公司规模
Large Corporate
地区
- Europe
国家
- Germany
产品
- SAP EH&S
- ARIS
- webMethods
- Adabas
- Natural
- CentraSite
- Terracotta
技术栈
- SAP
- ECC 6.00 EhP5
实施规模
- Enterprise-wide Deployment
影响指标
- Productivity Improvements
- Cost Savings
技术
- 功能应用 - 企业资源规划系统 (ERP)
适用行业
- 化学品
适用功能
- 离散制造
- 质量保证
用例
- 监管合规监控
- 过程控制与优化
服务
- 系统集成
- 软件设计与工程服务
关于客户
林德集团是世界领先的气体和工程公司,在全球 100 多个国家拥有约 50,000 名员工。2010 财年,该集团的销售额达到 128.68 亿欧元。林德集团的战略是实现长期盈利增长,并专注于通过前瞻性产品和服务拓展其国际业务。林德在全球每个业务领域、地区和地点都对其股东、业务合作伙伴、员工、社会和环境负责。林德致力于开发将客户价值和可持续发展目标相结合的技术和产品。
挑战
林德集团是一家世界领先的气体和工程公司,它面临的问题是运行在旧 SAP 版本上的环境合规系统过时。该系统仅符合当前 SAP 标准的 50% 左右,林德需要大量人工才能满足关键的法律要求。该系统容易出错,如果不进行大量人工,就无法满足业务需求。因此,操作和维护成本高昂且效率低下。林德集团需要一个更高效、更标准化的 SAP EH&S 平台。经过一年多对所有选项的考虑,林德选择了 IDS Scheer Consulting 和 3E Company 来承担这项任务。
解决方案
Linde AG 计划用更接近标准的当前软件版本替换现有的 SAP 模块 EH&S。IDS Scheer Consulting 与全球知名的化学、法规和合规信息服务提供商 3E Company 共同管理实施。因此,在欧洲范围内运行的 SAP EH&S 平台也可以重复使用以满足全球需求。在实施过程中,项目团队有三项主要任务:通过在 ECC 6.00 EhP5 上的新独立中央实例上实施 SAP EH&S,使 EH&S 恢复标准;通过集成 3E Company 的法律和规范相关信息内容,构建一个可靠的全球使用模块;通过将 Linde AG 的单独解决方案集成到 SAP EH&S 中,使所有流程在一个 SAP EH&S 模块中保持一致。
运营影响
Case Study missing?
Start adding your own!
Register with your work email and create a new case study profile for your business.
相关案例.
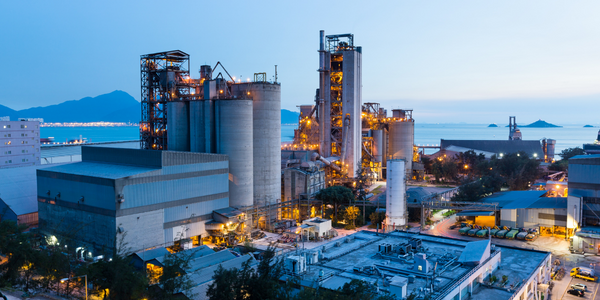
Case Study
Honeywell - Tata Chemicals Improves Data Accessibility with OneWireless
Tata was facing data accessibility challenges in the cement plant control room tapping signals from remote process control areas and other distant locations, including the gas scrubber. Tata needed a wireless solution to extend its control network securely to remote locations that would also provide seamless communication with existing control applications.

Case Study
Advanced Elastomer Systems Upgrades Production
In order to maintain its share of the international market for thermoplastic elastomers AES recently expanded its Florida plant by adding a new production line. While the existing lines were operating satisfactorily using a PROVOX distributed control system with traditional analog I/O, AES wanted advanced technology on the new line for greater economy, efficiency, and reliability. AES officials were anxious to get this line into production to meet incoming orders, but two hurricanes slowed construction.
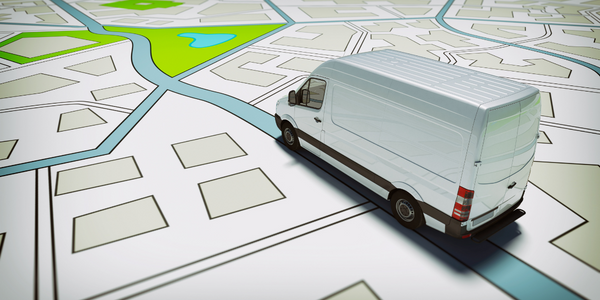
Case Study
Wireless GPS Tracking & Security Monitoring
Enhancing the security of hazardous freight and ensuring compliance with Homeland Security’s Transportation Security Administration mandate that all trains carrying chemicals capable of creating a toxic inhalation condition are equipped with on-board safety monitoring systems.
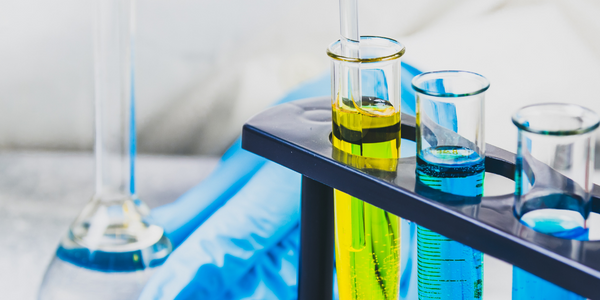
Case Study
Field Device Asset Management For Chemical Company in China
Chinese chemical subsidiary of multinational corporation serves customers throughout the world. Sales offices and research and technology centers are strategically located to provide rapid response to customer requests. Just two workers were assigned to maintain thousands of intelligent instruments in three production units, so they could do little more than react to device issues as they appeared. This costly maintenance method inevitably led to unexpected downtime when a critical instrument failed. Plant management recognized the need to change from reactive to predictive maintenance for all assets, including instruments and control valves, but help was needed in implementing such a technology-based initiative.
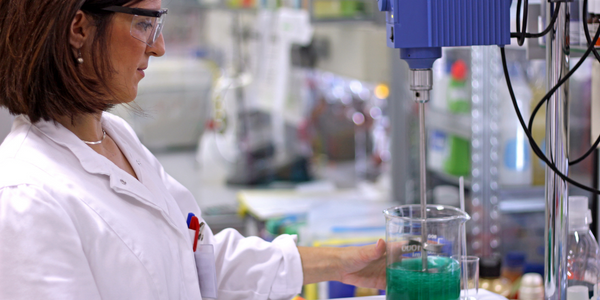
Case Study
Industrial Workforce Mobility for Improved Safety & Operations
Huntsman Corporation, a global manufacturer and marketer of differentiated chemicals, undertook an aggressive program to eliminate injuries, product defects, and environmental releases at their Port Neches facility. Termed “Project Zero”, this program required a completely mobile solution to empower operations and maintenance personnel to capture defects, track work progress and make process and safety related decisions in real-time.