公司规模
Mid-size Company
地区
- Europe
国家
- Netherlands
产品
- Field Service 2.0 for Dynamics 365
- Mobile Sales for Dynamics 365
技术栈
- Resco
- Microsoft Dynamics 365
实施规模
- Enterprise-wide Deployment
影响指标
- Environmental Impact Reduction
- Productivity Improvements
- Customer Satisfaction
技术
- 应用基础设施与中间件 - API 集成与管理
适用功能
- 现场服务
- 质量保证
用例
- 远程资产管理
- 机器状态监测
服务
- 系统集成
关于客户
Janssen-Fritsen is the largest manufacturer of physical education equipment in the Netherlands. They also supply equipment for international events such as the Summer Olympics. They are part of ABEO, a leading French group in the sports and leisure market. Over the years, the company has grown considerably, but it continues to operate as a family business. The safety of the equipment is the most important part of Janssen-Fritsen’s business, which is why they carry out regular inspections. As the company grew, its old mobile solution to carry out inspections no longer met its teams’ needs.
挑战
Janssen-Fritsen, a leading manufacturer of physical education equipment, faced a significant challenge as their business grew. Their existing mobile solution for carrying out equipment safety inspections was no longer sufficient. The company needed a mobile app with fast data synchronization that was user-friendly for both inspectors and the back office. The inspectors often had to work in areas with no internet connection, making a reliable offline mode a critical requirement. The company's inspectors carry out equipment safety checks in the field, fill out detailed reports, attach pictures of the equipment, and deliver the reports to their customers. Without fast sync and reliable offline mode, they struggled with slow loading times and inflexible schedule planning.
解决方案
Janssen-Fritsen implemented Resco and built their custom Resco-based solution with the help of their implementation partner, HSO. The Resco app was much more advanced, highly customizable, and had fast sync compared to their previous solution. The most important criteria for the new solution were mobility and ease of use for both the back office and inspectors. The Resco app replaced paper forms with a single mobile app for all their processes. The app also helps the company reduce its CO2 emissions by enabling proper planning of preventive maintenance and timely repairs. The Resco app operates without issues, even under challenging conditions, and has significantly reduced internal emails by managing work orders, scheduling, and reporting in the app.
运营影响
Case Study missing?
Start adding your own!
Register with your work email and create a new case study profile for your business.
相关案例.
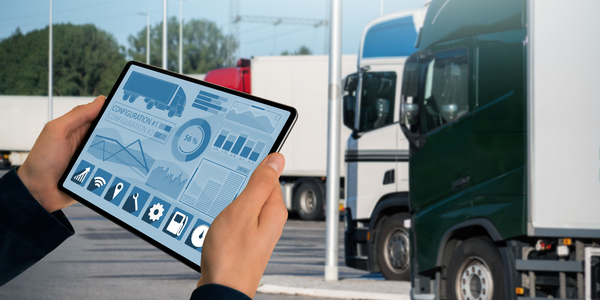
Case Study
IoT enabled Fleet Management with MindSphere
In view of growing competition, Gämmerler had a strong need to remain competitive via process optimization, reliability and gentle handling of printed products, even at highest press speeds. In addition, a digitalization initiative also included developing a key differentiation via data-driven services offers.
.png)
Case Study
Improving Vending Machine Profitability with the Internet of Things (IoT)
The vending industry is undergoing a sea change, taking advantage of new technologies to go beyond just delivering snacks to creating a new retail location. Intelligent vending machines can be found in many public locations as well as company facilities, selling different types of goods and services, including even computer accessories, gold bars, tickets, and office supplies. With increasing sophistication, they may also provide time- and location-based data pertaining to sales, inventory, and customer preferences. But at the end of the day, vending machine operators know greater profitability is driven by higher sales and lower operating costs.
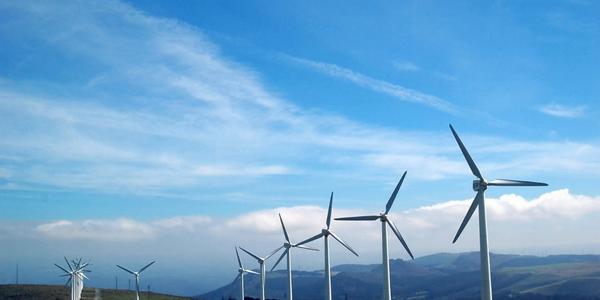
Case Study
Siemens Wind Power
Wind provides clean, renewable energy. The core concept is simple: wind turbines spin blades to generate power. However, today's systems are anything but simple. Modern wind turbines have blades that sweep a 120 meter circle, cost more than 1 million dollars and generate multiple megawatts of power. Each turbine may include up to 1,000 sensors and actuators – integrating strain gages, bearing monitors and power conditioning technology. The turbine can control blade speed and power generation by altering the blade pitch and power extraction. Controlling the turbine is a sophisticated job requiring many cooperating processors closing high-speed loops and implementing intelligent monitoring and optimization algorithms. But the real challenge is integrating these turbines so that they work together. A wind farm may include hundreds of turbines. They are often installed in difficult-to-access locations at sea. The farm must implement a fundamentally and truly distributed control system. Like all power systems, the goal of the farm is to match generation to load. A farm with hundreds of turbines must optimize that load by balancing the loading and generation across a wide geography. Wind, of course, is dynamic. Almost every picture of a wind farm shows a calm sea and a setting sun. But things get challenging when a storm goes through the wind farm. In a storm, the control system must decide how to take energy out of gusts to generate constant power. It must intelligently balance load across many turbines. And a critical consideration is the loading and potential damage to a half-billion-dollar installed asset. This is no environment for a slow or undependable control system. Reliability and performance are crucial.
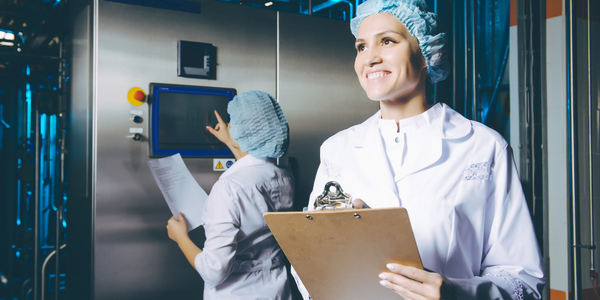
Case Study
Remote Wellhead Monitoring
Each wellhead was equipped with various sensors and meters that needed to be monitored and controlled from a central HMI, often miles away from the assets in the field. Redundant solar and wind generators were installed at each wellhead to support the electrical needs of the pumpstations, temperature meters, cameras, and cellular modules. In addition to asset management and remote control capabilities, data logging for remote surveillance and alarm notifications was a key demand from the customer. Terra Ferma’s solution needed to be power efficient, reliable, and capable of supporting high-bandwidth data-feeds. They needed a multi-link cellular connection to a central server that sustained reliable and redundant monitoring and control of flow meters, temperature sensors, power supply, and event-logging; including video and image files. This open-standard network needed to interface with the existing SCADA and proprietary network management software.