公司规模
Mid-size Company
地区
- America
国家
- United States
产品
- GPS Insight
技术栈
- GPS Tracking
实施规模
- Enterprise-wide Deployment
影响指标
- Cost Savings
- Environmental Impact Reduction
技术
- 传感器 - 全球定位系统
适用行业
- 矿业
适用功能
- 物流运输
用例
- 车队管理
- 车辆性能监测
服务
- 系统集成
关于客户
Kennecott Utah Copper is a medium-sized copper mining company operating in the United States. The company's operations are unique in that its vehicles don't traverse great distances but are spread out across a 25-mile stretch of land. This makes it difficult to manage their large fleet of vehicles. The company has been recognized for its efforts in pollution prevention, receiving a 2008 Outstanding Achievement Award in Pollution Prevention from the Utah Pollution Prevention Association. They were also nominated for an EPA award as a result of their continuous improvement in pollution prevention.
挑战
Kennecott Utah Copper’s (KUC) operation is unique in that its vehicles don’t traverse great distances but are spread out across a 25 mile stretch of land, which made it difficult to manage their large fleet of vehicles. The most significant issue they were having was in monitoring and policing their idle activity. Equipment would be left idling for hours on end, and managers knew they were producing large amounts of Green House Gas (GHG) as a result. The excessive idling was also leading to warranty issues. Kenny Harvey added, “As our equipment idled we lost valuable warranty coverage due to the fact that the manufacturers of our Light and Heavy Equipment were basing warranty coverage off of hours run, not miles driven.” Equipment utilization was also an issue. They needed to find a way to track equipment utilization in order to improve efficiency and vehicle availability by right-sizing their fleet. These issues needed to be addressed to ensure vehicles were operating efficiently throughout and completing their contractual or operational lifecycle.
解决方案
KUC implemented GPS Insight in late 2008 when it began to monitor idle time and GHG emissions on 28 Vehicle Assets. Since that time, the GPS Insight solution has enabled KUC to far exceed their original expectations. They have now implemented multiple programs and business improvement projects as a result of, and through the use of, the GPS Insight data. They are currently monitoring 242 Vehicle Assets, and are using the solution to track Preventative Maintenance intervals and alerts, ensuring proper routing of service vehicles, fuel savings, idle reduction, GHG reduction, and monitoring fleet utilization and availability. GPS Insight provides a wide variety of management tools that are invaluable, but only if it is utilized. There are many variants of reporting that a company can use to bring about huge gains in productivity and fuel savings, as well as large reductions in maintenance costs. GPS Insight will help your organization customize these tools to ensure they’re relevant to your operation.
运营影响
数量效益
Case Study missing?
Start adding your own!
Register with your work email and create a new case study profile for your business.
相关案例.
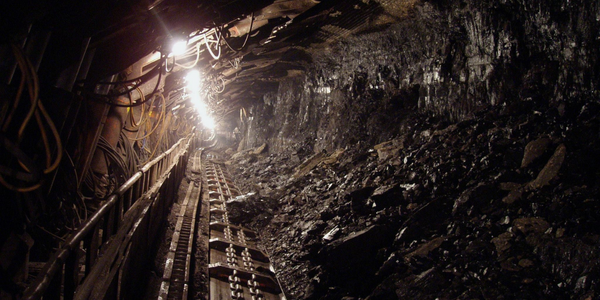
Case Study
Underground Mining Safety
The goal was to produce a safety system to monitor and support underground mining operations; existing systems were either too simple (i.e. phone line) or overly complex and expensive, inhibiting deployment, and providing little-to-no support in event of an accident. Given the dangerous nature of the mining work environment and the strict regulations placed on the industry, the solution would have to comply with Mine Safety and Health Administration (MSHA) regulations. Yet the product needed to allow for simple deployment to truly be a groundbreaking solution - increasing miner safety and changing daily operations for the better.
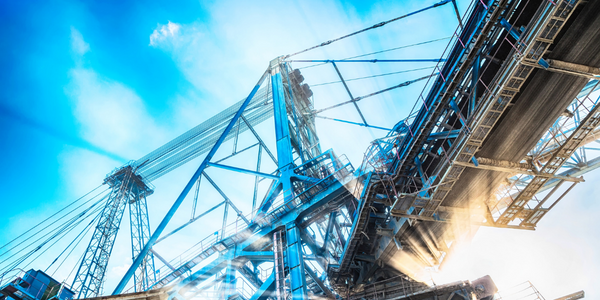
Case Study
Mining Firm Quadruples Production, with Internet of Everything
Dundee Precious Metal’s flagship mine, in Chelopech, Bulgaria, produces a gold, copper, and silver concentrate set a goal to increase production by 30%. Dundee wanted to increase production quality and output without increasing headcount and resources, improve miner safety, and minimize cost.
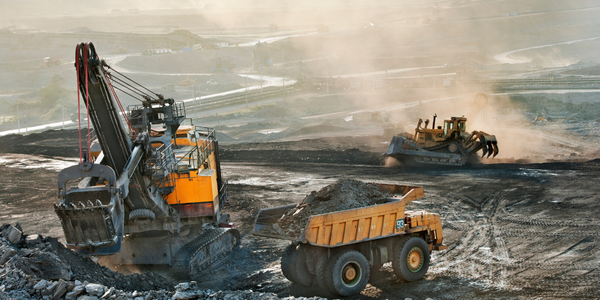
Case Study
Fastenal Builds the Future of Manufacturing with MachineMetrics
Fastenal's objective was to better understand their machine downtime, utilization, quality issues, and to embrace cutting-edge manufacturing technology/process improvement capabilities to bring their team to the next level. However, there was a lack of real-time data, visualization, and actionable insights made this transition impossible.
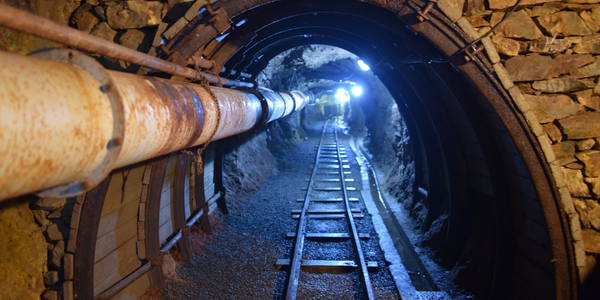
Case Study
Joy Mining Systems
Joy equipment faces many challenges. The first is machine integration and control. The business end of the machine has a rapidly-spinning cylinder with 6-inch diamond-studded cutting teeth. It chews through rock at rates measured in tens of tons per minute. The system grinds through the rock in front, creating a rectangular mine tunnel. Hydraulic lifters support the ceiling as the machine moves forward. Automated drills and screws drive 3-ft long screws into the ceiling to stabilize it. The rock and coal fall into a set of gathering "fingers" below the cutting cylinder. These fingers scoop up the rock and coal and deposit it onto a conveyor belt. The conveyor passes under the machine and out the back. A train of conveyor belt cars, up to a mile long, follows the cutter into the mine. The rock shoots along this train at over 400 feet per minute until it empties into rail cars at the end. Current systems place an operator cage next to the cutter. Choking dust (potentially explosive), the risk of collapse and the proximity of metal and rock mayhem make the operator cage a hazardous location.
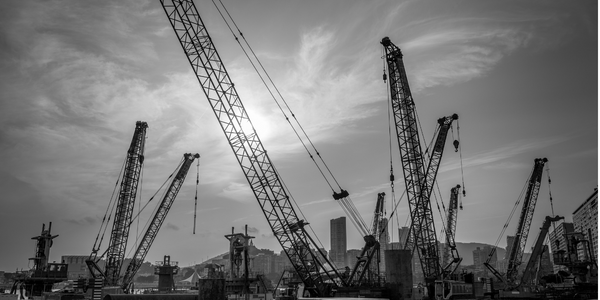
Case Study
Improved Monitoring in Industrial Manufacturing Facility
When your crane is moving tons of magma-hot iron, you can’t afford an unexpected failure. McWane Ductile knew monitoring the crane motor metrics within their facility could help prevent a mechanical failure that would strand an enormous bucket of molten metal overhead. Unfortunately, their legacy wired monitoring system couldn’t work with moving objects in this extreme environment. If they could integrate wireless capabilities into their existing equipment they could extend their monitoring capabilities without starting over from scratch.