公司规模
Mid-size Company
地区
- America
国家
- Mexico
产品
- Plex Cloud ERP
技术栈
- Cloud ERP
实施规模
- Enterprise-wide Deployment
影响指标
- Productivity Improvements
- Customer Satisfaction
- Digital Expertise
技术
- 功能应用 - 企业资源规划系统 (ERP)
适用行业
- 金属
- 汽车
适用功能
- 商业运营
- 质量保证
用例
- 工厂可见化与智能化
- 预测性维护
服务
- 系统集成
关于客户
OKAY Industries, Inc. is a company specializing in stamping, machining, and prototyping, with a focus on producing complex metal stampings with extremely tight tolerances. The company serves a diverse range of industries, including medical and surgical devices, defense, firearms, specialty, industrial, and automotive markets. Known for its precision and commitment to perfection, OKAY Industries operates in a highly demanding environment where there is no room for error. The company is located in Queretaro, Mexico, and is recognized for its culture of continuous improvement, having achieved ISO certification and compliance with new ISO standards. OKAY Industries is dedicated to maintaining high standards of quality and efficiency in its operations.
挑战
OKAY Industries faced a significant challenge in managing its operations due to the existence of 18 different databases that were not integrated with the company's UNIX server. This fragmentation made it difficult to compile detailed information necessary for continuous improvement in operational efficiency. The company needed a solution that could integrate its entire operation, streamline data management, and support its culture of continuous improvement. Additionally, OKAY Industries had to comply with new ISO standards and requirements, which added another layer of complexity to its operations.
解决方案
OKAY Industries implemented Plex Cloud ERP to address its operational challenges. The implementation began with a focus on quality functions, as the company's parts require perfection. The system was customized to track weights up to seven decimal places, ensuring precise quality monitoring. The transition to Plex Cloud ERP involved inputting extensive data, including part numbers and routings, which was initially done by student interns. Once the data was in place, the company used Plex for quality monitoring, which went smoothly. The next phase involved implementing a complex costing system within Plex, allowing OKAY to analyze the cost of producing each part down to the penny. This system provided detailed information on material costs, assembly costs, and manpower, enabling managers to drill down into the data for insights. The implementation was successful, with a dedicated team ensuring internal buy-in and setting a firm go-live date. The result was a smoothly functioning operation with 100% real-time data, enhancing production visibility and decision-making.
运营影响
数量效益
Case Study missing?
Start adding your own!
Register with your work email and create a new case study profile for your business.
相关案例.
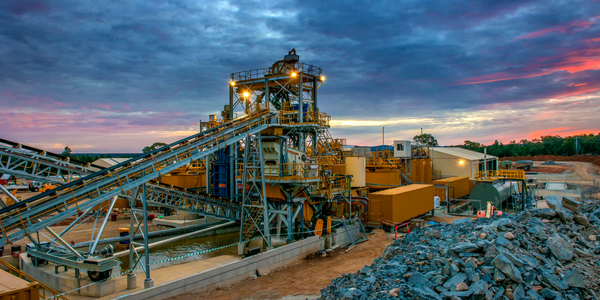
Case Study
Goldcorp: Internet of Things Enables the Mine of the Future
Goldcorp is committed to responsible mining practices and maintaining maximum safety for its workers. At the same time, the firm is constantly exploring ways to improve the efficiency of its operations, extend the life of its assets, and control costs. Goldcorp needed technology that can maximize production efficiency by tracking all mining operations, keep employees safe with remote operations and monitoring of hazardous work areas and control production costs through better asset and site management.
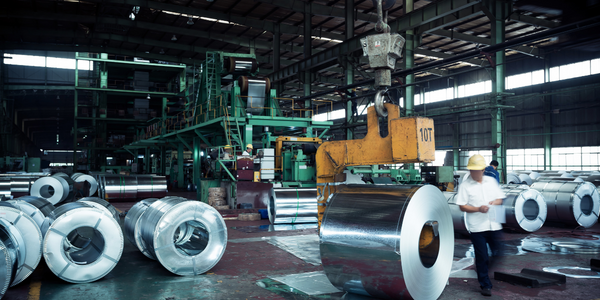
Case Study
KSP Steel Decentralized Control Room
While on-site in Pavlodar, Kazakhstan, the DAQRI team of Business Development and Solutions Architecture personnel worked closely with KSP Steel’s production leadership to understand the steel production process, operational challenges, and worker pain points.
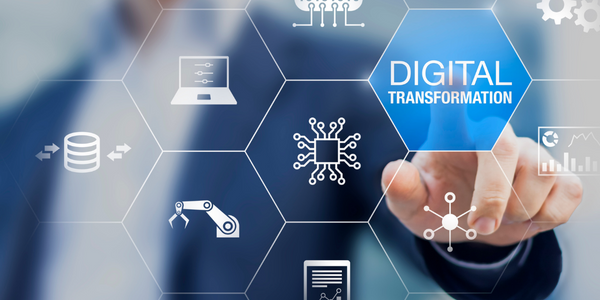
Case Study
Bluescope Steel on Path to Digitally Transform Operations and IT
Increasing competition and fluctuations in the construction market prompted BlueScope Steel to look toward digital transformation of its four businesses, including modern core applications and IT infrastructure. BlueScope needed to modernize its infrastructure and adopt new technologies to improve operations and supply chain efficiency while maintaining and updating an aging application portfolio.
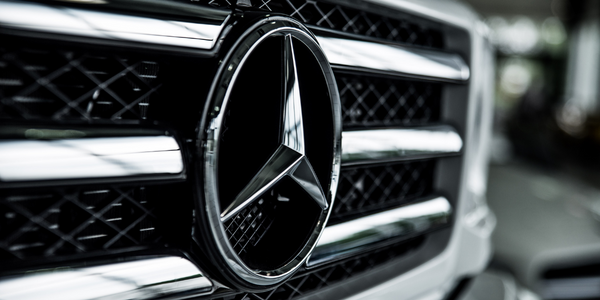
Case Study
Integral Plant Maintenance
Mercedes-Benz and his partner GAZ chose Siemens to be its maintenance partner at a new engine plant in Yaroslavl, Russia. The new plant offers a capacity to manufacture diesel engines for the Russian market, for locally produced Sprinter Classic. In addition to engines for the local market, the Yaroslavl plant will also produce spare parts. Mercedes-Benz Russia and his partner needed a service partner in order to ensure the operation of these lines in a maintenance partnership arrangement. The challenges included coordinating the entire maintenance management operation, in particular inspections, corrective and predictive maintenance activities, and the optimizing spare parts management. Siemens developed a customized maintenance solution that includes all electronic and mechanical maintenance activities (Integral Plant Maintenance).
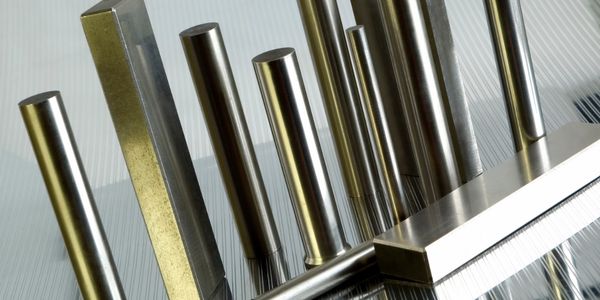
Case Study
RobotStudio Case Study: Benteler Automobiltechnik
Benteler has a small pipe business area for which they produce fuel lines and coolant lines made of aluminum for Porsche and other car manufacturers. One of the problems in production was that when Benteler added new products, production had too much downtime.