公司规模
Large Corporate
产品
- eFlex Assembly
技术栈
- PLC logic
- HMI programs
- RFID
实施规模
- Enterprise-wide Deployment
影响指标
- Cost Savings
- Productivity Improvements
技术
- 功能应用 - 制造执行系统 (MES)
适用行业
- 汽车
适用功能
- 离散制造
用例
- 自动化制造系统
服务
- 系统集成
- 软件设计与工程服务
关于客户
The customer in this case study is a global automotive manufacturer. They have two manufacturing plants that produce the same V6 engine with similar production rates and model variants. Each plant has over 100 workstations and can produce up to 200 model variants. The manufacturer is facing challenges with their highly automated fixed tooling line, which is inflexible and costly to change. This has resulted in lost opportunities and a lack of competitiveness in the market. The manufacturer is looking for a solution that allows for rapid changes in production requirements, configurability, distributed control, and plug-and-play capabilities.
挑战
The global automotive manufacturer in this case study had two manufacturing plants producing the same V6 engine with similar production rates and model variants. One plant used the eFlex Assembly architecture, while the other used a highly automated fixed architecture. Both lines had over 100 workstations and up to 200 model variants. Both sites needed to re-rate production and introduce new models. The challenge was that the highly automated fixed tooling line was inflexible, costly, and time-consuming to change. This resulted in lost opportunities and a lack of competitiveness in the market. The manufacturer needed a solution that would allow for rapid changes in production requirements, configurability, distributed control, and plug-and-play capabilities.
解决方案
The solution was the implementation of the eFlex Assembly architecture in one of the manufacturing plants. This architecture allowed for quick line changes without the need for coding, outsourcing, print updates, or extensive engineering work. The plant staff could perform the entire change during a 2-day weekend, with the line running at rate by midday on Monday. The eFlex Assembly architecture also allowed for the shutdown to occur over a weekend, with normal production resuming by midday on Monday. This was in stark contrast to the automated fixed tooling line, which required a shutdown of 9 days. The eFlex Assembly architecture also allowed for the creation of a new line configuration offline at the engineer's desk within 6-8 hours, compared to the 480 hours of preparation work required for the automated fixed tooling line.
运营影响
数量效益
Case Study missing?
Start adding your own!
Register with your work email and create a new case study profile for your business.
相关案例.
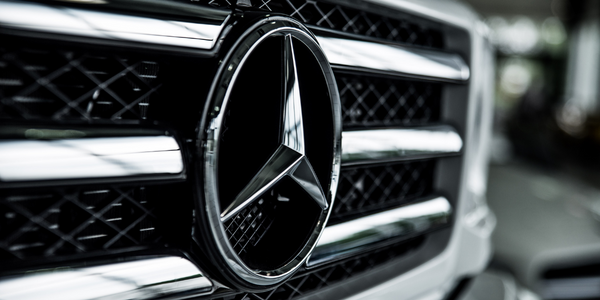
Case Study
Integral Plant Maintenance
Mercedes-Benz and his partner GAZ chose Siemens to be its maintenance partner at a new engine plant in Yaroslavl, Russia. The new plant offers a capacity to manufacture diesel engines for the Russian market, for locally produced Sprinter Classic. In addition to engines for the local market, the Yaroslavl plant will also produce spare parts. Mercedes-Benz Russia and his partner needed a service partner in order to ensure the operation of these lines in a maintenance partnership arrangement. The challenges included coordinating the entire maintenance management operation, in particular inspections, corrective and predictive maintenance activities, and the optimizing spare parts management. Siemens developed a customized maintenance solution that includes all electronic and mechanical maintenance activities (Integral Plant Maintenance).
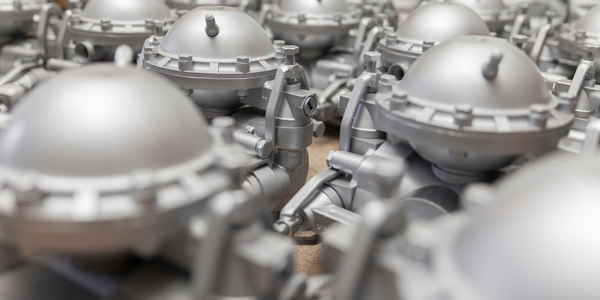
Case Study
Monitoring of Pressure Pumps in Automotive Industry
A large German/American producer of auto parts uses high-pressure pumps to deburr machined parts as a part of its production and quality check process. They decided to monitor these pumps to make sure they work properly and that they can see any indications leading to a potential failure before it affects their process.