Hausbeck Pickles and Peppers Transforms Operations with Cloud-Based ERP for Enhanced Inventory Management
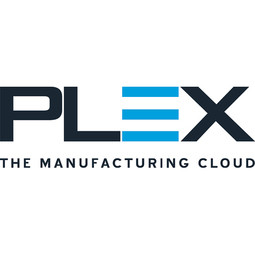
公司规模
Mid-size Company
地区
- America
国家
- United States
产品
- Plex Smart Manufacturing Platform
技术栈
- Cloud-based ERP
实施规模
- Enterprise-wide Deployment
影响指标
- Cost Savings
- Customer Satisfaction
- Productivity Improvements
技术
- 功能应用 - 企业资源规划系统 (ERP)
- 平台即服务 (PaaS) - 数据管理平台
适用行业
- 食品与饮料
适用功能
- 质量保证
- 仓库和库存管理
用例
- 库存管理
- 质量预测分析
- 过程控制与优化
服务
- 云规划/设计/实施服务
- 系统集成
关于客户
Hausbeck Pickles and Peppers is a prominent player in the food and beverage industry, specializing in the production of pickles and peppers. The company supplies its products to major fast-food chains such as Subway, Burger King, Sonic, Domino’s Pizza, Papa John’s, Pizza Hut, Taco Bell, and KFC. Located in Saginaw, Michigan, Hausbeck Pickles and Peppers operates a factory that produces an impressive volume of products daily. On average, the factory produces 400,000 pounds of pickles or peppers each day, amounting to approximately 10 billion pickle slices, 20 million pounds of banana peppers, and 13 million pounds of jalapeños annually. Despite its success, the company faced challenges in managing its business processes, particularly in inventory management and production tracking. With no dedicated IT department or expertise in ERP systems, Hausbeck sought a solution to streamline its operations and improve efficiency.
挑战
Hausbeck Pickles and Peppers faced significant challenges in managing their inventory and production processes. The company relied heavily on paper-based processes, which limited visibility into their largest asset, inventory. This lack of visibility made it difficult to manage inventory costs effectively throughout the production process. The situation was exacerbated by a failed mock audit, highlighting the need for better control over ingredient tracking and traceability. The CFO realized that the data from their accounting system was not aligning with actual inventory costs, leading to discrepancies and missing inventory. The company used QuickBooks for accounting and another system for inventory, but these systems lacked integration and costing capabilities. Additionally, tracking and tracing ingredients through production was cumbersome and time-consuming, relying on multiple spreadsheets and manual processes.
解决方案
To address the challenges faced by Hausbeck Pickles and Peppers, the company decided to implement a cloud-based ERP system. Recognizing the need for a consolidated solution, they hired Russ Edwards as the ERP Manager and Cost Accountant to lead the initiative. Edwards evaluated various ERP systems and determined that a cloud-based solution would be ideal, given the company's limited resources and budget constraints. After careful consideration, Hausbeck chose the Plex Smart Manufacturing Platform for its comprehensive traceability capabilities. The implementation process was smooth, with the team relying heavily on Plex's Customer Success and Support (CSS) experts. The implementation was completed in six months, and the company benefited from not having to transition from an existing ERP system. The new system allowed for real-time production tracking, eliminating the delays and manual processes previously involved. Employees, even those with limited technological skills, found the system easy to use, enhancing overall efficiency.
运营影响
数量效益
Case Study missing?
Start adding your own!
Register with your work email and create a new case study profile for your business.
相关案例.

Case Study
The Kellogg Company
Kellogg keeps a close eye on its trade spend, analyzing large volumes of data and running complex simulations to predict which promotional activities will be the most effective. Kellogg needed to decrease the trade spend but its traditional relational database on premises could not keep up with the pace of demand.
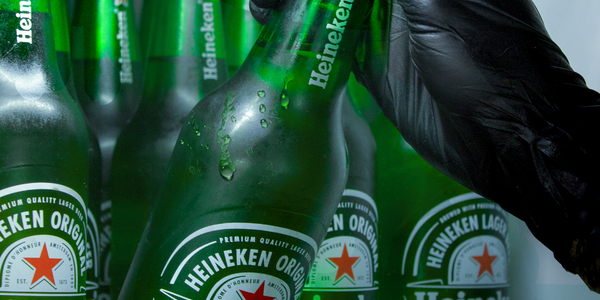
Case Study
HEINEKEN Uses the Cloud to Reach 10.5 Million Consumers
For 2012 campaign, the Bond promotion, it planned to launch the campaign at the same time everywhere on the planet. That created unprecedented challenges for HEINEKEN—nowhere more so than in its technology operation. The primary digital content for the campaign was a 100-megabyte movie that had to play flawlessly for millions of viewers worldwide. After all, Bond never fails. No one was going to tolerate a technology failure that might bruise his brand.Previously, HEINEKEN had supported digital media at its outsourced datacenter. But that datacenter lacked the computing resources HEINEKEN needed, and building them—especially to support peak traffic that would total millions of simultaneous hits—would have been both time-consuming and expensive. Nor would it have provided the geographic reach that HEINEKEN needed to minimize latency worldwide.
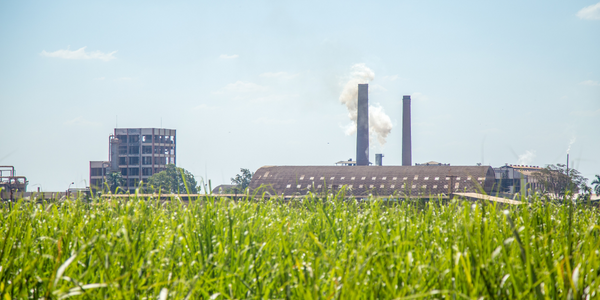
Case Study
Energy Management System at Sugar Industry
The company wanted to use the information from the system to claim under the renewable energy certificate scheme. The benefit to the company under the renewable energy certificates is Rs 75 million a year. To enable the above, an end-to-end solution for load monitoring, consumption monitoring, online data monitoring, automatic meter data acquisition which can be exported to SAP and other applications is required.
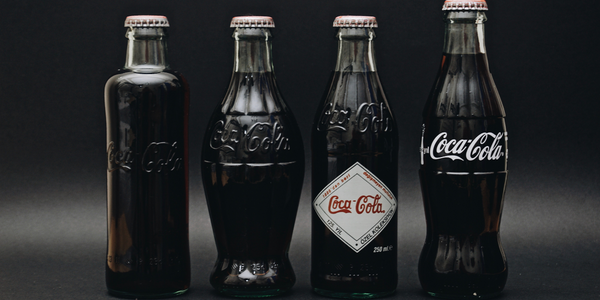
Case Study
Coca Cola Swaziland Conco Case Study
Coco Cola Swaziland, South Africa would like to find a solution that would enable the following results: - Reduce energy consumption by 20% in one year. - Formulate a series of strategic initiatives that would enlist the commitment of corporate management and create employee awareness while helping meet departmental targets and investing in tools that assist with energy management. - Formulate a series of tactical initiatives that would optimize energy usage on the shop floor. These would include charging forklifts and running cold rooms only during off-peak periods, running the dust extractors only during working hours and basing lights and air-conditioning on someone’s presence. - Increase visibility into the factory and other processes. - Enable limited, non-intrusive control functions for certain processes.
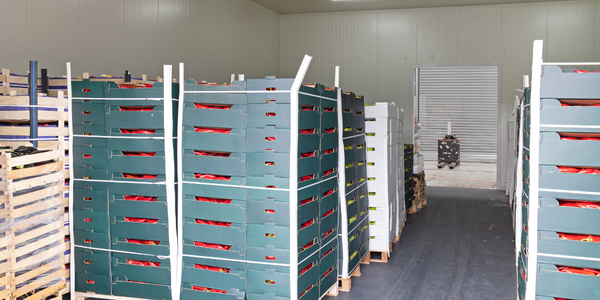
Case Study
Temperature Monitoring for Restaurant Food Storage
When it came to implementing a solution, Mr. Nesbitt had an idea of what functionality that he wanted. Although not mandated by Health Canada, Mr. Nesbitt wanted to ensure quality control issues met the highest possible standards as part of his commitment to top-of-class food services. This wish list included an easy-to use temperature-monitoring system that could provide a visible display of the temperatures of all of his refrigerators and freezers, including historical information so that he could review the performance of his equipment. It also had to provide alert notification (but email alerts and SMS text message alerts) to alert key staff in the event that a cooling system was exceeding pre-set warning limits.
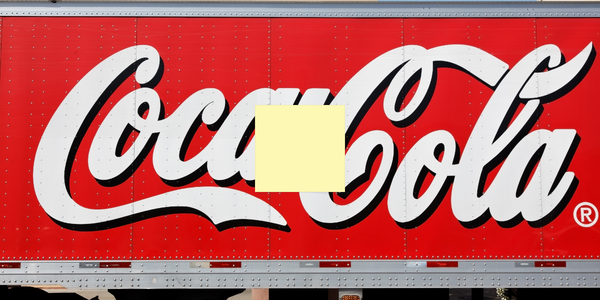
Case Study
Coca-Cola Refreshments, U.S.
Coca-Cola Refreshments owns and manages Coca-Cola branded refrigerators in retail establishments. Legacy systems were used to locate equipment information by logging onto multiple servers which took up to 8 hours to update information on 30-40 units. The company had no overall visibility into equipment status or maintenance history.