LEVC Identifies 25-40% Savings on All Systems Estimated with aPriori
公司规模
Large Corporate
地区
- Europe
- Asia
国家
- United Kingdom
- China
产品
- aPriori
技术栈
- 3D CAD Models
- Digital Twin
实施规模
- Enterprise-wide Deployment
影响指标
- Cost Savings
- Productivity Improvements
技术
- 分析与建模 - 数字孪生/模拟
- 功能应用 - 产品生命周期管理系统 (PLM)
适用行业
- 汽车
适用功能
- 产品研发
- 采购
用例
- 预测性维护
服务
- 软件设计与工程服务
- 系统集成
关于客户
Hailing an iconic black cab in London has long been considered a safe and reliable premium service synonymous with the city. Today, with the transportation sector flooded with competition, and the current focus on turning London into an electric city, the rebirth of the black cab came at just the right time. Realizing their potential, The London Taxi Company – the original black cab company – was purchased by Geely of China in 2013. The resurrection of the iconic black cab combined with the city’s new zero emission policy on all taxis has evolved into The London Electric Vehicle Company. LEVC’s black cabs are sold to independent taxi owners in and around the city, as well as fleets and independent owners in cities worldwide. According to their website, their company goal is to “change the world and make cities cleaner and greener for everyone, where air pollution is a thing of the past and easy, comfortable and safe transportation is accessible to all.” Dr. Scott Hunter-Saphir is the Projects Controller at LEVC. His essential responsibility is managing all the budgetary requirements relating to spend, scope, concept, and delivery around projects that are initiated on the engineering side.
挑战
As a new business creating a new design with a new team, a new factory, and a new supply base, the number one priority for LEVC was getting to market quickly with a high quality product. This drove a focus on delivery at the expense of an integrated manufacturing costing strategy. The closer they got to launch, the more apparent it became that they hadn’t put as much into the cost management side of the vehicle as they should have. It was during this time that LEVC committed to developing a cohesive cost strategy going forward. Once this priority was established, LEVC realized they needed some type of tool and process to help identify where they could reduce costs both internally and with suppliers in the future.
解决方案
LEVC is now using aPriori to generate detailed manufacturability data and costs for a wide variety of components. Internal assessments of their own costing results and approach has helped them to identify new and potentially valuable cost-down projects their team could analyze in the future. The process started with a comprehensive costing exercise on the metal structure parts of the car, which has already started to return some strong financial results and beneficial engagement with their suppliers. LEVC also conducted a full bottom up costing analysis on the interior of the vehicle, where there are several plastic injection molded parts. Before using aPriori, the company spent significant time and money looking to retool parts and move them out to China. The problem they encountered was their volumes were much lower than other manufacturers with similar types of vehicles, so their payback time to retool would be much longer. When you add to that the shipping costs and import duties, the costs were prohibitive, despite the usually expected savings from low cost production centers. aPriori helped LEVC identify a better way – using their current supply base – and use that to start discussions with suppliers about where they could become more efficient – without the need for retooling.
运营影响
数量效益
Case Study missing?
Start adding your own!
Register with your work email and create a new case study profile for your business.
相关案例.
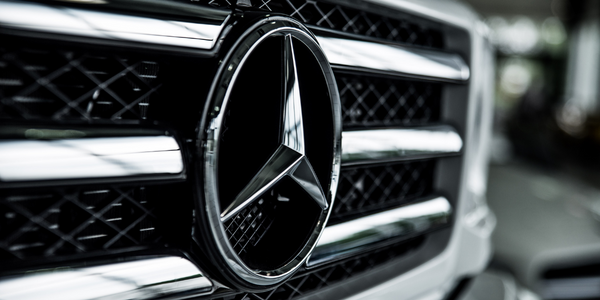
Case Study
Integral Plant Maintenance
Mercedes-Benz and his partner GAZ chose Siemens to be its maintenance partner at a new engine plant in Yaroslavl, Russia. The new plant offers a capacity to manufacture diesel engines for the Russian market, for locally produced Sprinter Classic. In addition to engines for the local market, the Yaroslavl plant will also produce spare parts. Mercedes-Benz Russia and his partner needed a service partner in order to ensure the operation of these lines in a maintenance partnership arrangement. The challenges included coordinating the entire maintenance management operation, in particular inspections, corrective and predictive maintenance activities, and the optimizing spare parts management. Siemens developed a customized maintenance solution that includes all electronic and mechanical maintenance activities (Integral Plant Maintenance).
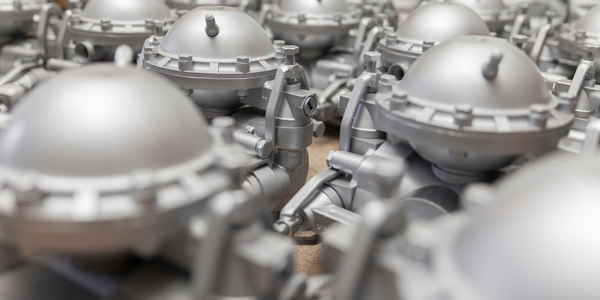
Case Study
Monitoring of Pressure Pumps in Automotive Industry
A large German/American producer of auto parts uses high-pressure pumps to deburr machined parts as a part of its production and quality check process. They decided to monitor these pumps to make sure they work properly and that they can see any indications leading to a potential failure before it affects their process.