Hybrid Android mobile application provides better control over field service orders
公司规模
SME
地区
- America
国家
- Brazil
产品
- Blink Mobility Platform
- Sankhya ERP
技术栈
- HTML5
- Android
- iOS
- Amazon Cloud
实施规模
- Enterprise-wide Deployment
影响指标
- Customer Satisfaction
- Digital Expertise
- Productivity Improvements
技术
- 应用基础设施与中间件 - 数据交换与集成
- 基础设施即服务 (IaaS) - 云计算
- 平台即服务 (PaaS) - 连接平台
适用行业
- 建筑与基础设施
- 公用事业
适用功能
- 现场服务
- 维护
用例
- 预测性维护
- 远程资产管理
服务
- 云规划/设计/实施服务
- 软件设计与工程服务
- 系统集成
关于客户
AC/DC Engenharia Ltda is an engineering and construction company based in Florianopolis, Brazil. They provide services to the electrical generation, transmission and distribution industry. Those services range from project planning and technical consulting, system design and installation, to the inspection and maintenance of measurement and control systems within electrical installations. AC/DC Engenharia employs around 40 field technicians and provides services to many organizations across Brazil’s 26 states and territories. AC/DC is supported by OneBlink’s South American distributor CRE-8 Mobility and has begun its use of the Blink Mobility Platform with its ‘Service Orders App’ tightly integrated with its Sankhya ERP system.
挑战
The first challenge was the amount of time spent by valuable field technicians having to come to the office every day. Previously the team of around 40 AC/DC field technicians were required to come their local branch office every morning to collect their work/service orders for that day. This involved the AC/DC branch Team Leader or supervisor arriving early each morning to first print and then assign each service order/s within their respective field maintenance team. The teams would complete these paper-based forms during the day, building reports based on the data collected from each of their inspections. These paper-based forms were then manually entered into the Sankhya ERP the next day after the technicians returned to the office to collect the next day’s service orders. These paper-based forms were left in the office/s to become the responsibility of a data entry team. Re-entering this data was time-consuming, inefficient and susceptible to errors, this would often cause additional wasted time inside the ERP identifying and correcting data. Having identified that a focused ‘Service Orders App’ could streamline much of the service/inspection process, the second challenge any mobility solution had to consider was the broad mix of mobile devices in Brazil. AC/DC wanted to use their employee’s current devices as a way of minimizing additional investment, which forced a requirement that any app development cover multiple OS’s including Android, iOS and Windows. Therefore, to ensure one development effort could be applied to all device types and to make the maintenance and updating of the various apps as efficient as possible, OneBlink’s Enterprise Mobility Platform was the selected underlying technology.
解决方案
The Blink Mobility Platform is perfectly suited to modeling existing paper-based work practices to today’s mobile devices in the form of highly customized activity-based enterprise apps. The Blink Mobility Platform is provided as a high availability managed service that straddles the areas of MADP (Mobile Application Development Platform), IaaS (Infrastructure-as-a-Service) and mBaaS (mobile Backend-as-a-Service) and runs in the Amazon cloud with a Brazilian point-of-presence. Many inbuilt features within the Blink Mobility Platform automate much of the ‘heavy lifting’ of traditional app development, dramatically reducing the time between scoping of projects and ‘go live’. CRE-8 used the capability of the Blink Mobility Platform and began with development of a hybrid Android app (HTML5 based app supported by a native Android app shell) for AC/DC’s 40 field technicians. While the same code base can easily be applied to iOS devices as well, the initial Android functionality was vital due to its dominance in the Brazilian market. The solution works equally well on Android tablets as well as iOS devices and has enabled the Team Leader to better manage the technicians while in the field, assigning new service orders and prioritizing tasks in real time, saving time overall while addressing urgent needs more effectively. It now takes far less time to collect the data and complete each service call while the data collected is also more comprehensive and in-depth. The capturing of contextual data (GPS, photo, date/time) adds even more value and importantly works offline (i.e., when there is no or unreliable internet connection).
运营影响
数量效益
Case Study missing?
Start adding your own!
Register with your work email and create a new case study profile for your business.
相关案例.

Case Study
IoT Solutions for Smart City | Internet of Things Case Study
There were several challenges faced: It is challenging to build an appliance that can withstand a wide range of voltage fluctuations from as low at 90v to as high as 320v. Since the device would be installed in remote locations, its resilience was of paramount importance. The device would have to deal with poor network coverage and have the ability to store and re-transmit data if networks were not available, which is often the case in rural India. The device could store up to 30 days of data.
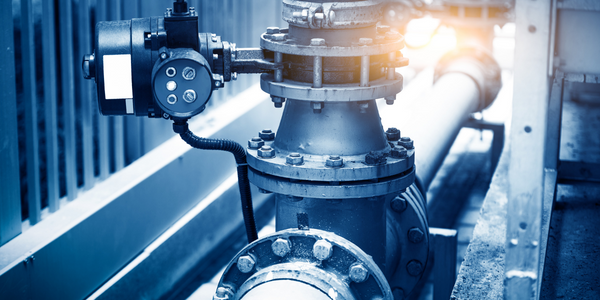
Case Study
Automation of the Oguz-Gabala-Baku water pipeline, Azerbaijan
The Oguz-Gabala-Baku water pipeline project dates back to plans from the 1970’s. Baku’s growth was historically driven by the booming oil industry and required the import of drinking water from outside of the city. Before the construction of the pipeline, some 60 percent of the city’s households received water for only a few hours daily. After completion of the project, 75 percent of the two million Baku residents are now served around the clock with potable water, based on World Health Organization (WHO) standards. The 262-kilometer pipeline requires no pumping station, but uses the altitude differences between the Caucasian mountains and the capital to supply 432,000 m³/d to the Ceyranbatan water reservoir. To the people of Baku, the pipeline is “the most important project not only in 2010, but of the last 20 years.”
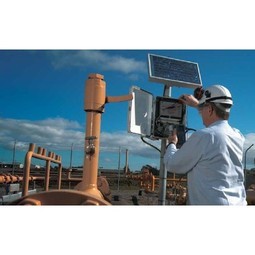
Case Study
GPRS Mobile Network for Smart Metering
Around the world, the electricity supply industry is turning to ‘smart’ meters to lower costs, reduce emissions and improve the management of customer supplies. Smart meters collect detailed consumption information and using this feedback consumers can better understand their energy usage which in turn enables them to modify their consumption to save money and help to cut carbon emissions. A smart meter can be defined in many ways, but generally includes an element of two-way communication between the household meter and the utility provider to efficiently collect detailed energy usage data. Some implementations include consumer feedback beyond the energy bill to include online web data, SMS text messages or an information display in consumers’ premises. Providing a cost-effective, reliable communications mechanism is one of the most challenging aspects of a smart meter implementation. In New Zealand, the utilities have embraced smart metering and designed cost effective ways for it to be implemented. The New Zealand government has encouraged such a move to smart metering by ensuring the energy legislation is consistent with the delivery of benefits to the consumer while allowing innovation in this area. On the ground, AMS is a leader in the deployment of smart metering and associated services. Several of New Zealand’s energy retailers were looking for smart metering services for their residential and small business customers which will eventually account for over 500,000 meters when the multi-year national deployment program is concluded. To respond to these requirements, AMS needed to put together a solution that included data communications between each meter and the central data collection point and the solution proposed by Vodafone satisfied that requirement.
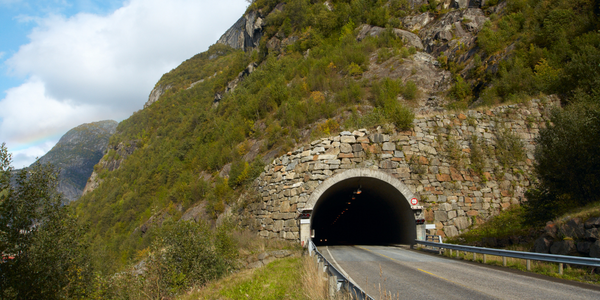
Case Study
IoT System for Tunnel Construction
The Zenitaka Corporation ('Zenitaka') has two major business areas: its architectural business focuses on structures such as government buildings, office buildings, and commercial facilities, while its civil engineering business is targeted at structures such as tunnels, bridges and dams. Within these areas, there presented two issues that have always persisted in regard to the construction of mountain tunnels. These issues are 'improving safety" and "reducing energy consumption". Mountain tunnels construction requires a massive amount of electricity. This is because there are many kinds of electrical equipment being used day and night, including construction machinery, construction lighting, and ventilating fan. Despite this, the amount of power consumption is generally not tightly managed. In many cases, the exact amount of power consumption is only ascertained when the bill from the power company becomes available. Sometimes, corporations install demand-monitoring equipment to help curb the maximum power demanded. However, even in these cases, the devices only allow the total volume of power consumption to be ascertained, or they may issue warnings to prevent the contracted volume of power from being exceeded. In order to tackle the issue of reducing power consumption, it was first necessary to obtain an accurate breakdown of how much power was being used in each particular area. In other words, we needed to be able to visualize the amount of power being consumed. Safety, was also not being managed very rigorously. Even now, tunnel construction sites often use a 'name label' system for managing entry into the work site. Specifically, red labels with white reverse sides that bear the workers' names on both sides are displayed at the tunnel work site entrance. The workers themselves then flip the name label to the appropriate side when entering or exiting from the work site to indicate whether or not they are working inside the tunnel at any given time. If a worker forgets to flip his or her name label when entering or exiting from the tunnel, management cannot be performed effectively. In order to tackle the challenges mentioned above, Zenitaka decided to build a system that could improve the safety of tunnel construction as well as reduce the amount of power consumed. In other words, this new system would facilitate a clear picture of which workers were working in each location at the mountain tunnel construction site, as well as which processes were being carried out at those respective locations at any given time. The system would maintain the safety of all workers while also carefully controlling the electrical equipment to reduce unnecessary power consumption. Having decided on the concept, our next concern was whether there existed any kind of robust hardware that would not break down at the construction work site, that could move freely in response to changes in the working environment, and that could accurately detect workers and vehicles using radio frequency identification (RFID). Given that this system would involve many components that were new to Zenitaka, we decided to enlist the cooperation of E.I.Sol Co., Ltd. ('E.I.Sol') as our joint development partner, as they had provided us with a highly practical proposal.
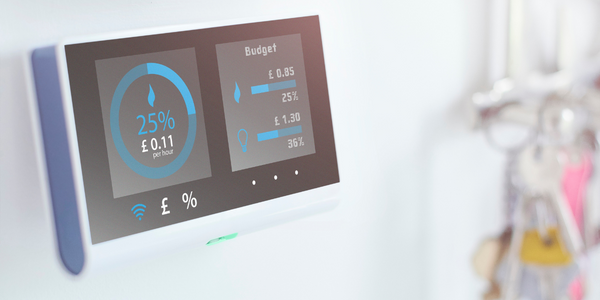
Case Study
NB-IoT connected smart meters to improve gas metering in Shenzhen
Shenzhen Gas has a large fleet of existing gas meters, which are installed in a variety of hard to reach locations, such as indoors and underground, meaning that existing communications networks have struggled to maintain connectivity with all meters. The meter success rate is low, data transmissions are so far unstable and power consumption is too high. Against this background, Shenzhen Gas, China Telecom, Huawei, and Goldcard have jointly trialed NB-IoT gas meters to try and solve some of the challenges that the industry faces with today’s smart gas meters.
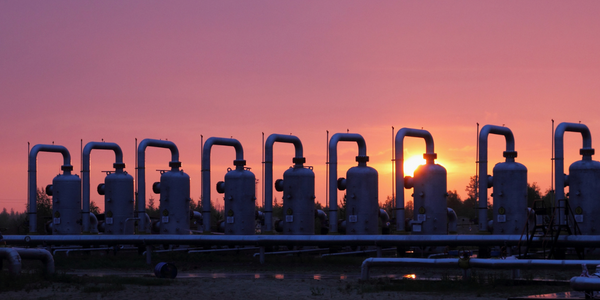
Case Study
British Gas Modernizes its Operations with Innovative Smart Metering Deployment
The UK government has mandated that smart meters are rolled out as standard across Great Britain by end of 2020, and this roll-out is estimated to create £14 billion in net benefits to the UK in consumer energy savings and lower energy generation demand, according to the Oxford Economics report, “The Value of Smart Metering to Great Britain.” While smart-metering systems have been deployed in many countries, the roll-out in Great Britain is unique because it is led by energy retailers, who have responsibility for the Electricity and Gas meters. The decision to have a retailer-led roll out was made by DECC (Department of Energy and Climate Change) to improve customer experience and drive consumer benefits. It has also led to some unique system-level requirements to support the unique local regulatory model.