公司规模
Large Corporate
地区
- Europe
国家
- Belgium
产品
- WebFOCUS
- iWay Software
技术栈
- Business Intelligence
- Data Integration
实施规模
- Enterprise-wide Deployment
影响指标
- Productivity Improvements
- Customer Satisfaction
技术
- 分析与建模 - 实时分析
适用行业
- 海洋与航运
- 汽车
适用功能
- 物流运输
- 离散制造
用例
- 供应链可见性(SCV)
- 实时定位系统 (RTLS)
服务
- 系统集成
- 数据科学服务
关于客户
International Car Operators (ICO) is a world-leading stevedoring company that handles roll-on/roll-off cargo operations. They are a leader in international vehicle transport, processing about 1,600,000 vehicles each year with a fleet of more than 1,000 ships. Headquartered in Antwerp and Zeebrugge, in Belgium, ICO ensures optimum productivity in all roll-on/roll-off processes, vehicle handling, and other logistics activities. ICO’s terminals are Europe’s second-largest vehicle transportation hubs. ICO owns several terminals where vehicles bound for export get to their destination by rail, by road, or by sea. It’s also within these terminals that ships are unloaded, before materials are sorted and sent to their final destinations. In addition to the organization and management of vehicle-transportation logistic chains, ICO also provides several other services.
挑战
International Car Operators (ICO) is a leading company in the material-handling industry, specializing in loading and unloading cargo ships. They offer a broad range of logistics services related to terminals, vessels, shipping agencies, vehicle support, and customs clearance. The company faced a challenge in offering a system that would facilitate the efficient processing and sharing of information between entering ships, material-handling and logistic service providers, and customers. They needed a system that could collate all available information and present it to customers in the most convenient and accessible way possible. The information should also be available to support key business processes.
解决方案
To fulfill its mission, ICO developed its own computer platform that was strengthened with the addition of WebFOCUS from Information Builders. ICO chose WebFOCUS for its ability to easily manage multiple sources of information and to simultaneously serve a large number of users, for both operational and reporting needs. ICO also uses Information Builders iWay adapters to facilitate smooth integration of data coming from various platforms. At Antwerp’s terminal, iWay essentially provides all “pre-announcements” processing. When a ship sails to one of ICO’s terminals, iWay adapters convert all vehicle information into operational data. iWay also monitors each vehicle’s follow-up, and other aspects of its life cycle. This vast array of information opens up other opportunities that go beyond simple operational processes. For ICO, reporting on the various aspects of its operations is too critical a process to be neglected. The company is therefore determined to expand its reporting capabilities throughout the entire organization.
运营影响
Case Study missing?
Start adding your own!
Register with your work email and create a new case study profile for your business.
相关案例.
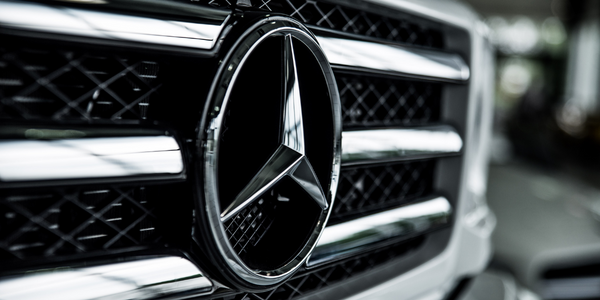
Case Study
Integral Plant Maintenance
Mercedes-Benz and his partner GAZ chose Siemens to be its maintenance partner at a new engine plant in Yaroslavl, Russia. The new plant offers a capacity to manufacture diesel engines for the Russian market, for locally produced Sprinter Classic. In addition to engines for the local market, the Yaroslavl plant will also produce spare parts. Mercedes-Benz Russia and his partner needed a service partner in order to ensure the operation of these lines in a maintenance partnership arrangement. The challenges included coordinating the entire maintenance management operation, in particular inspections, corrective and predictive maintenance activities, and the optimizing spare parts management. Siemens developed a customized maintenance solution that includes all electronic and mechanical maintenance activities (Integral Plant Maintenance).
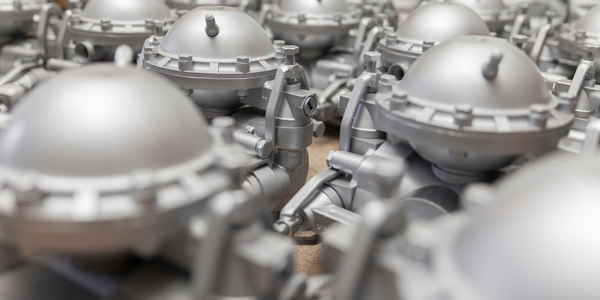
Case Study
Monitoring of Pressure Pumps in Automotive Industry
A large German/American producer of auto parts uses high-pressure pumps to deburr machined parts as a part of its production and quality check process. They decided to monitor these pumps to make sure they work properly and that they can see any indications leading to a potential failure before it affects their process.