公司规模
Large Corporate
地区
- America
国家
- United States
产品
- Tableau
- Trifacta
- Hortonworks Hadoop
技术栈
- Tableau Server
- Tableau Desktop
- Microsoft Access
实施规模
- Enterprise-wide Deployment
影响指标
- Productivity Improvements
- Cost Savings
技术
- 分析与建模 - 实时分析
- 平台即服务 (PaaS) - 数据管理平台
适用行业
- 食品与饮料
- 零售
适用功能
- 销售与市场营销
- 商业运营
用例
- 供应链可见性(SCV)
- 补货预测
- 需求计划与预测
服务
- 数据科学服务
- 系统集成
关于客户
PepsiCo is a multinational food, snack, and beverage corporation headquartered in Harrison, New York, in the hamlet of Purchase. PepsiCo's product mix as of 2015 based on net revenue consists of 53 percent foods, and 47 percent beverages. On a worldwide basis, the company's current products lines include several hundred brands that in 2009 were estimated to have generated approximately $108 billion in cumulative annual retail sales. The company operates in more than 200 countries and territories around the world. PepsiCo’s Collaborative Planning, Forecasting, and Replenishment (CPFR) team provides data and analyses that enable effective retail sales management. The team also collaborates with large retailers to supply the right quantities of product for their warehouses and stores.
挑战
PepsiCo’s Collaborative Planning, Forecasting, and Replenishment (CPFR) team faced the challenge of reconciling disparate data from various sources, including warehouse inventory, store inventory, and point-of-sale inventory. Each customer had their own data standards, which didn’t correspond with each other or PepsiCo’s system. This made data wrangling a challenge and reports could take months to generate. The team primarily relied on Excel for analysis, creating large quantities of messy data. And the team had no efficient way to spot errors, leading to potentially costly outcomes. For example, a missing product from a report could result in inaccurate forecasts and lost revenue. The CPFR team needed a way to wrangle large quantities of disparate data. At the same time, the team needed a visual analysis tool that could help them make the most of PepsiCo data.
解决方案
To bring coherence to the data, PepsiCo turned to Tableau partner, Trifacta. For greater efficiency and scale, PepsiCo implemented Hortonworks Hadoop as a landing and staging environment for this variety of data. Now reports run directly on Hadoop, without involving multiple steps with Access and PepsiCo servers. This process allows analysts to directly manipulate data using Trifacta. Tableau provides PepsiCo with the finishing step: powerful analytics and visualizations, helping the business make sense of volumes of data. PepsiCo analysts share relevant Tableau workbooks with management over Tableau Server. The combined use of Tableau and Trifacta helps the CPFR team drive the business forward, increasing visibility into customer orders. Trifacta’s visual profiling capabilities and Tableau’s advanced visual analytics allow the team to easily identify gaps and get ahead of larger issues.
运营影响
数量效益
Case Study missing?
Start adding your own!
Register with your work email and create a new case study profile for your business.
相关案例.

Case Study
The Kellogg Company
Kellogg keeps a close eye on its trade spend, analyzing large volumes of data and running complex simulations to predict which promotional activities will be the most effective. Kellogg needed to decrease the trade spend but its traditional relational database on premises could not keep up with the pace of demand.
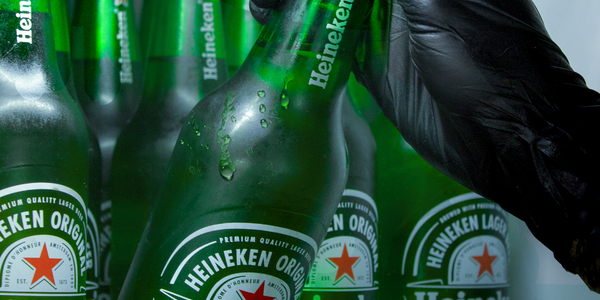
Case Study
HEINEKEN Uses the Cloud to Reach 10.5 Million Consumers
For 2012 campaign, the Bond promotion, it planned to launch the campaign at the same time everywhere on the planet. That created unprecedented challenges for HEINEKEN—nowhere more so than in its technology operation. The primary digital content for the campaign was a 100-megabyte movie that had to play flawlessly for millions of viewers worldwide. After all, Bond never fails. No one was going to tolerate a technology failure that might bruise his brand.Previously, HEINEKEN had supported digital media at its outsourced datacenter. But that datacenter lacked the computing resources HEINEKEN needed, and building them—especially to support peak traffic that would total millions of simultaneous hits—would have been both time-consuming and expensive. Nor would it have provided the geographic reach that HEINEKEN needed to minimize latency worldwide.
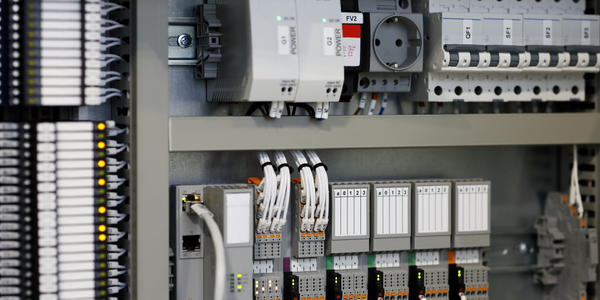
Case Study
Improving Production Line Efficiency with Ethernet Micro RTU Controller
Moxa was asked to provide a connectivity solution for one of the world's leading cosmetics companies. This multinational corporation, with retail presence in 130 countries, 23 global braches, and over 66,000 employees, sought to improve the efficiency of their production process by migrating from manual monitoring to an automatic productivity monitoring system. The production line was being monitored by ABB Real-TPI, a factory information system that offers data collection and analysis to improve plant efficiency. Due to software limitations, the customer needed an OPC server and a corresponding I/O solution to collect data from additional sensor devices for the Real-TPI system. The goal is to enable the factory information system to more thoroughly collect data from every corner of the production line. This will improve its ability to measure Overall Equipment Effectiveness (OEE) and translate into increased production efficiencies. System Requirements • Instant status updates while still consuming minimal bandwidth to relieve strain on limited factory networks • Interoperable with ABB Real-TPI • Small form factor appropriate for deployment where space is scarce • Remote software management and configuration to simplify operations
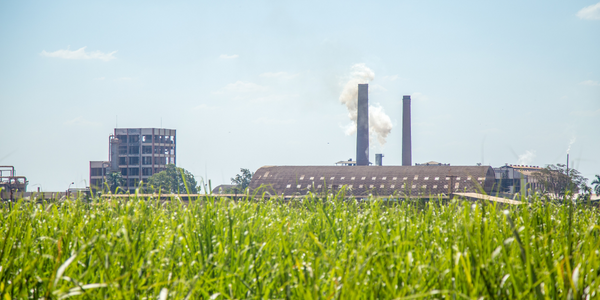
Case Study
Energy Management System at Sugar Industry
The company wanted to use the information from the system to claim under the renewable energy certificate scheme. The benefit to the company under the renewable energy certificates is Rs 75 million a year. To enable the above, an end-to-end solution for load monitoring, consumption monitoring, online data monitoring, automatic meter data acquisition which can be exported to SAP and other applications is required.
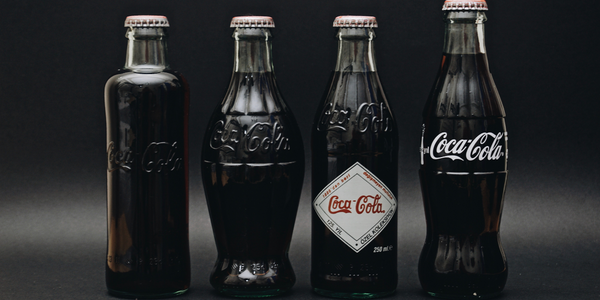
Case Study
Coca Cola Swaziland Conco Case Study
Coco Cola Swaziland, South Africa would like to find a solution that would enable the following results: - Reduce energy consumption by 20% in one year. - Formulate a series of strategic initiatives that would enlist the commitment of corporate management and create employee awareness while helping meet departmental targets and investing in tools that assist with energy management. - Formulate a series of tactical initiatives that would optimize energy usage on the shop floor. These would include charging forklifts and running cold rooms only during off-peak periods, running the dust extractors only during working hours and basing lights and air-conditioning on someone’s presence. - Increase visibility into the factory and other processes. - Enable limited, non-intrusive control functions for certain processes.