公司规模
Large Corporate
地区
- America
- Asia
- Europe
国家
- United States
- China
- Germany
- Japan
- Mexico
产品
- Plex Manufacturing Cloud
- Plex Smart Manufacturing Platform
技术栈
- Cloud-based ERP
- Real-time data integration
实施规模
- Enterprise-wide Deployment
影响指标
- Productivity Improvements
- Customer Satisfaction
- Innovation Output
技术
- 功能应用 - 企业资源规划系统 (ERP)
- 平台即服务 (PaaS) - 数据管理平台
适用行业
- 汽车
适用功能
- 商业运营
- 质量保证
用例
- 自动化制造系统
- 库存管理
- 过程控制与优化
服务
- 系统集成
- 软件设计与工程服务
关于客户
Motus Integrated Technologies is a privately held Tier 1 supplier of automotive interior products to the world’s automakers. The company’s nearly 4,000 employees produce high-performance headliners, visors, door and console armrests, and instrument panel trim components for the global automotive market from state-of-the-art manufacturing facilities around the world. Headquartered in Michigan, Motus Integrated Technologies has operations in Mexico, Germany, China, and Japan. Motus excels in the automotive industry by producing stylish, functional products that attract car buyers and bring vehicles to life. You can find its products—which include headliners, trays, panels, and trim—inside the world’s most popular vehicles. The company supports its customers from concept to launch with creative design, product and process innovation, and worldwide manufacturing resources. Motus has earned a reputation for superior product design and performance.
挑战
Facing its launch as an independent company, Motus Integrated Technologies needed to move off its QAD MFG/PRO manufacturing system. Motus aimed to upgrade to a new level of solution that would enable it to address its leading business challenges. The company’s paper-based processes limited visibility into production and inventory, and heavy use of spreadsheets hindered analysis of financial and production data. Seeking to implement common business processes on three continents, Motus began looking for a cloud-based ERP solution. As Motus evaluated potential ERP solutions, the company had several priorities. First, because Motus would have faced penalties for not moving off of Johnson Controls’ system promptly, any potential solution had to go live quickly. Second, the new company didn’t want to be burdened with implementing and maintaining a system in house where they’d have to manage databases. Given these priorities, moving to a cloud solution just made sense— and so Motus chose Plex.
解决方案
Once the vendor was selected, Motus went to work on an implementation plan. In just a four-month period in 2015, Motus moved four of its plants to the Plex Manufacturing Cloud. And when Motus purchased Leon Plastics in 2016, the company quickly moved its three newly acquired plants to Plex. In 2018, Motus divested two plants to another investor. Today, all five plants as well as its corporate headquarters run their business on Plex. Due to the sheer variety of products that Motus makes, there’s no typical day in its manufacturing plants. Some facilities are more machine-intensive and less reliant on human effort. Others revolve around assembly lines on which 10 or 12 people may be building products by hand. Moving to Plex has enabled Motus to keep tighter control over these complex operations simply by placing a computer in each work center on the shop floor. In Motus’ previous paper-based processes, manufacturing operators would keep track of production and scrap on paper. Most of this data wasn’t entered into computers until the next shift. As a result, the company’s view of materials and finished goods was perpetually 12 to 16 hours behind. With Plex, this data is available in real time— and several data entry clerks have been reassigned to more valuable tasks within the company. Motus has further increased efficiency by deploying tablets that enable workers to perform inventory cycle counts without walking to the nearest workstation.
运营影响
数量效益
Case Study missing?
Start adding your own!
Register with your work email and create a new case study profile for your business.
相关案例.
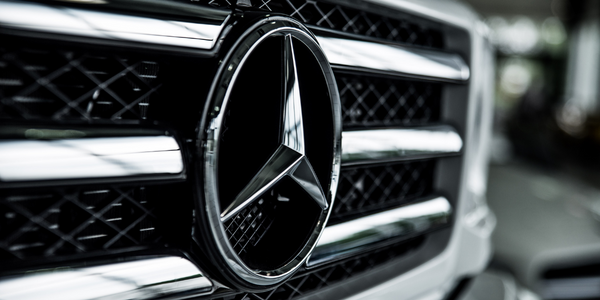
Case Study
Integral Plant Maintenance
Mercedes-Benz and his partner GAZ chose Siemens to be its maintenance partner at a new engine plant in Yaroslavl, Russia. The new plant offers a capacity to manufacture diesel engines for the Russian market, for locally produced Sprinter Classic. In addition to engines for the local market, the Yaroslavl plant will also produce spare parts. Mercedes-Benz Russia and his partner needed a service partner in order to ensure the operation of these lines in a maintenance partnership arrangement. The challenges included coordinating the entire maintenance management operation, in particular inspections, corrective and predictive maintenance activities, and the optimizing spare parts management. Siemens developed a customized maintenance solution that includes all electronic and mechanical maintenance activities (Integral Plant Maintenance).
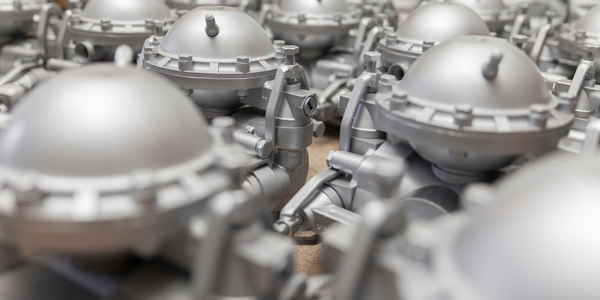
Case Study
Monitoring of Pressure Pumps in Automotive Industry
A large German/American producer of auto parts uses high-pressure pumps to deburr machined parts as a part of its production and quality check process. They decided to monitor these pumps to make sure they work properly and that they can see any indications leading to a potential failure before it affects their process.