Identifying data patterns and mining insights about user behaviour to ensure maximum customer satisfaction
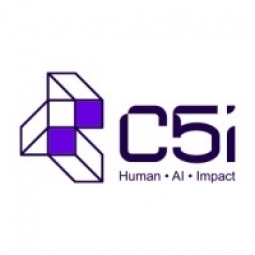
公司规模
Large Corporate
产品
- SQL engine
技术栈
- SQL
实施规模
- Enterprise-wide Deployment
影响指标
- Customer Satisfaction
- Productivity Improvements
技术
- 分析与建模 - 数据挖掘
- 分析与建模 - 实时分析
适用功能
- 质量保证
- 产品研发
用例
- 质量预测分析
- 根因分析与诊断
服务
- 数据科学服务
关于客户
The customer in this case study is a leading technology multinational company. The company operates in the Information Technology industry and has a large user base. The company has multiple products with various functionalities. The company was looking to improve its customer satisfaction by ensuring ease of navigation and user preferability. The company had huge volumes of user experience data and wanted to mine insights from this data. The company also wanted to improve its software quality and was looking for ways to identify patterns in data and make data cuts to suggest linkages in constituents which otherwise seemed to be absolutely disjoint.
挑战
Blueocean Market Intelligence’s client, a leading technology multinational, had huge volumes of user experience data and wanted to mine insights to enhance the user experience. The goal was to improve customer satisfaction by ensuring ease of navigation and user preferability. This included identifying patterns in data and making data cuts to suggest linkages in constituents which otherwise seemed to be absolutely disjoint. The client also wanted to give pointers to the software quality management team for ensuring better quality. The client was faced with key questions such as: Are users enjoying the experience as they navigate through the product? Is the GUI comfortable for the user? What causes bugs? How can the User Interface (UI) be improved?
解决方案
Blueocean Market Intelligence collated requisite data points on the SQL engine. There were five products with multiple functionalities. The available user data was correlated with various other pieces of information to drive meaningful insights. Based on frequency of occurrence of events, usage reports were prepared. These reports included slicing and dicing of data and analyzing different data points giving information, which was otherwise hidden. Also, root cause analysis was conducted for uncovering bugs and finding plausible solutions for bug fixing. Finally, dashboards were prepared for intuitive representation of information. For each of the functionality, user behavior was compared across products. For each of the product, analysis was conducted across various versions. The client approached with questions about user preferability of different applications. Using expertise in data analysis, Blueocean Market Intelligence prepared reports with key findings from the data pointers. Along with the important findings, recommendations were given for impactful execution.
运营影响
数量效益
Case Study missing?
Start adding your own!
Register with your work email and create a new case study profile for your business.
相关案例.
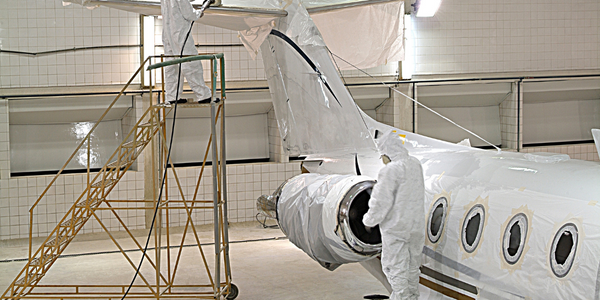
Case Study
Aircraft Predictive Maintenance and Workflow Optimization
First, aircraft manufacturer have trouble monitoring the health of aircraft systems with health prognostics and deliver predictive maintenance insights. Second, aircraft manufacturer wants a solution that can provide an in-context advisory and align job assignments to match technician experience and expertise.
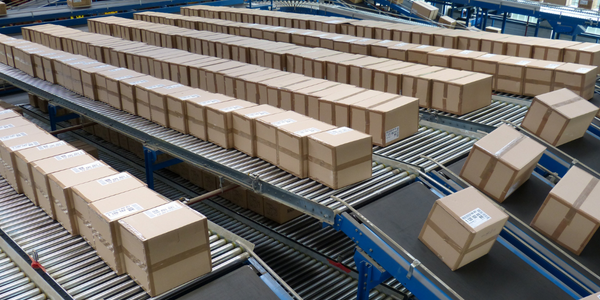
Case Study
IoT Data Analytics Case Study - Packaging Films Manufacturer
The company manufactures packaging films on made to order or configure to order basis. Every order has a different set of requirements from the product characteristics perspective and hence requires machine’s settings to be adjusted accordingly. If the film quality does not meet the required standards, the degraded quality impacts customer delivery causes customer dissatisfaction and results in lower margins. The biggest challenge was to identify the real root cause and devise a remedy for that.
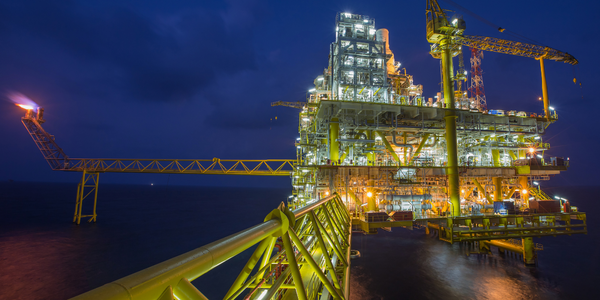
Case Study
Large Oil Producer Leverages Advanced Analytics Platform
Approximately 17,000 wells in the customer's portfolio have beam pump artificial lift technology. While beam pump technology is relatively inexpensive compared to other artificial lift technology, beam pumps fail frequently, at rates ranging from 66% to 95% per year. Unexpected failures result in weeks of lost production, emergency maintenance expenses, and costly equipment replacements.
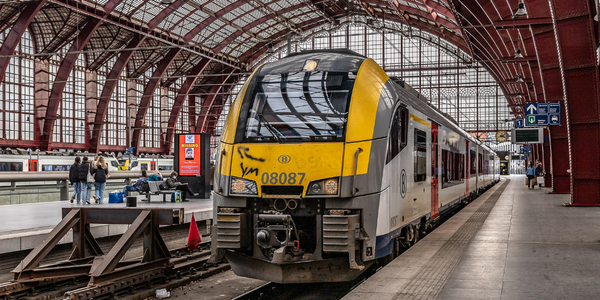
Case Study
The Internet of Trains
Train operators the world over are expected to work miracles, i.e. never to be late. So, with acute service and availability targets to meet, an efficient maintenance program is important. And data-enabled functionality is a must for Siemens. Reactive maintenance (after an incident) and routine, preventive maintenance with its visual inspections and scheduled exchange of components, are no longer enough. We’ve moved on to more cost-effective, condition-based, predictive maintenance. The actual condition of components is measured via the transfer and remote monitoring of diagnostic sensor data; data which is also used to analyse patterns and trends. This helps predict when a component is likely to fail, so it can be repaired before anything untoward happens. To ensure the commercial sustainability of this approach, Siemens needs to use and re-use existing data, creating a kind of ‘Internet of Trains’. Towards this end, they’re analysing sensor data in near real time, which means they can react very quickly, ensuring that customer transport services aren’t interrupted. “It is really difficult to define every issue before it impacts operations using only data from the trains”, Kress explains. However, recent success stories prove that everything is possible.
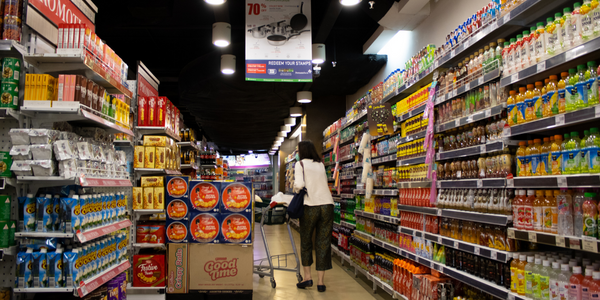
Case Study
FMCG Case Study – CPG Line Monitoring
The leading CPG company operates several warehouses, mostly closer to the last distribution point (Large retailers). Products in various categories are packaged in specific delivery or display cartons at these facilities. As most CPG businesses consist of high volume with low margins, optimizing every operation and effective utilization of resources add up to profit margins. The key problem at these warehouses is the lack of visibility into reasons for machine breakdowns or idle time, thereby delay in delivery. The sunrise meetings lead to post-mortem of delivery issues like delay or quality. The customer wanted to implement real-time line monitoring and alert system to gain control over downtime issues and implement improvement measures.
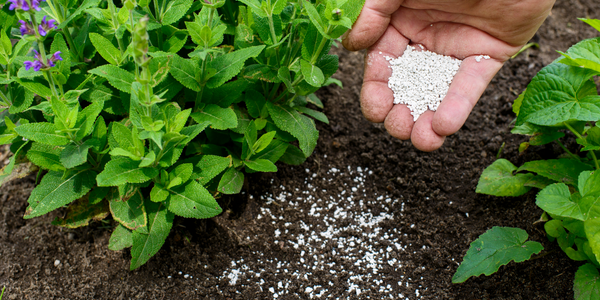
Case Study
Vale Fertilizantes Saves $1.4M in Production Losses with Predix Asset Performanc
Reducing production lossesIn 2013, the company identified a need in the maintenance and operation of its acid nitric plant to reduce production losses and improve annual production. Vale noticed there was a gap in nitric acid production from 2011 to 2012 and discovered that three pieces of equipment were responsible for the main losses, including two weak acid condensers and a compressor discharge air cooler. The condenser’s losses were due to thickness loss, lack of availability of the spare condenser, and shell cracking.With a production loss above 14,000 tons in 15 months, Vale aimed to reduce annual loss by 10,000 tons by August 2015.