving sustainable growth.
挑战
GR Spring & Stamping (GRSS) operates in a highly competitive market, particularly within the automotive industry. The company has faced significant challenges due to foreign competition, economic downturns, and increasing supplier requirements from automotive OEMs. These pressures have led many competitors to succumb, but GRSS has managed to thrive by institutionalizing a mindset of continuous improvement. The company recognizes that to survive and succeed, it must constantly innovate and improve its processes. This mindset is deeply embedded in the company's culture, with every employee expected to contribute ideas for improvement. The challenge for GRSS is to maintain this culture of continuous improvement and ensure that it translates into tangible benefits for the company. The company has developed a program called the World Class Idea (WCI) program, which encourages employees to submit suggestions for improvements. The challenge is to effectively manage this program, ensure that valuable ideas are implemented, and that the program contributes to the company's overall success.
解决方案
GR Spring & Stamping (GRSS) has implemented a comprehensive solution to address the challenges of maintaining a culture of continuous improvement. The company has developed the World Class Idea (WCI) program, which encourages employees to submit suggestions for improvements across various categories, including quality, cost, delivery, safety, and morale. The program is integrated with the Plex Cloud ERP system, allowing employees to easily submit their ideas through a dialogue box. This system streamlines the process of capturing and reviewing suggestions, ensuring that valuable ideas are not overlooked. Supervisors review the suggestions weekly to determine their feasibility and prevent duplication. Employees are incentivized to participate in the program, receiving financial rewards for each approved suggestion. The WCI program fosters a culture of innovation by celebrating even small gains and encouraging employees to think about improvement possibilities from the moment they enter the workplace. GRSS emphasizes that success is achieved not by making one significant improvement but by making numerous small improvements. This approach has led to significant cost savings and operational efficiencies, with the company achieving annual savings of $1.2 million. The WCI program has also contributed to employee satisfaction, as employees feel valued and empowered to contribute to the company's success.
运营影响
数量效益
Case Study missing?
Start adding your own!
Register with your work email and create a new case study profile for your business.
相关案例.
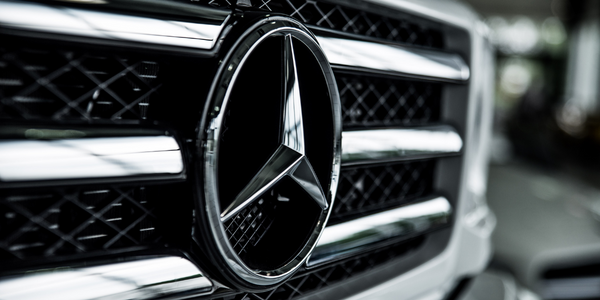
Case Study
Integral Plant Maintenance
Mercedes-Benz and his partner GAZ chose Siemens to be its maintenance partner at a new engine plant in Yaroslavl, Russia. The new plant offers a capacity to manufacture diesel engines for the Russian market, for locally produced Sprinter Classic. In addition to engines for the local market, the Yaroslavl plant will also produce spare parts. Mercedes-Benz Russia and his partner needed a service partner in order to ensure the operation of these lines in a maintenance partnership arrangement. The challenges included coordinating the entire maintenance management operation, in particular inspections, corrective and predictive maintenance activities, and the optimizing spare parts management. Siemens developed a customized maintenance solution that includes all electronic and mechanical maintenance activities (Integral Plant Maintenance).
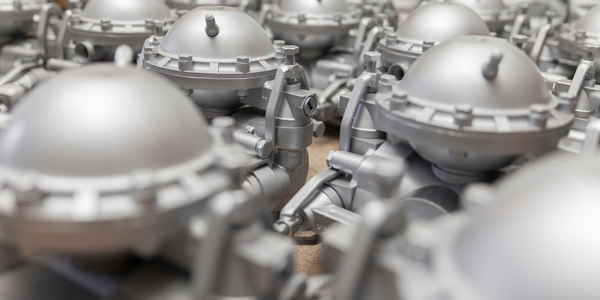
Case Study
Monitoring of Pressure Pumps in Automotive Industry
A large German/American producer of auto parts uses high-pressure pumps to deburr machined parts as a part of its production and quality check process. They decided to monitor these pumps to make sure they work properly and that they can see any indications leading to a potential failure before it affects their process.